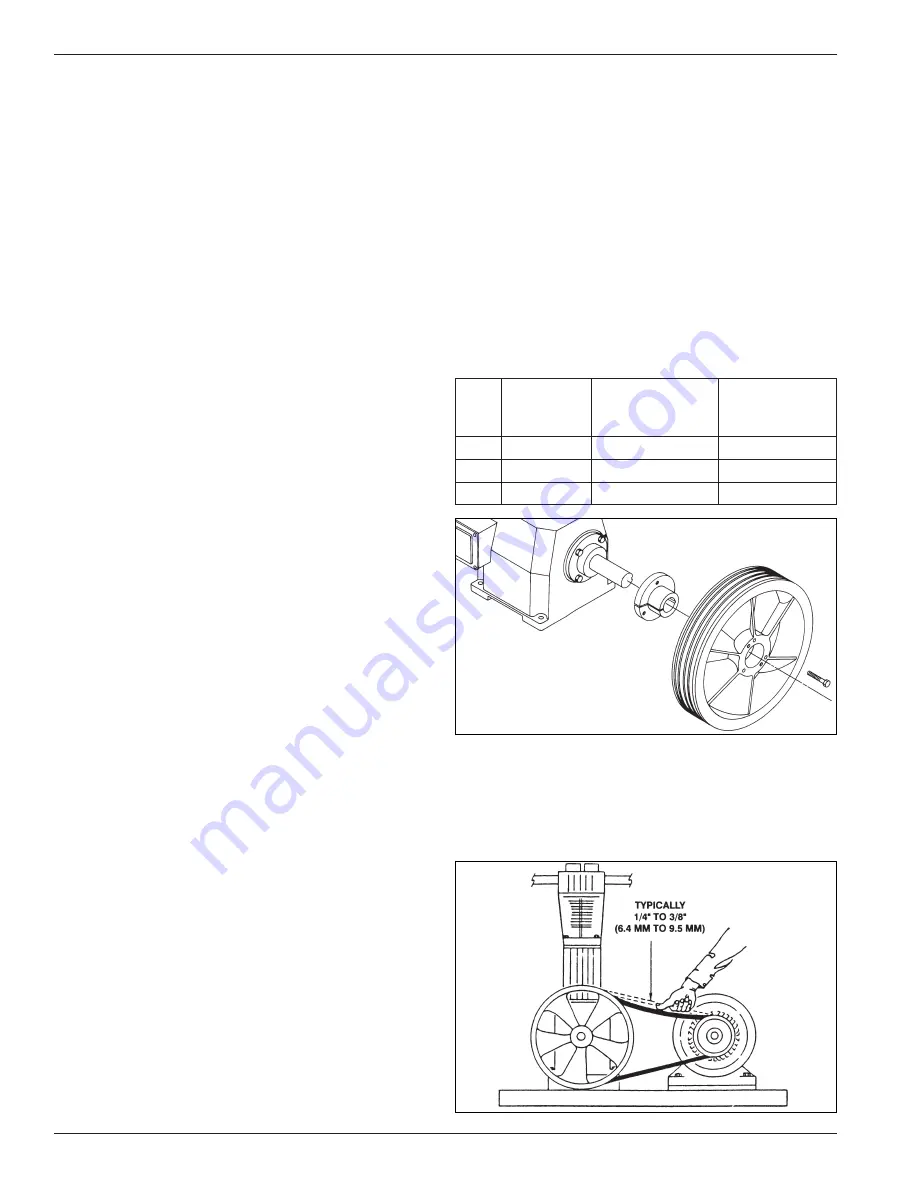
Less than 90% of the relief valve set point pressure.
Less than the maximum operating pressure of the
compressor.
Midpoint of the pressure switch range.
5.
Vibration Switch:
Shuts down the unit if vibration
becomes excessive. Recommended for units mounted
to a portable skid.
1.9 Compressor Cooling
This compressor has a water-cooled head and cylinder.
There is one water inlet connection on the cylinder and
two water outlet connections on the head. The owner
of the compressor is responsible for the inlet and
outlet water connections.
The cylinder has one water jacket while the head has
three water jackets. See Figure 1.9 for details.
when installation is complete. Always check the flywheel
runout before startup and readjust if it exceeds the value
listed in Appendix B.
Hub
Size
Diameter
in. (cm)
Bolt Torque
Ft-lb (kg-meter)
Set Screw
Torque Ft-lb
(kg-meter)
SF
4.625 (11.7)
12-18 (1.7–2.5)
22 (3.1)
E
6.0 (15.2)
30-36 (4.1–4.9)
22 (3.1)
J
7.25 (18.4)
75-81 (10.3–11.1)
109 (15.1)
Figure 2.2A: Flywheel installation
Tighten the belts so that they are taut, but not extremely
tight. Consult your V-belt supplier for specific tension
recommendations. Belts that are too tight may cause
premature bearing failure. Refer to figure 2.2B.
Figure 2.2B: Belt tension
NOTE: Read this entire chapter, then proceed with
the startup checklist.
2.1 Inspection After Extended
Storage
If your compressor has been out of service for a long
period of time, you should verify that the cylinder bore
and valve areas are free of rust and other debris. For
valve and/or cylinder head removal instructions, refer to
chapter 4 of this IOM manual.
Drain the oil from the crankcase and remove the
nameplate and crankcase inspection plate. Inspect the
running gear for signs of rust and clean or replace parts
as necessary. Replace the crankcase inspection plate
and fill crankcase with the appropriate lubricant through
the nameplate inspection opening. Squirt oil on the
crossheads and rotate the crankshaft by hand to ensure
that all bearing surfaces are coated with oil.
Rotate unit manually to ensure running gear functions
properly. Replace nameplate and proceed with startup.
2.2 Flywheel and V-belt Alignment
Before working on the drive assembly, be sure that the
electric power is disconnected. When installing new belts,
always make sure the driver and compressor are close
enough together to avoid forcing the belt onto the flywheel.
Improper belt tension and sheave alignment can cause
vibration, excessive belt wear and premature bearing
failures. Before operating your compressor, check alignment
of the V-grooves of the compressor flywheel and driver
sheave. Visual inspection often will indicate if the belts are
properly aligned, but use of a square is the best method.
The flywheel is mounted on the shaft via a split, tapered
bushing and three bolts (see figure 2.2A). These bolts
should be tightened in an even and progressive manner
to the specified torque by the manufacturer. There must
be a gap between the bushing flange and the flywheel
Chapter 2—Starting Up Your Corken Compressor
10