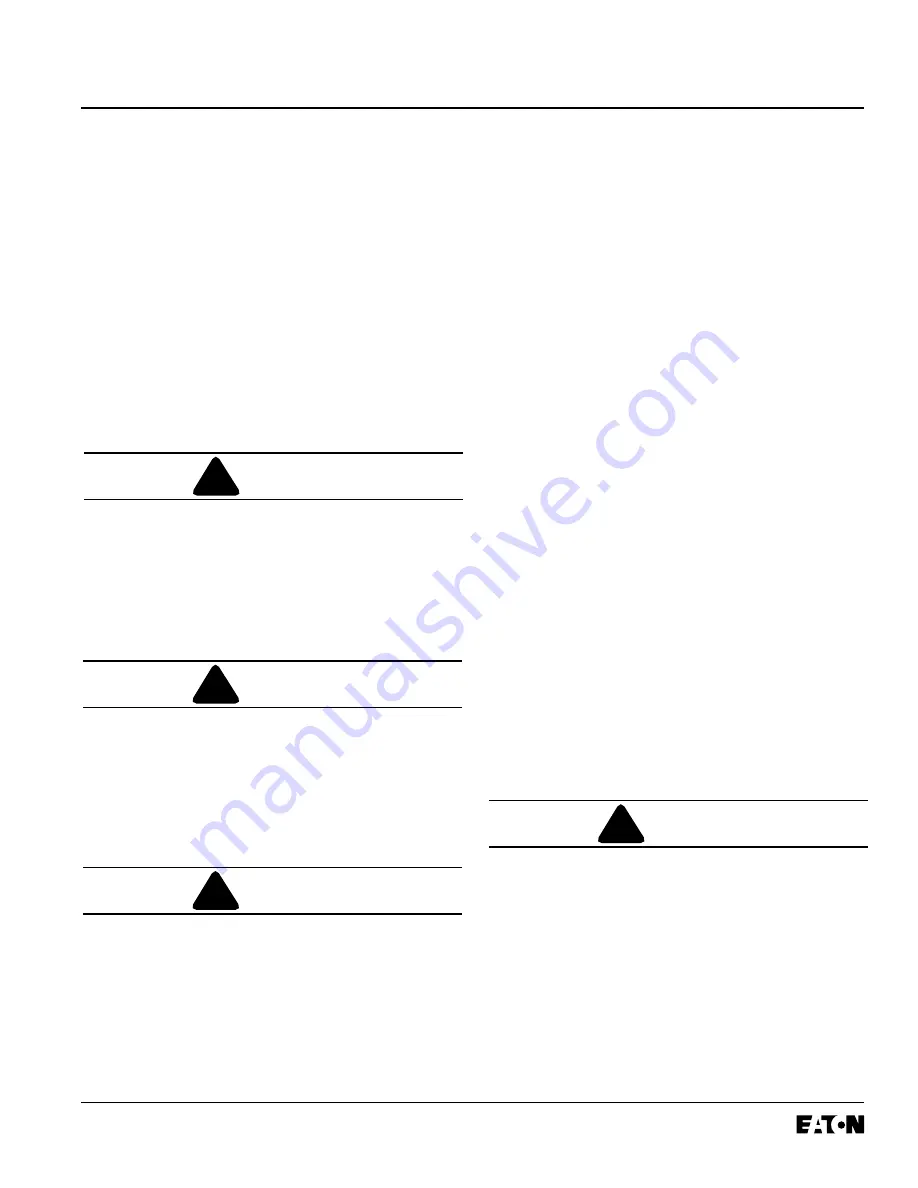
I.B. ATS-SD02
Page 17
Effective 5/98
door and set it aside in a safe place until mounting is
complete.
Step 2: Gently maneuver the switch into its location
using the four lift brackets.
Step 3: Bolt the enclosure to the base. Use separate
cleats (Option 42 only) if Seismic UBC Zone 4
certification is desired (Figure 4-5), and secure
with 1/2-13 UNC Grade 5 hex bolts.
Step 4: Tighten bolts to 50 ft-lbs (68 Nm).
Step 5: Double check to ensure that all packing and
shipping material has been removed.
4.4 POWER CABLE CONNECTIONS
POWER CONDUCTORS MAY HAVE VOLTAGE PRE-
SENT THAT CAN CAUSE SEVERE PERSONAL
INJURY OR DEATH. DE-ENERGIZE ALL POWER OR
CONTROL CIRCUIT CONDUCTORS TO BE CON-
NECTED TO THE TRANSFER SWITCH EQUIPMENT
BEFORE BEGINNING TO WORK WITH THE CON-
DUCTORS AND/OR TERMINATING THEM TO THE
EQUIPMENT.
USE OF CABLE LUGS NOT DESIGNED FOR THE
TRANSFER SWITCH MAY CAUSE HEATING PROB-
LEMS. BREAKER LUGS ONLY MOUNT TO THE
BREAKER, WHILE TRANSFER SWITCH LUGS
MOUNT TO BOTH THE BREAKER AND THE BUS-
BAR BEHIND THE BREAKER. FOR INSTALLATION
INSTRUCTIONS, REFER TO THE INSTRUCTION
LEAFLET SUPPLIED FOR THE SPECIFIC LUGS.
TO HELP PREVENT COMPONENT DAMAGE OR
FUTURE MALFUNCTIONS, USE EXTREME CARE TO
KEEP CONTAMINANTS OUT OF THE TRANSFER
SWITCH EQUIPMENT WHEN MAKING POWER
CABLE CONNECTIONS.
Proceed with the following steps:
Step 1: Verify that the line and load cables comply with
applicable electrical codes.
Step 2: Verify that transfer switch rated current and
voltage (see identification plate on the intelli-
gence panel of transfer switch) agree with sys-
tem current and voltage.
Step 3: After the transfer switch is mounted, provide
conduit or cable openings as required. Ensure
that no metal filings contaminate the transfer
switch components.
Step 4: Test all power cables before connecting to the
unit to insure that conductors or cable insulation
have not been damaged while being pulled into
position.
Step 5: Carefully strip insulation from the power cables.
Avoid nicking or ringing of the conductor
strands. Prepare the stripped conductor termi-
nation end by cleaning it with a wire brush. If
aluminum conductors are used, apply an appro-
priate joint compound to the clean conductor
surface area. Refer to Figure 4-3 for approxi-
mate locations of power connections.
Power cables are to be connected to solderless screw
type lugs located on the transfer switch switching
devices. Refer to the separate Customer Wiring
Diagrams supplied with the transfer switch equipment
for power termination. Verify that the lugs supplied will
accommodate the power cables being used. Also verify
that the cables comply with local electrical codes.
Standard transfer switch equipment, as supplied from
the factory, will accommodate the wire sizes shown in
Table 4.1.
IMPROPER POWER CABLE CONNECTIONS CAN
CAUSE EXCESSIVE HEAT AND SUBSEQUENT
EQUIPMENT FAILURE.
Step 6: Tighten cable lugs to the torque identified on
the label affixed to the unit immediately adja-
cent to the lugs.
Step 7: Make necessary connections of options using
wiring diagrams supplied with the unit.
Step 8: Connect engine start wires to the red terminal
blocks marked 51 and 52.
!
WARNING
!
CAUTION
!
CAUTION
!
CAUTION
Содержание ATVISPE31000XSU
Страница 2: ......
Страница 41: ...I B ATS SD02 Page 35 Effective 5 98...
Страница 42: ...I B ATS SD02 Page 36 Effective 5 98...
Страница 43: ......