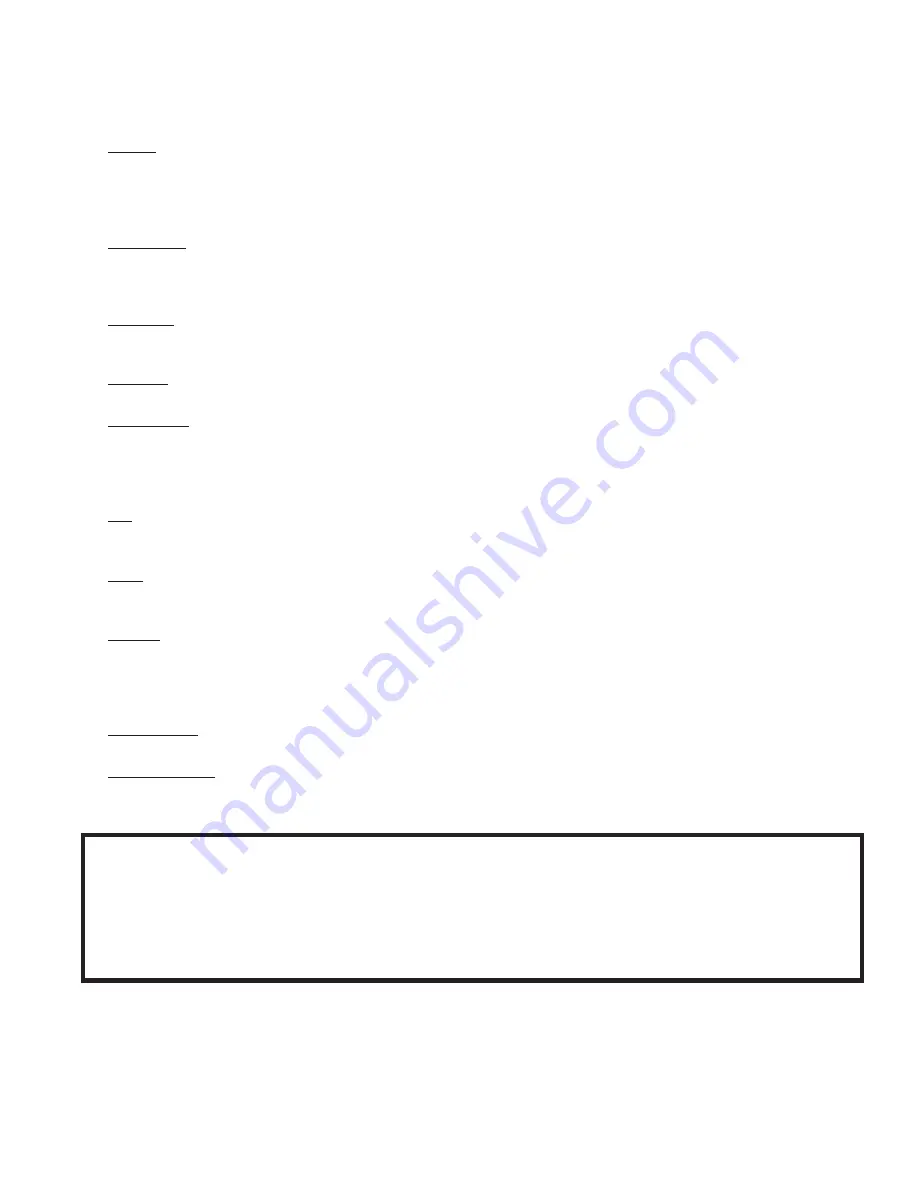
39
XIV Trouble Shooting
A. Combustion
1)
Nozzles - The selection of the nozzle supplied with this boiler is the result of extensive testing to obtain the best flame shape
and efficient combustion. Other brands of the same spray angle and pattern may be used but may not perform at the expected
level of CO
2
and smoke. Nozzles are delicate and should be protected from dirt and abuse. Nozzles are mass-produced and
can vary from sample to sample. For all of those reasons a spare nozzle should be part of a service technician’s replacement
parts inventory.
2)
Flame Shape - As seen for the observation port, the flame should appear straight with no sparklers rolling up toward the
crown of the chamber. If the flame drags to the right or left, sends sparklers upward or makes wet spots on the chamber
walls, the nozzle should be replaced. If the condition persists look for fuel leaks, air leaks, water or dirt in the fuel as
described below.
3)
Fuel Leaks - Any fuel leak between the pump and the nozzle will be detrimental to good combustion results. Look for wet
surfaces in the air tube, under the ignitor and around the air inlet. Any such leaks should be repaired as they may cause
erratic burning of the fuel and in the extreme case may become a fire hazard.
4) Air Leaks
- Any such leaks should be repaired as they may cause erratic burning of fuel and in extreme cases may become a
fire hazard.
5)
Gasket Leaks - If CO
2
readings between 11.0% and 12.5% with a #1 smoke cannot be obtained in the breeching, or if odors
are observed, look for leaks around the burner mounting gasket, observation door and canopy gasket, or in the breeching
below the point where the flue gas sample is taken. Air leakage into the boiler or breeching can cause low CO
2
readings (the
lower the firing rate, the greater effect an air leak can have on CO
2
readings). Such leaks can also cause flue gas leakage into
the building, resulting in odor complaints.
6) Dirt - The use of a fuel filter is good practice. Accidental accumulation of dirt in the fuel system can clog the nozzle or
nozzle strainer and produce a poor spray pattern from the nozzle. The smaller the firing rate, the smaller the slots in the
nozzle and the more prone to plugging it becomes.
7)
Water
- Water in the fuel in large amounts will stall the fuel pump. Water in the fuel in smaller amounts will cause excessive
wear on the pump. More importantly it chills the flame and causes smoke and unburned fuel to pass through the combustion
chamber and clog the flueways of the boiler.
8) Cold Oil - If the oil temperature near the fuel pump is 40°F or lower, poor combustion or delayed ignition may result. Cold
oil is harder for the nozzle to atomize, thus the oil droplets get larger and travel further creating a longer flame. An outside
fuel tank that is above grade or has fuel lines in a shallow bury is a good candidate for cold oil. The best solution is to bury
the tank and lines deep enough to keep the oil above 40°F. Be sure to follow any state and local codes when burying fuel oil
tanks and/or fuel oil lines.
9) Start-Up Noise - Delayed ignition is the cause of start-up noises. If it occurs recheck for electrode settings, flame shape, air
or water in the fuel lines.
10) Shut Down Noise - If the flame runs out of air before it runs out of fuel, an after burn with noise may occur. That may be the
result of a faulty cut-off valve in the fuel pump, or it may be air trapped in the nozzle line. It may take several firing cycles
for that air to be fully vented through the nozzle. Water in the fuel or poor flame shape can also cause shut down noises.
TEST PROCEDURE FOR FUEL SIDE PROBLEMS
A good test for isolating fuel side problems is to temporarily connect the burner to a small alternate
source of clean, fresh, warm #2 fuel oil located near the burner. If the burner runs successfully when
drawing out of the auxiliary pail then the problem is isolated to the fuel or fuel lines being used on the
installation.
Содержание TWZ Series
Страница 2: ......
Страница 10: ...8 FIGURE 4 1 INSTALLATION OVER A COMBUSTIBLE FLOOR FIGURE 4 0 CLEARANCES...
Страница 27: ...25 FIGURE 10 0 CONNECTIONS DIAGRAM BOILERS WITH OR LESS TANKLESS HEATER...
Страница 28: ...26 FIGURE 10 1 CONNECTIONS DIAGRAM FOR BURNER PRIMARY CONTROLS Carlin 40200 Beckett 7505 Riello 530SE...
Страница 47: ...45...
Страница 49: ...47...
Страница 50: ...48 SERVICE RECORD DATE SERVICE PERFORMED...
Страница 51: ...49 Notes...