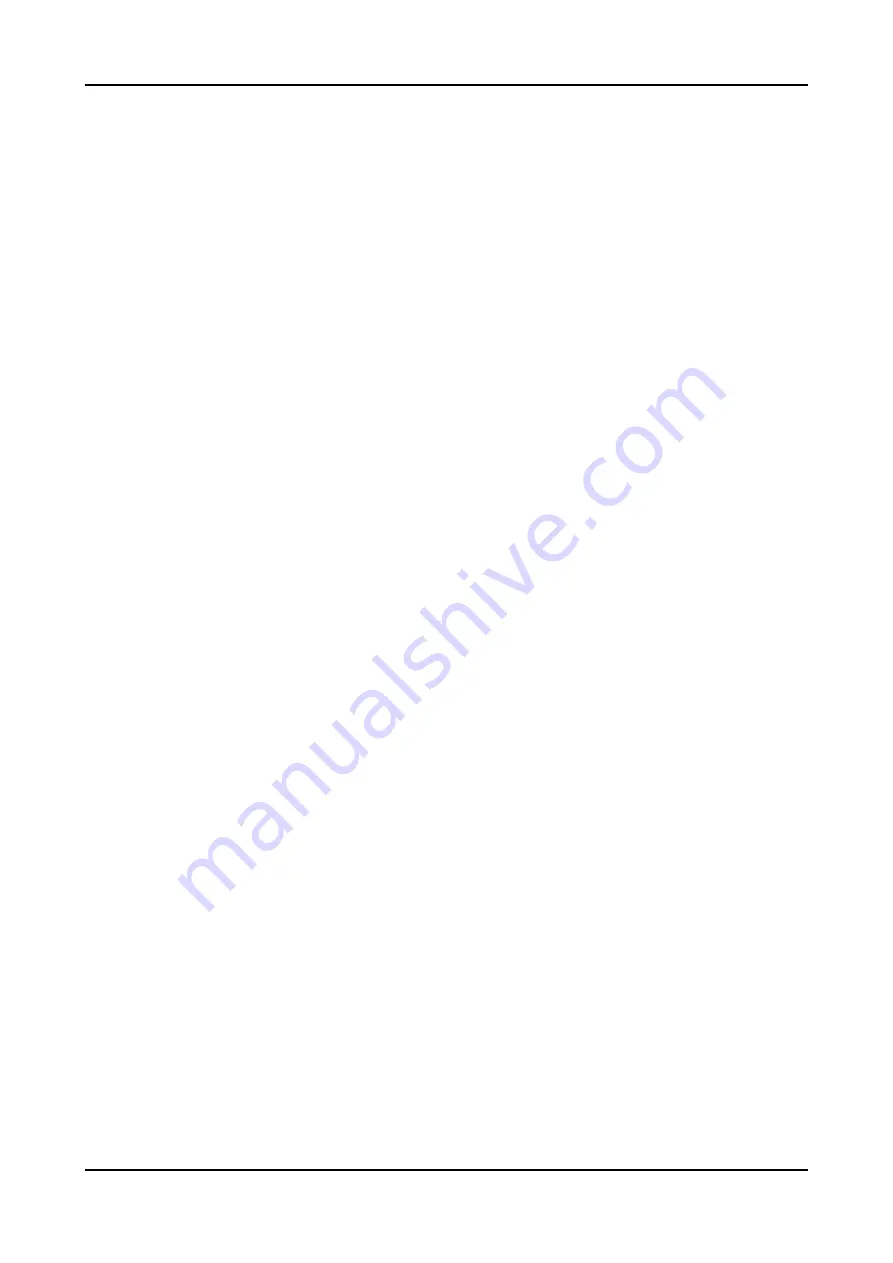
CompAir Limited
page 12
1.
COMPRESSOR
CompAir V-Compact reciprocating compressors are
single-acting units with two or four cylinders
arranged in a 90°-Vee formation for complete
primary balance. The standard version has two
compression stages while the Low Pressure version
is a single-stage machine.
These compressors are available in 'oil-free' or
'lubricated' versions. Two-stage compressors are
fitted with an air-cooled or water-cooled intercooler.
The cylinders, crankcase and air-cooled
intercoolers are cooled by air blast from a cowled
fan fitted on the non-drive end of the crankshaft. The
cylinders and cylinder heads are furnished with
cooling fins.
The normal drive method is by electric motor flange-
mounted to the compressor driving the crankshaft
directly through a flexible coupling. Alternative drive
arrangements include direct drive via a separately
mounted electric motor and flexible coupling and an
electric motor or diesel engine mounted with the
compressor on a common base-plate and driving
through multiple Vee-belts and pulleys.
The crankcase is a single iron casting provided with
large access doors. Two detachable bearing
housings carry the crankshaft main journal white
metal bearing shells. The counterbalanced
crankshaft has either one or two crankpins, each
crankpin carrying two forged steel connecting rods
on plain steel backed aluminium/tin big-end
bearings.
Each 1st stage piston of the oil-free compressors
carries a single two-piece pressure ring and one
guide ring. The 2nd stage pistons are fitted with two
pressure rings and one guide ring. All the rings are
of PTFE. Each piston is driven by a rod attached to
a crosshead carried on the connecting-rod small
end. Ventilated distance pieces fitted between the
crankcase and the cylinders incorporate the
crosshead guide sleeves and gland assemblies
which prevent oil from entering the cylinders.
In the lubricated compressors no distance pieces
are required and the pistons are attached directly to
the connecting rod small ends by hardened steel
gudgeon pins.
GENERAL DESCRIPTION
Two suction and two delivery valves are fitted in each
first stage cylinder head and one suction and one
delivery valve in each second stage cylinder head.
The delivery manifold is designed as a pulsation
vessel to minimise valve pressure peaks in the air
delivery pipe to the aftercooler or receiver .
2.
SAFETY DEVICES
The standard compressors have a safety switch
mounted on the crankcase which operates to shut
down the compressor if oil pressure falls too low.
Two switching thermometers protect the compressor
against high 1 st stage and 2nd stage air
temperature. An interstage safety valve provides
protection to the 1 st stage pressure system.
On low pressure versions the safety switch provides
protection against low oil pressure and high air
temperature.
3.
INSTRUMENT PANEL
On standard machines an instrument panel
mounted on the compressor carries 1 st stage and
2nd stage air pressure gauges, two switching
thermometers and an oil pressure gauge. On low
pressure models the panel carries a delivery air
pressure gauge and an oil pressure gauge.
4.
LUBRICATION SYSTEM
An externally-mounted gear type pump is belt driven
from the fan end of the crankshaft. Oil is drawn into
the pump through a submerged strainer in the
crankcase and is circulated through the lubrication
system via a full-flow oil filter. An adjustable
pressure relief valve is incorporated in the pump and
a dipstick is fitted in the crankcase oil filler tube.
Содержание EO40/0001
Страница 12: ...CompAir Limited page 10...
Страница 16: ...CompAir Limited page 14...
Страница 17: ...page 15 V100 VL400 User Manual 3 LEADING PARTICULARS...
Страница 39: ...page 37 V100 VL400 User Manual 7 FAULT FINDING...
Страница 44: ...CompAir Limited page 42...
Страница 45: ...page 43 V100 VL400 User Manual APPENDIX 1 The Pressure Systems Safety Regulations 2000...
Страница 48: ...CompAir Limited page 46...