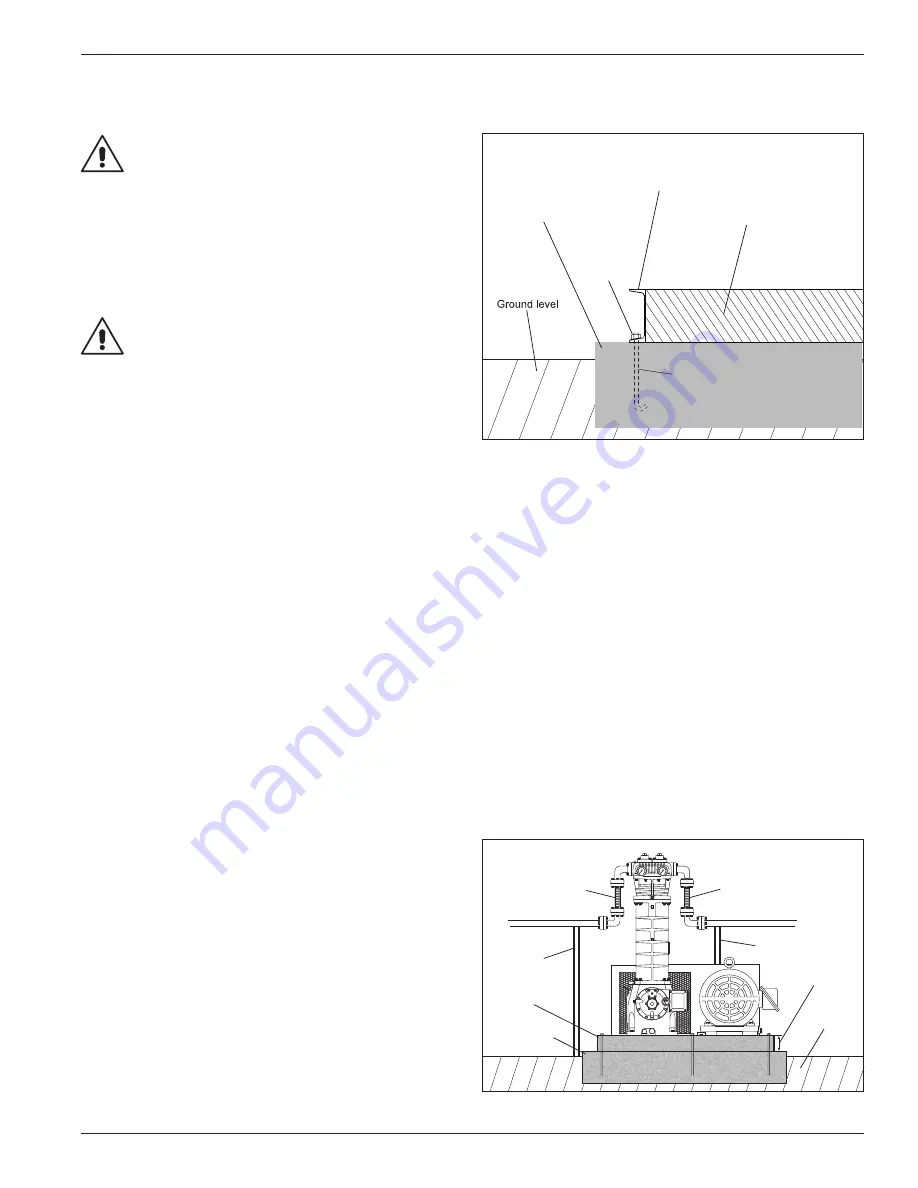
1.1 Location
WARNING
Compressor must be installed in a well
ventilated area.
Corken compressors are designed and manufactured for
outdoor duty. For applications where the compressor will be
subjected to extreme conditions for extended periods such
as corrosive environments, arctic conditions, etc., consult
Corken. Check local safety regulations and building codes
to assure installation will meet local safety standards.
WARNING
Corken compressors handling toxic or
flammable gases such as LPG/NH
3
should be
located outdoors in a well ventilated area. A
minimum of 18 inches (45 cm) clearance between the
compressor and the nearest wall is recommended. This
will make it accessible from all sides and provide
unrestricted air flow for adequate cooling.
Noise Level: Many factors affect the noise level generated
by a compressor installation. Several of these, including
motor noise, piping vibration, foundation/skid design,
and surrounding structures are outside Corken’s control.
The use of sufficient pipe supports, flexible hoses, and
proper baseplate/skid support will all reduce noise. Thus,
Corken cannot guarantee a particular noise level from our
compressors. However, noise levels from a properly installed
Corken compressor should not exceed 85dBa at three feet.
1.2 Foundation
Proper foundations are essential for a smooth running
compression system. Corken recommends the
compressor be attached to a concrete slab at least 8
inches thick with a 2 inch skirt around the circumference
of the baseplate. The baseplate should be securely
anchored into the foundation by 1/2 inch diameter “J”
bolts that are 12 inches long. The total mass of the
foundation should be approximately twice the weight of
the compressor system (compressor, baseplate, motor,
etc.). See figure 1.2 for details.
After leveling and bolting down the baseplate, the volume
beneath the channel iron baseplate can be grouted to
prevent flexing of the top portion of the baseplate and
the “J” bolt that extends beyond the foundation. The
grout also improves the dampening capabilities of the
foundation by creating a solid interface between the
compressor and foundation.
On some of the longer baseplates, such as with the 107
mountings, a 3 inch hole can be cut in the baseplate for
filling the middle section of the baseplate with grout.
For a more detailed explanation of a proper foundation
design, please refer to Important "
Instructions for
Compressor Foundation Design
” (item number ED410).
Main beam (C-Beam)
Cross beam (H-Beam)
3/4″ diameter “J” bolt
Hex nut
&
washer
Concrete foundation
Note: The depth of the concrete foundation will
vary based on local soil conditions.
Figure 1.2: Recommended foundation details
for Corken compressors
1.3 Piping
Proper piping design and installation is as important as a
proper foundation is to a smooth operating compressor.
Improper piping installation will result in undesirable
transmission of compressor vibration to the piping.
DO NOT SUPPORT PIPING WITH THE COMPRESSOR.
Unsupported piping is the most frequent cause of vibration
of the pipe. The best method to minimize transmission of
vibration from the compressor to the piping is to use
flexible connectors (see figure 1.3 for details).
Pipe must be adequately sized to prevent excessive pressure
drop between the suction source and the compressor as
well as between the compressor and the final discharge
point. In most cases, piping should be at least the same
diameter as the suction nozzle on the compressor.
If a restrictive device such as a valve, pressure regulator,
Chapter 1—Installing Your Corken Compressor
Ground level
Concrete
foundation
Baseplate should be
a maximum of 4″ high
Grouted
baseplate
Pipe support
Pipe support
Flexible connections
Flexible connections
Figure 1.3: 103 mounting shown above.
5