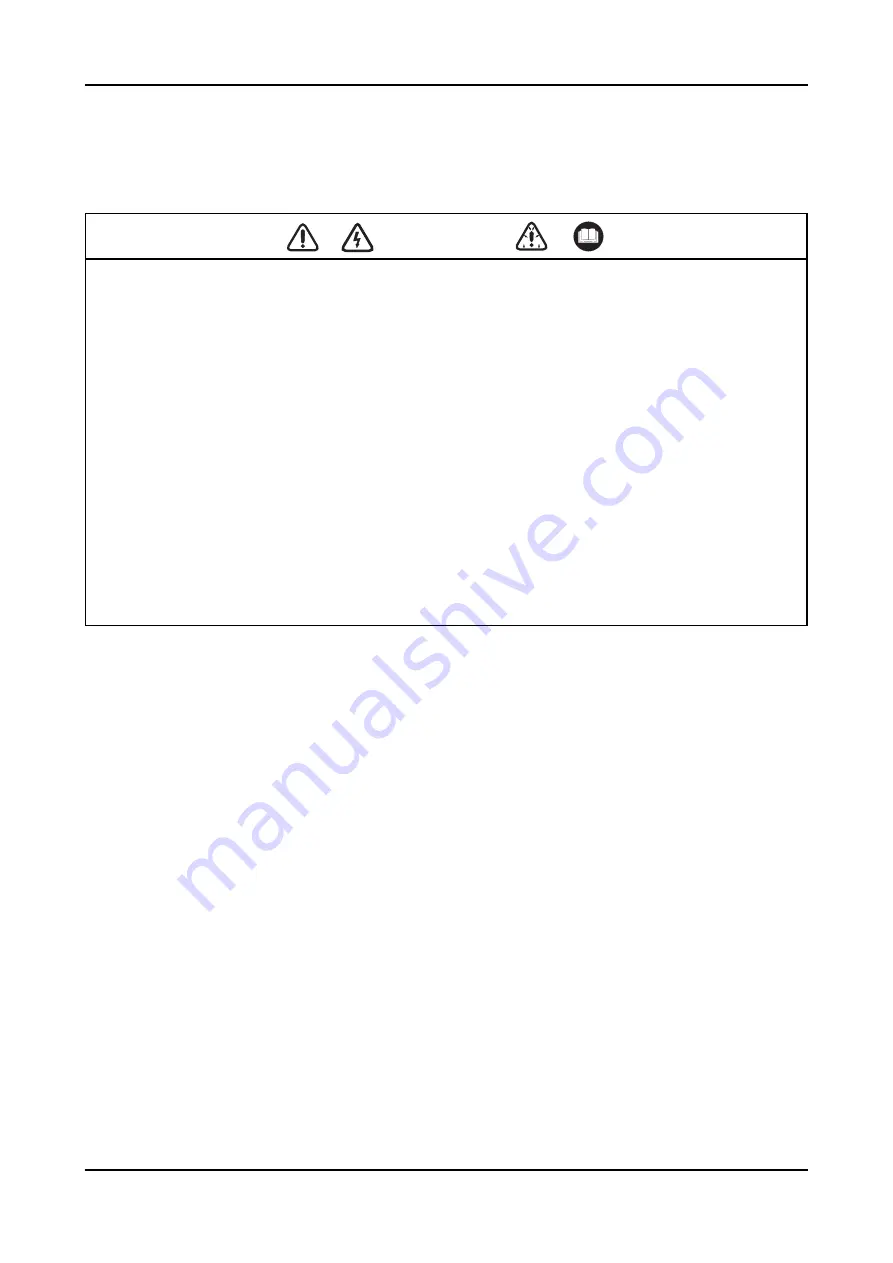
page 35
V100-VL400 User Manual – Maintenance
4.
MAINTENANCE PROCEDURES
The compressor must be stopped.
Remove the oil filler cap, withdraw the dipstick and
check the level. If topping up is required, pour in the
appropriate quantity of the correct oil to bring the
level up to the 'MAX' mark on the dipstick. Refit the
oil filler cap.
4.1.3 To Change the Oil Filter Element
The full-flow oil filter has a disposable cartridge type
element.
The compressor must be stopped.
1.
Remove the old filter element by unscrewing it
from the housing and discard it.
2.
Carefully clean out the filter housing.
3.
Apply a light film of oil to the seal of the new
element.
4.
To fit the new element, screw it into the
housing until it contacts the gasket and then
tighten it a further quarter turn.
4.1 Lubrication System
4.1.1 Recommended Oil
At ambient temperatures from 0° to 30°C, the
recommended oil for the 3000 Series V-Compact is
Shell Corena P68. Where temperatures are
consistently in excess of 30°C, use 100 viscosity
rating of the selected brand.
For alternative lubricants consult your local
distributor. In normal circumstances the oil should
be changed after every 2,500 hours of service. If the
compressor is operating in adverse conditions, such
as high dust levels or the presence of chemical or
other pollutants, more frequent oil changes may be
necessary.
4.1.2 To Check the Oil Level
The oil level is indicated on the dipstick housed
inside the oil filler tube. The oil level is correct when
it reaches the 'MAX' mark.
z
Refer to the safety procedures before carrying
out any maintenance or servicing work on the
compressor unit.
z
Lethal voltages are used in this equipment.
Use extreme caution when carrying out
electrical checks. Isolate the power supply
before starting any maintenance work.
z
Where a maintenance procedure below
includes the warning
'The compressor must
be stopped'
the following steps must be
taken before work is commenced:
1. Close the isolating shut-off valve to the
receiver.
2. Switch the power supply 'OFF' at the
isolator.
3. Check that all pressurised air trapped in the
system is released to atmosphere.
4. Check that all pressure gauges on the
display panel register zero.
5. Ensure that the cooling water system has
been drained on water cooled models.
6. Check that the drain valve on the delivery
manifold is clear and air pressure released.
7. Open the manual drain cock to ensure that
pressurised air trapped between the first
and second stages has been released.
WARNING
Содержание EO40/0001
Страница 12: ...CompAir Limited page 10...
Страница 16: ...CompAir Limited page 14...
Страница 17: ...page 15 V100 VL400 User Manual 3 LEADING PARTICULARS...
Страница 39: ...page 37 V100 VL400 User Manual 7 FAULT FINDING...
Страница 44: ...CompAir Limited page 42...
Страница 45: ...page 43 V100 VL400 User Manual APPENDIX 1 The Pressure Systems Safety Regulations 2000...
Страница 48: ...CompAir Limited page 46...