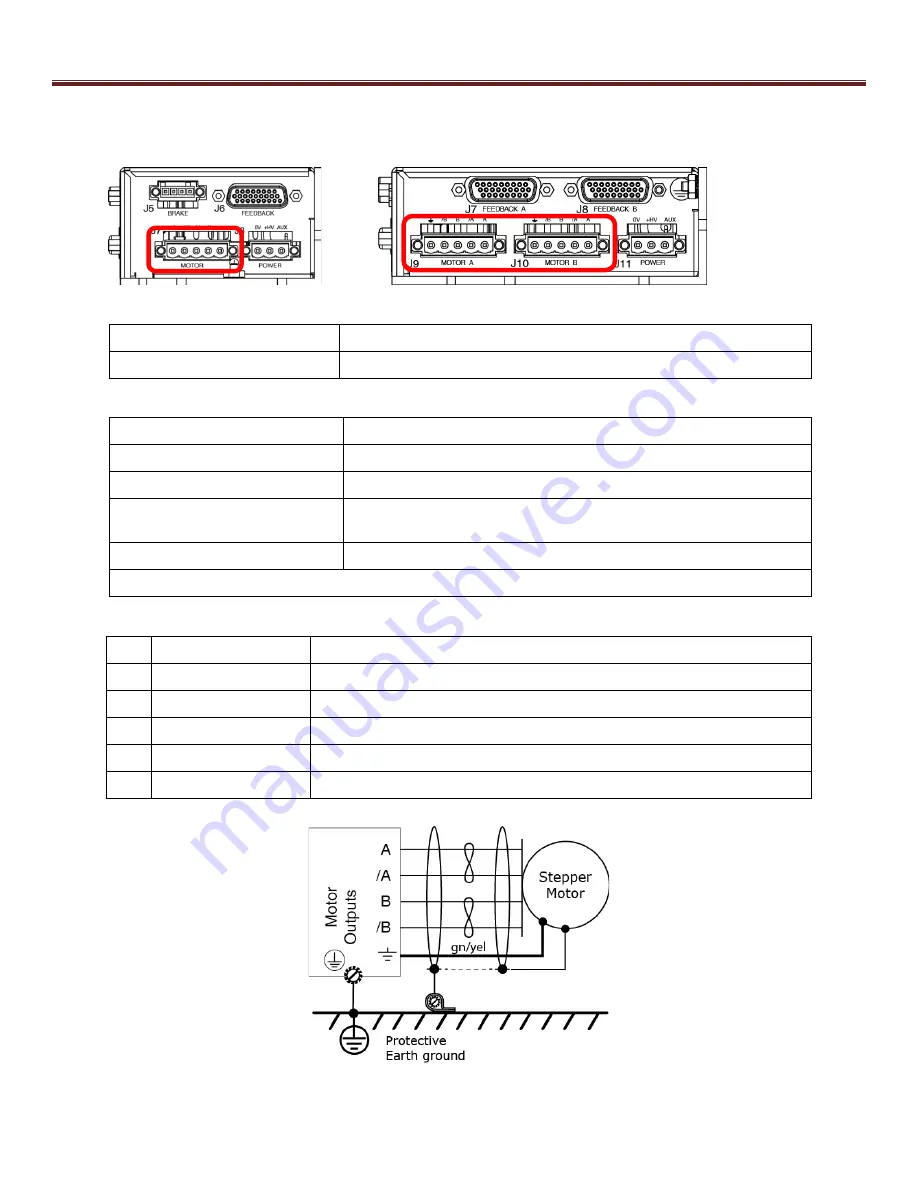
Accelnet & Stepnet Plus Panels User Guide
16-01339 Rev 07
5.6 TEL,
TE2,
TP2
M
OTOR
C
ONNECTORS
M
OTOR
C
ONNECTOR
L
OCATIONS
M
OTOR
R
ECEPTACLE
Description
Euro-style 5.08 mm, 5-position, male receptacle
Manufacturer PN
Wago: 231-564/108-000
C
ABLE
P
LUG
Description
Euro-style, 5 position, 5.08 mm pluggable female terminal block
Manufacturer PN
Wago: 231-305/107-000
Wire Size
22 - 14 AWG
Recommended Wire
22~14 AWG, 600 V
Shielded cable required for CE compliance
Wire Insertion/Extraction Tool
Wago: 231-131
Standard connector and tool are included in Connector Kits TEL-CK, TE2-CK, and TP2-CK.
P
IN
D
ESCRIPTION
Pin
Signal
Function
1
Ground
Motor frame ground and cable shield
2
/B
Output /B
3
B
Output B
4
/A
Output /A
5
A
Output A