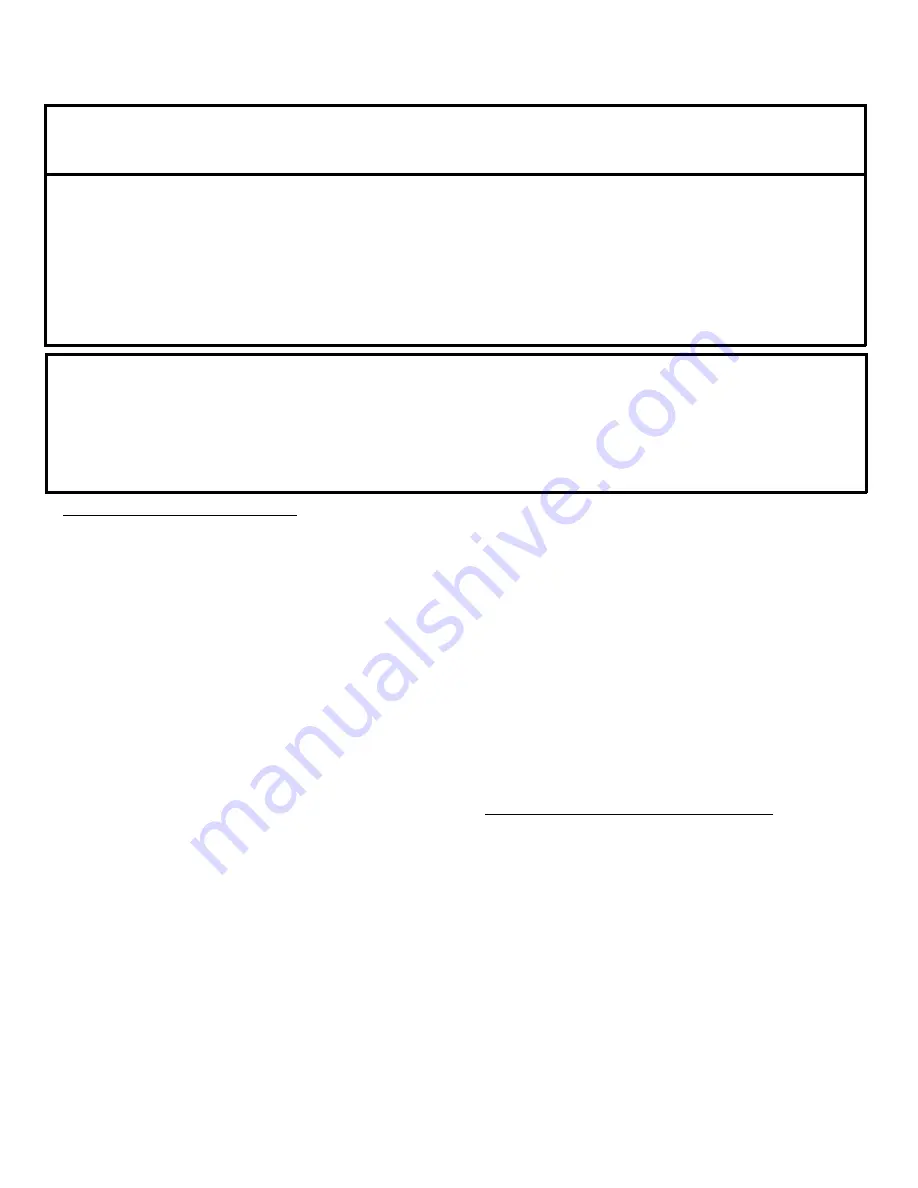
MODEL
HP
VOLT
PH
RPM
NEMA
FULL LOCKED
CORD
CORD
CORD
EMERSON
G.E.
NO.
(Nom) CODE
LOAD
ROTOR
SIZE
TYPE
OD
WINDING
WINDING
AMPS
AMPS
RESISTANCE
RESISTANCE
MAIN/START
MAIN/START
STEP512L
0.5
115
1
3450
F
12.0
55.0
14/3
SJTOW-A
0.390
1.70--16.6
STEP522L
0.5
230
1
3450
F
6.0
11.5
14/3
SJTOW-A
0.390
9.32--10.14
STEP532L
0.5
230
3
3450
G
3.4
7.8
14/4
SO
0.600
8.58--
STEP542L
0.5
460
3
3450
G
1.7
3.9
14/4
SO
0.600
34.32--
STEP552L
0.5
575
3
3450
G
1.4
3.1
14/4
SO
0.600
53.62--
STEP1022L
1.0
230
1
3450
B
8.0
13.8
14/3
SJTOW-A
0.390
2.83--15.14
STEP1032L
1.0
230
3
3450
K
5.4
21.3
14/4
SO
0.600
4.34--
STEP1042L
1.0
460
3
3450
K
2.8
10.7
14/4
SO
0.600
17.36--
STEP1052L
1.0
575
3
3450
K
2.3
8.6
14/4
SO
0.600
27.12--
Winding Resistance
±
5%, Pump rated for operation at
±
10% voltage at motor.
Standard Units:
(Optional - Moisture sensor & Power cable for 1 phase is 14/5 SO, 0.670 O.D,
replaces
standard SJTOW-A cable.)
(Optional - Temperature sensor cable for 3 phase models is 14/2 SOW, .530 O.D.)
(Optional - Moisture & Temperature sensor cable for 3 phase models is 18/5 SOW, 0.476 OD.)
CSA Listed Units:
(Optional - CSA Listed Moisture Sensor Cable for 1 phase is 14/2 SOW, 0.530 O.D.)
(Optional - CSA Listed Temperature sensor cable for 3 phase models is 14/2 SOW, .530 O.D.)
(Optional - CSA Listed Moisture & Temperature sensor cable for 3 phase models is 18/5 SOW, 0.476 OD.)
SECTION: D START-UP OPERATION
D-1) Check Voltage and Phase:
Before operating pump, compare the voltage and phase information
stamped on the pump identification plate to the available power.
D-2) Check Pump Rotation:
Before putting pump into service for the first time, the motor rotation
must be checked. Improper motor rotation can result in poor pump
performance and can damage the motor and/or pump. To check the
rotation, suspend the pump freely, momentarily apply power and
observe the "kickback". "Kickback" should always be in a
counter-clockwise direction as viewed from the top of the pump
motor housing.
D-2.1) Incorrect Rotation for Three-Phase Pumps:
In the event that the rotation is incorrect for a three-phase installation,
interchange any two power cable leads at the control box.
DO NOT
change leads in the cable housing in the motor. Recheck the
"kickback" rotation again by momentarily applying power.
D-2.2) Incorrect Rotation for Single-Phase Pumps:
In the unlikely event that the rotation is incorrect for a single phase
pump, contact a Barnes Pumps Service Center.
D-3) Start-Up Report:
Included at the end of this manual are two start-up report sheets,
these sheets are to be completed as applicable. Return one copy to
Barnes Pumps, Inc. and store the second in the control panel or with
the pump manual if no control panel is used. It is important to record
this data at initial start-up since it will be useful to refer to should
servicing the pump be required in the future.
D-3.1) Identification Plate:
Record the numbers from the pump identification plate on both
START-UP REPORTS provided at the end of the manual for future
reference.
D-3.2) Insulation Test:
Before the pump is put into service, an insulation (megger) test
should be performed on the motor. The resistance values (ohms) as
well as the voltage (volts) and current (amps) should be recorded
on the start-up report.
D-3.3) Pump-Down Test:
After the pump has been properly wired and lowered into the basin,
sump or lift station, it is advisable to check the system by filling with
liquid and allowing the pump to operate through its pumping cycle.
The time needed to empty the system, or pump-down time along
with the volume of water, should be recorded on the start-up report.
SECTION E: PREVENTATIVE MAINTENANCE
As the motor is oil filled, no lubrication or other maintenance is
required, and generally Barnes Pumps will give very reliable service
and can be expected to operate for years of normal sewage pumping
without failing. However, as with any mechanical piece of equipment
a preventive maintenance program is recommended and suggested
to include the following checks:
1) Inspect motor chamber for oil level and contamination and
repair as required per section F-1.
2) Inspect impeller and body for excessive build-up or clogging and
repair as required per section F-2.
3) Inspect seal for wear or leakage and repair as required per
section F-3.
4) Inspect motor and bearings and replace as required per
section F-4.
7
Содержание STEP1042L
Страница 16: ...Fig 9 16 ...
Страница 17: ...Fig 10 17 ...