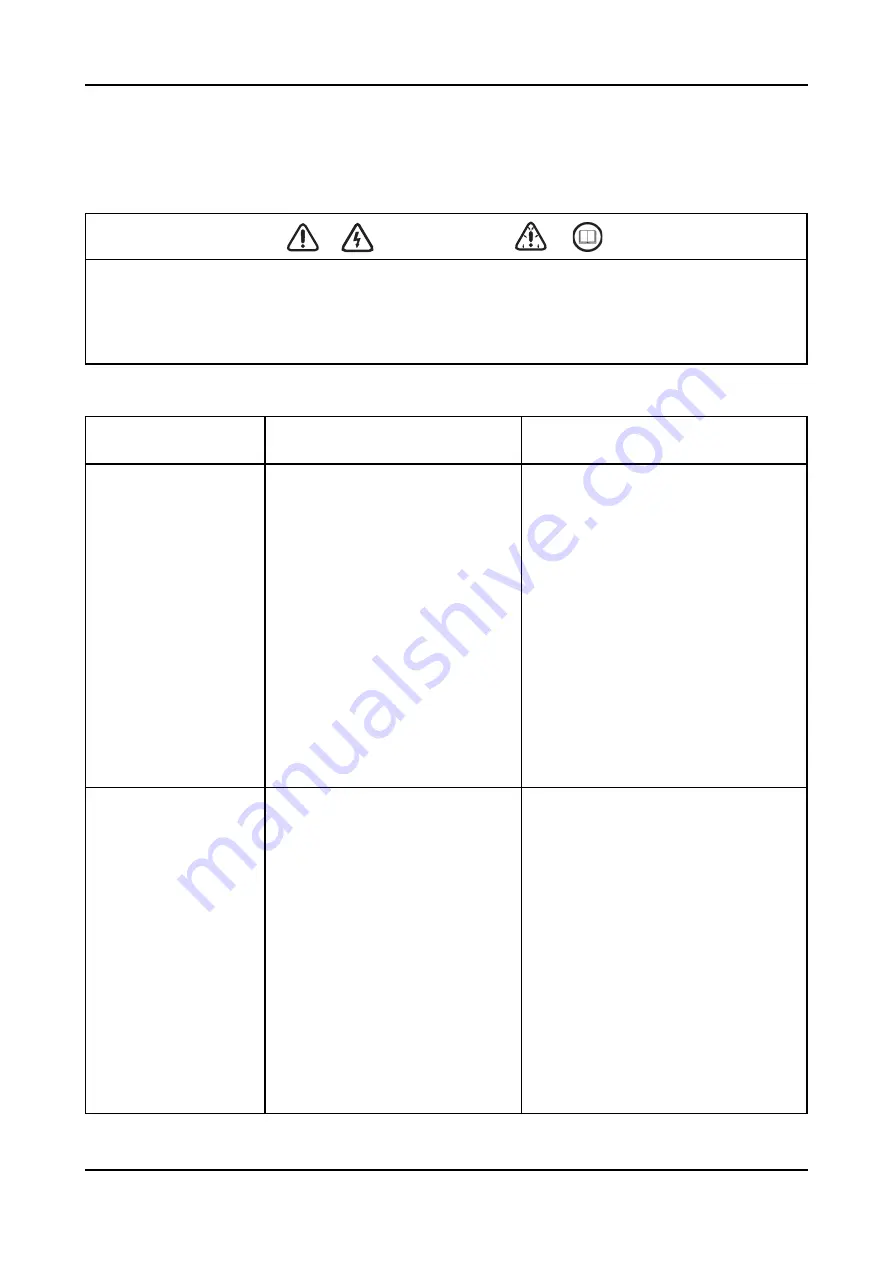
CompAir Limited
page 38
z
Refer to the safety procedures before carrying
out any fault finding investigation on the
compressor unit.
WARNING
z
Lethal voltages are used in this equipment.
Use extreme caution when carrying out
electrical checks. Isolate the power supply
before starting any maintenance work.
FAULT FINDING
Indication
Possible Cause
Remedy
Low oil pressure.
(1)
Low oil level.
(1)
Check/top up oil.
(2)
Incorrect grade of oil in
(2)
Drain crankcase and refill with
crankcase.
correct oil.
(3)
Oil pump drive belt or pulley
(3)
Check drive belt and pulley.
loose.
Rectify or renew as necessary.
(4)
Oil pressure gauge faulty.
(4)
Check gauge calibration.
Renew gauge if defective.
(5)
Incorrect setting of oil
(5)
Check setting of valve. If
pressure relief valve.
necessary remove and clean
Ball valve sticking in
valve assembly.
open position.
Check seating. Reset valve.
(6)
Clogged oil filter element.
(6)
Renew oil filter element.
(7)
Broken or loose connections
(7)
Check condition of oil pipes
on oil pipework.
and filter. Renew if necessary.
(8)
Oil pump gears faulty.
(8)
Renew oil pump gears.
(9)
Worn main bearings.
(9)
Inspect bearings and small
end bushes. Renew if necessary.
Compressor
(1)
Inadequate ventilation of
(1)
Check ventilation meets
overheating.
compressor room.
the recommendations in the
'Installation' section of this
manual.
(2)
Incorrect positioning of
(2)
Check positioning meets
compressor or aftercooler.
the recommendations in the
'Installation' section of this
manual.
(3)
Valves faulty.
(3)
Remove valves. Inspect valve
plates, springs and seats.
Check condition of ring joints.
Renew as necessary .
(4)
Intercooler passages
(4)
Clean intercooler internally and
obstructed (usually only
externally.
after very long service).
Содержание EO40/0001
Страница 12: ...CompAir Limited page 10...
Страница 16: ...CompAir Limited page 14...
Страница 17: ...page 15 V100 VL400 User Manual 3 LEADING PARTICULARS...
Страница 39: ...page 37 V100 VL400 User Manual 7 FAULT FINDING...
Страница 44: ...CompAir Limited page 42...
Страница 45: ...page 43 V100 VL400 User Manual APPENDIX 1 The Pressure Systems Safety Regulations 2000...
Страница 48: ...CompAir Limited page 46...