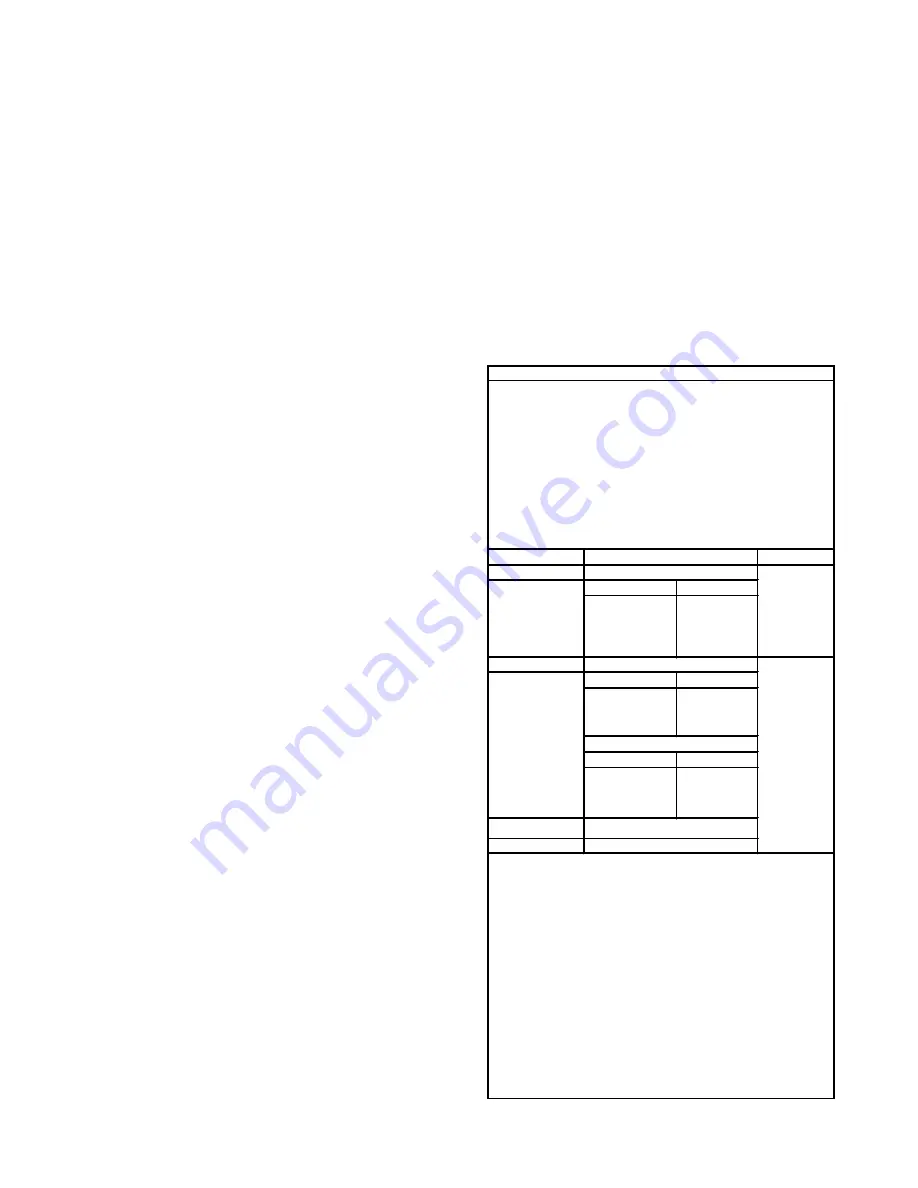
19
I.B. 8926-1A
Part 8
INSPECTION PRIOR TO ENERGIZING
1. Before energizing the motor control center
(MCC), conduct a thorough inspection to make
certain that all foreign materials such as tools,
scraps of wire and other debris are removed
from all units and the structure. Remove any
accumulation of dust and dirt with a vacuum
cleaner.
2. All circuit connections are tightened at time of
assembly by power-driven tools with controlled
torque. However, the vibrations experienced in
transit may loosen some of these connections.
Check at least 10% of the total connections for a
tight connection.
Should this spot-check
reveal some loose connections, it will be
necessary to check all connection points.
The connections to be checked include bus
hardware, circuit breaker and switch terminals,
contactor and relay terminals and terminal
blocks. Always check the incoming line
connections. Tighten to the torque values shown
in Tables 8-1.
3. Remove all blocks or other temporary holding
means used for shipment from all component
devices in the MCC interior.
4. Check the enclosure to see that it has not been
damaged so as to reduce electrical spacings.
5. Compare all circuits for agreement with the
wiring diagrams which accompany the MCC. Be
sure that each motor is connected to its intended
starter.
6. Make certain that field wiring is clear of live
busses and physically secured to withstand the
effects of fault current.
7. Check to determine that all grounding
connections are made properly.
8. Check all devices for damage. Make all
necessary repairs or replacements, prior to
energizing.
9. Manually exercise all switches, circuit breakers,
and other operating mechanisms to make
certain that they are properly aligned and
operate freely.
10. Test any ground-fault protection systems that
were furnished.
11. Set any adjustable current and voltage trip
mechanisms to the proper values.
12. Ensure that overload relay heater elements are
installed and selected to the full-load current
shown on the nameplate of each motor.
13. Install power circuit fuses in the fusible switches
in accordance with NEC application
requirements. Make sure that fuses are
completely inserted in the clips provided. Do not
attempt to defeat the rejection feature on the
fuse clip, when provided.
14. Do not operate a current transformer with its
secondary circuit open. Insure current
transformer is connected to a load, or a
secondary shorting bar is installed.
15. To prevent possible damage to equipment or
injury to personnel, check to insure that all parts
and barriers that may have been removed
during wiring and installation have been properly
reinstalled.
Coil Leads……………………………………………. …….8 lb.-in.
Relays……………………………………………………
…….8 lb.-in.
Push Buttons……………………………………….. …….8 lb.-in.
Control Fuse Blocks……………………………………
…….8 lb.-in.
Auxiliary Contacts………………………………………….8 lb.-in.
Control Wiring Terminal Blocks
Side Mounted Lug/Compression………………… …....9 lb.-in.
Rail Mounted Lug Type…………………………….…...12 lb.-in.
Rail Mounted Compression Type………………….
…...18 lb.-in.
Using Overload
Catalog Number
Conductors
C306DN3
Wire size (AWG) Torque (lb.-in.)
14-10
35
8
40
6 - 4
45
3 - 2
50
For Starters
Wire size (AWG) Torque (lb.-in.)
8
40
6 - 4
45
3 - 2
50
Socket Size (In.) Torque (lb.-in.)
3/16
120
1/4
200
5/16
250
Size N and Size 4
Size 5 and Size 6
30 Amp Fuse Assy………………………………… ……25 lb.-in.
60 Amp Fuse Assy………………………………… ……50 lb.-in.
100 Amp Fuse Assy………………………………………50 lb.-in.
200 Amp Fuse Assy………………………………. …..300 lb.-in.
400 Amp Fuse Assy………………………………. …..300 lb.-in.
600 Amp Fuse Assy………………………………. …..300 lb.-in.
#2/0-350 MCM…………………………………….. …..360 lb.-in.
#2/0-650 MCM…………………………………….. …..360 lb.-in.
#2/0-750 MCM…………………………………….. …..500 lb.-in.
500-1000 MCM…………………………………….. …..600 lb.-in.
All………………………………….. ………….275 lb.-in.(23lb.-ft.)
20 lb.-in.
BREAKERS-
Refer to Torque Values on Breaker Case
Incoming Line Lugs:
Bus Bolts:
Size 3
Socket Head Screw
275 lb.-in.
500 lb.-in.
Use 75
Degrees C
copper or
aluminum
conductors
Slotted Head Screw
Fused Switches:
TABLE 8-1 DRIVING TORQUE
Control Wiring:
Power Wiring: Starters
C306GN3 and
size 2 Contactor
Tightening Torque - Load Side
Use 75
Degrees C
copper
conductors
Содержание Freedom 2100 Series
Страница 31: ...31 I B 8926 1A Part 11 PLAN VIEWS...