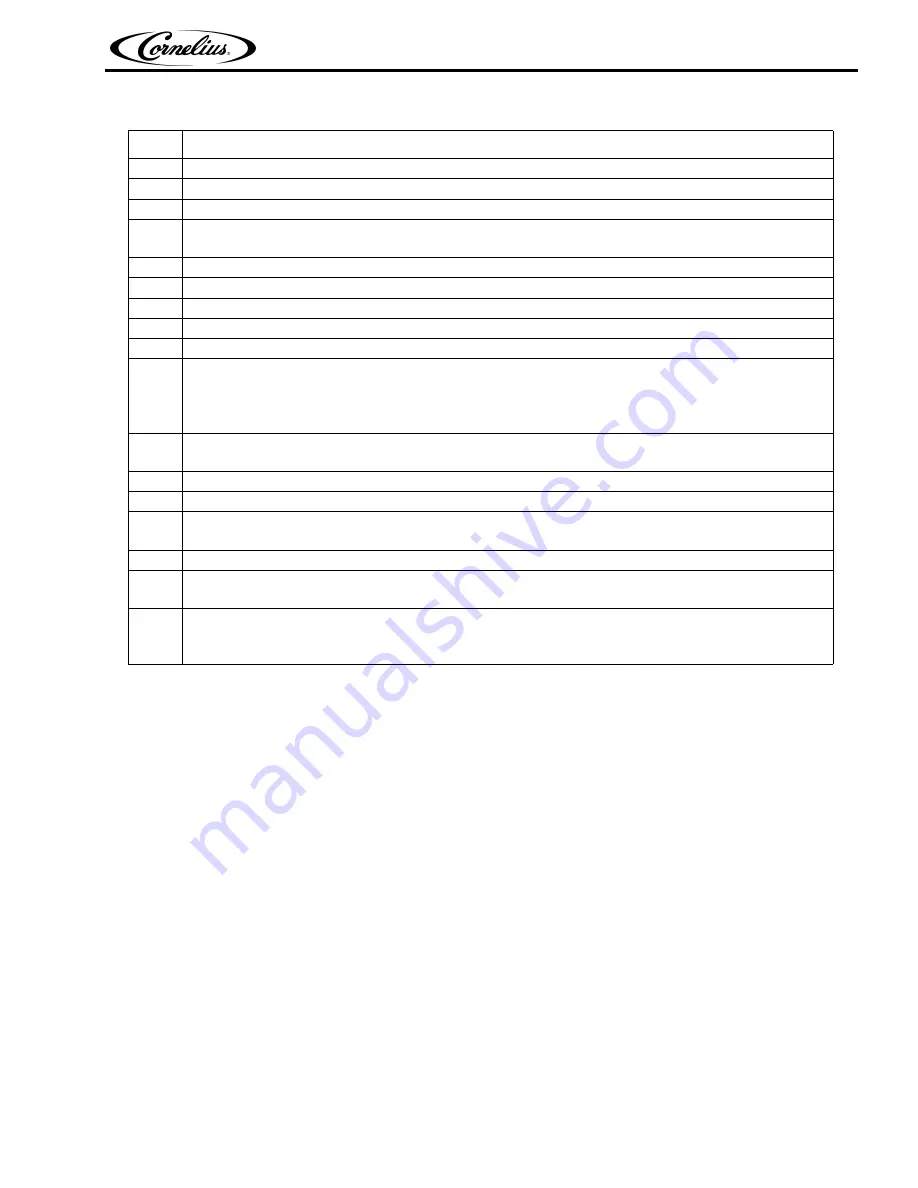
Viper Operator’s Manual
© 2022, Marmon Foodservice Technologies Inc.
- 15 -
Publication Number: 620073146OPR
NOTE:
Use Dow-Corning DC-111 (P/N 321471000) light grade silicone lubricant to lubricate the O-rings.
Servicing SPH Dispensing Valves
Sanitizing the System
The syrup systems should be sanitized every 180 days by a qualified service technician following the sanitizer manufac-
turer’s recommendations or when changing syrup types.
The sanitizing process consists of emptying the barrel, washing the lines and barrel, cleaning the BIB connectors, rinsing
and refilling the system.
NOTE: Sanitizing should only be performed by qualified service technicians.
Suggested Sanitizers
KAY-5® Sanitizer/Cleaner (100 PPM)
Mix one packet of KAY-5® Sanitizer/Cleaner per 2.5 gallons of tap water [70°-100°F (24°-35°C)] according to manufacturer's
instructions to ensure 100 PPM of available chlorine.
Household Bleach (200 PPM)
For 6% Sodium Hypochlorite bleach, mix 2.5 fl oz (75mL) in 5 gallons of tap water [70°-100°F (24°-35°C)]. For 5.25% Sodium
Hypochlorite bleach, mix 2.2 fl oz (66mL) of bleach in 5 gallons of tap water [75°-95°F (24°-35°C)]. This will ensure a bleach
solution of 200 PPM of available chlorine.
5.
Unscrew the relief valve from the faceplate.
6.
Disassemble the dispensing valve (see Figure 10).
7.
Remove ice ball grate from faceplate, if applicable
8.
Remove the two screws and hold-down plates securing the spring housing to the dispensing valve body, then remove
the housing.
9.
Remove the torsion spring from the dispensing valve.
10.
Remove the knob, spring, sleeve, and lever from the dispensing valve.
11.
Remove spring fitting from dispensing valve.
12.
Press the valve with the caged O-ring, down and out of the dispensing valve body.
13.
Carefully remove the caged O-ring from the valve.
14.
Wash all the parts in warm water. Remove all traces of syrup and lubricant, especially from the faceplate, o-rings, ice
ball grate (if applicable), and dispensing valve. If parts are excessively coated, wipe clean with a paper towel to remove
excess syrup and lubricant, especially from caged o-ring and dispensing valve. Use a brush (provided with the unit) to
clean the faceplate relief valve passages.
15.
Submerge all the parts in a sanitizing solution according to the suggested sanitizers above for 10 minutes (no more
than 15 min).
16.
Remove the parts from the sanitizing solution and place them on clean paper towels.
17.
Assemble the dispensing valve. Rinse them with warm water, and place them on clean paper towels.
18.
Lubricate the caged o-ring. Carefully install the caged o-ring onto the valve from the straight end (opposite tapered
end). Lubricate the grooves that the o-ring rides to fill in all void areas around the o-ring.
19.
Carefully install the valve with the caged o-ring in the dispensing valve body.
20.
Install the spring fitting, knob and lever parts, torsion spring and spring housing assembly by reversing the removal
procedure. Do not tighten down the hold-down plates securing the spring housing at this time.
21.
After re-installing the faceplate, turn the dispensing valve spring housing to the left (counterclockwise) to put tension
on the tension spring. Apply just enough tension so that the dispense valve shaft returns to the closed position after
release. Do not overtighten. Overtightening results in a high activation force on the valve.
Table 12.
Step
Action
Содержание 621257142
Страница 26: ...Cornelius Inc www cornelius com ...