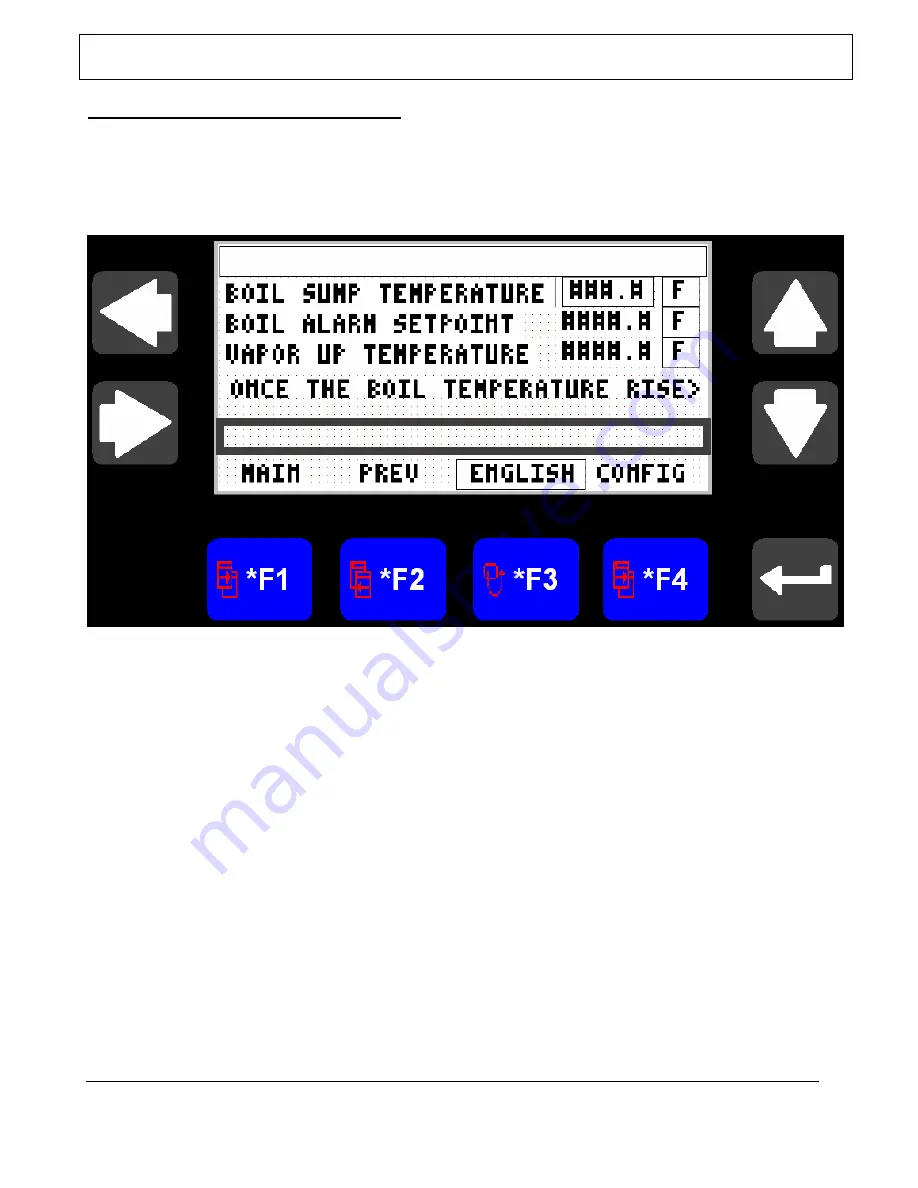
Forward Technology – a Crest Group Company
Operation and Maintenance Manual for F-100 Cleaning System
F-100 Manual Rev H
Non-Flammable
34
PROCESS PARAMETERS: OEM (Continued)
WARNING: All of these settings are Factory set and should not be changed unless
authorized by Forward Technology Inc.
OEM: FTI
Figure 27: FTI
Right Arrow = Not Used
Left Arrow = Not Used
Up Arrow = Select Numeric Entry
Down Arrow = Select Numeric Entry
F1 = Go To Main Menu
F2 = Go To Previous Screen (Alarm History)
F3 = Change Display Temperature English/Metric
F4 = Go To Configuration Screen, Not Used, FTI Service ONLY
WARNING: All of these settings are Factory set and should not be changed unless authorized by Forward
Technology Inc.