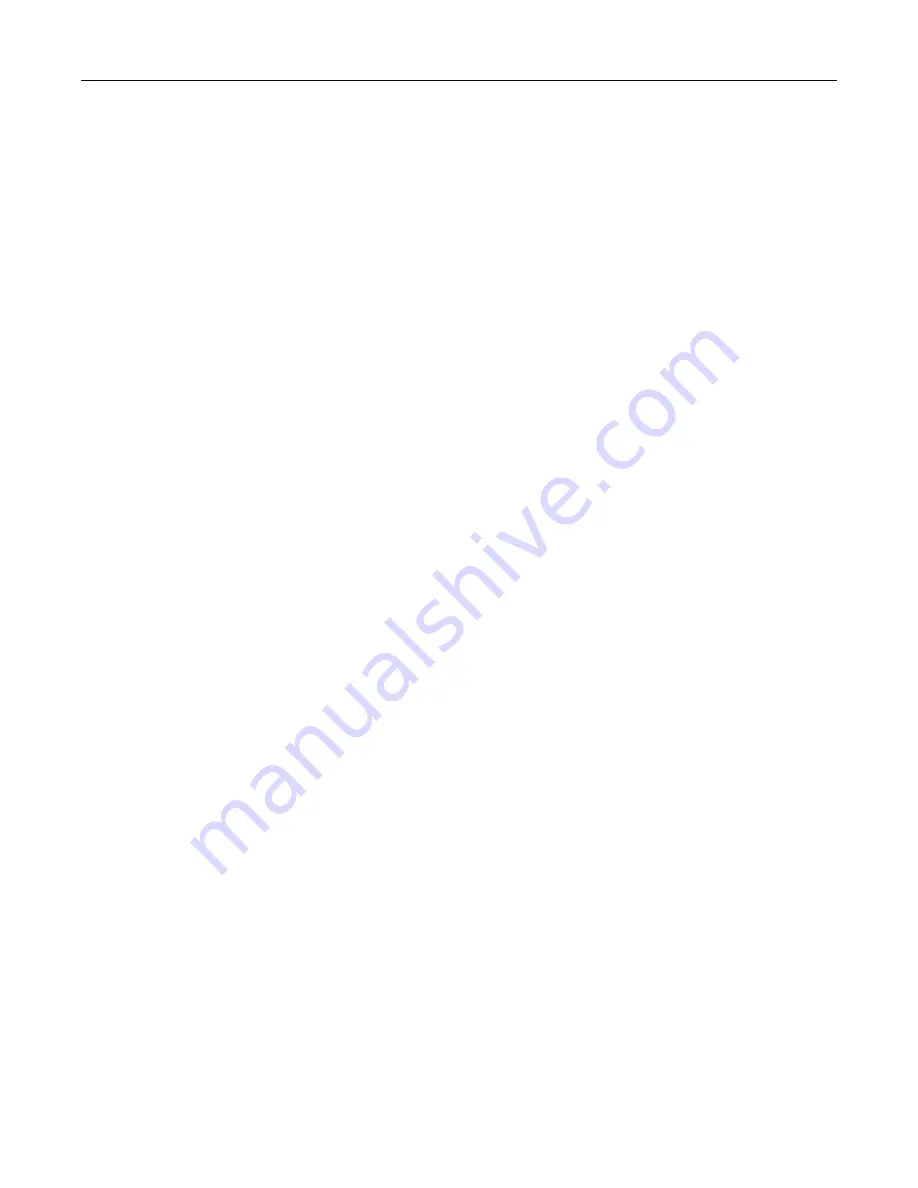
Troubleshooting — 3
Notes
Rev 3-97
* School
UNIVERSAL TROUBLESHOOTING TECHNIQUES
There are some basic procedures which apply to troubleshooting at any level,
whether it be component level circuit board repair or very general system level
service.
Symptom Recognition
The first step in troubleshooting is to determine that a problem really exists. All
too often a problem exists in a system that is never identified and never fixed.
The long term result is an unsatisfied customer. On the other hand, a system
operator may expect a certain result and feels that there is something wrong
with the system when he does not get that result. Recognizing symptoms of an
actual problem may be very obvious or may be quite subtle. In either case a
solid understanding of how an IQ System operates is critical to determining if
a problem is real. Symptom recognition, then, is the determination that a
problem exists by virtue of the system response being different from the
expected response.
Example: Amplifiers in equipment room #1 do not respond to commands sent
from the computer.
Symptom Elaboration
Once you decide that a problem exists you need to try to find out as much about
the problem as possible by examining the nature of the symptoms. This step
in the process often involves some very basic testing to get you looking in the
right general area for the exact problem. Specifically is the process of defining
the exact nature of the problem.
Example: When taking a Roll Call all components appear except those in
equipment room #1.
Probable Faulty Block
Once you have gathered all the information you can about the specific nature
of the problem you can usually determine where to start looking. This step often
involves checking your symptoms against system documentation.
Example: Examine system prints and find that component in equipment room
#1 are all on Crown Bus loop 3 and they are the only components on loop 3.
Problem is likely to be a communication problem somewhere in loop 3.
Probable Faulty Function
At this point it is often necessary to use your troubleshooting tools to break the
problem down until you find out exactly what the problem is.
Example: Visually inspect cable connections for loop 3 at the interface and in
the equipment room. You locate a Crown Bus cable that has been pulled loose
from a PIP data input at Amplifier 13. An alternate method of testing if the DOS
software is used is to run a SEARCH on loop 3 using the IQ software. It would
reveal a “Break on loop 3 before Amplifier 13.” This would tell you where to go
to physically look for a cable problem.
Problem Verification & Repair
The final step once the problem is found is to fix it and test the system. There
have been times in every technician’s life where they think they have found the
problem, performed a repair, and found that something else was wrong. It is