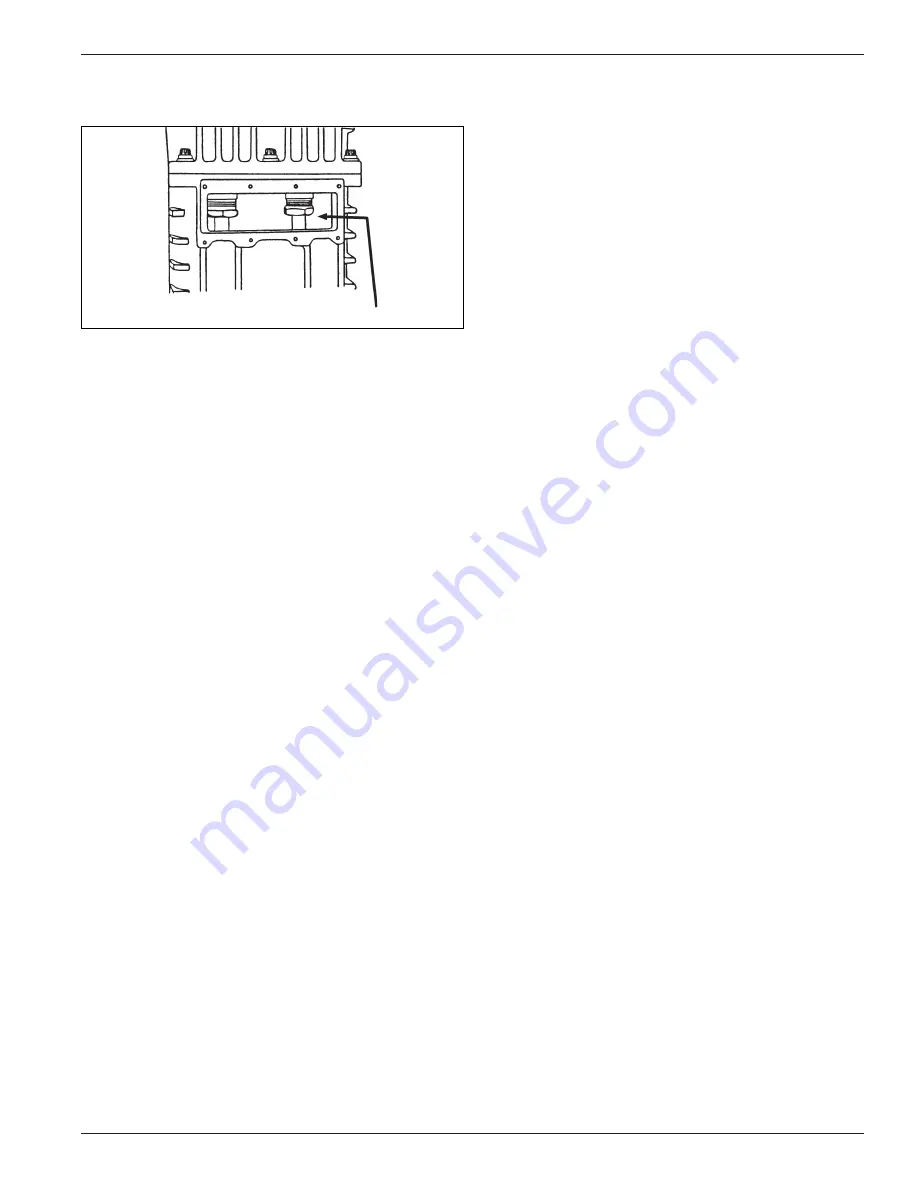
Synthetic lubricants are generally not necessary. Please
consult your lubricant supplier if you are considering the
use of synthetic oil.
Note: Fill crankcase with oil through this opening
Figure 1.5C: Oil filling location
New or rebuilt units should be filled with oil through
the opening behind the compressor nameplate. This
provides excellent lubrication for the crossheads on
initial startup (see Figure 1.5C).
1.6 Purging, Padding, Venting and
Draining of Distance Pieces
The key to leakage control and oil-free operation of Corken
compressors is the distance piece. The distance piece is
integral with the crosshead guide and forms the upper
portion of it. The distance piece is equipped with tapped
holes to allow purging, padding, venting, and draining (see
Figure 1.6). Proper connections to and from these tapped
holes are essential for optimum compressor performance.
Compressors with the A-Style packing arrangement are
shipped with all distance piece connections plugged.
These compressors are used with inlet pressures
above atmospheric pressure.
Corrosive gases should be prevented from entering
the crankcase, since even small amounts of gas
leakage into the crankcase can seriously contaminate
the crankcase oil. To prevent this contamination, the
distance piece may be purged, padded, or vented
using a clean, non-corrosive gas like dry air or nitrogen.
Purging:
Purging of the distance piece controls leakage of process
gas to the atmosphere. Process gas leakage into the
distance piece is quickly diluted by the purge gas and
swept away. The purge gas should be vented to a safe
release area, flare, compressor’s inlet, or treatment
facility, depending on the gas and local regulations.
When purging, it is critical to maintain the proper
pressure loading across each set of packing. The higher
pressure should be on the open side of the “V”, which is
also the side with the spring.
Purging can be performed on all D-Style configurations.
Consult factory for details on specific packing
configurations necessary for your application.
Moisture, oil, or condensate can be removed from the
distance piece with the purge gas by using the lower
distance piece connection (drain location) as the purge
gas outlet connection.
Corken offers purge kits which include the necessary
regulator, valves, fittings, etc. Consult the factory for details.
Padding (Buffering):
If purging is not practical, the distance piece can be
pressurized with a static pressure. This is called padding
or buffering. Padding is done at a pressure above the
compressor’s suction pressure using a clean non-
corrosive gas like dry air or nitrogen. The higher pressure
in the distance piece tends to reduce the process gas
leakage to the atmosphere. A small amount of purge gas
will likely get into the process gas. A pressure regulator
can be used to maintain proper distance piece pressure.
When padding, it is critical to maintain the proper
pressure loading across each set of packing. The higher
pressure should be on the open side of the “V”, which is
also the side with the spring.
Consult factory for details on specific packing
configurations necessary for your application.
Venting:
The distance piece can also simply be vented to an
appropriate release area, flare, or treatment facility. This
is sometimes useful for indoor installations.
Draining:
Since some oil will pass the bottom packing set,
regular draining of the distance piece is essential to
maintain oil-free operation (See Figure 1.6).
Corken
recommends draining the distance piece once a week for
units in continuous-duty operation. Installing a drain cock
to the distance piece drain will help simplify draining of
the distance piece.
Highly Corrosive Gases:
The compressor should be blocked from the system via
valves on the suction and discharge piping, then purged with
dry inert gas before being shut down. Experience has proven
this significantly lowers corrosion damage to the machine.
1.7 Relief Valves
An appropriate relief valve must be installed on the discharge
side of the compressor. Relief valves should be made of a
material compatible with the gas being compressed. Local
7