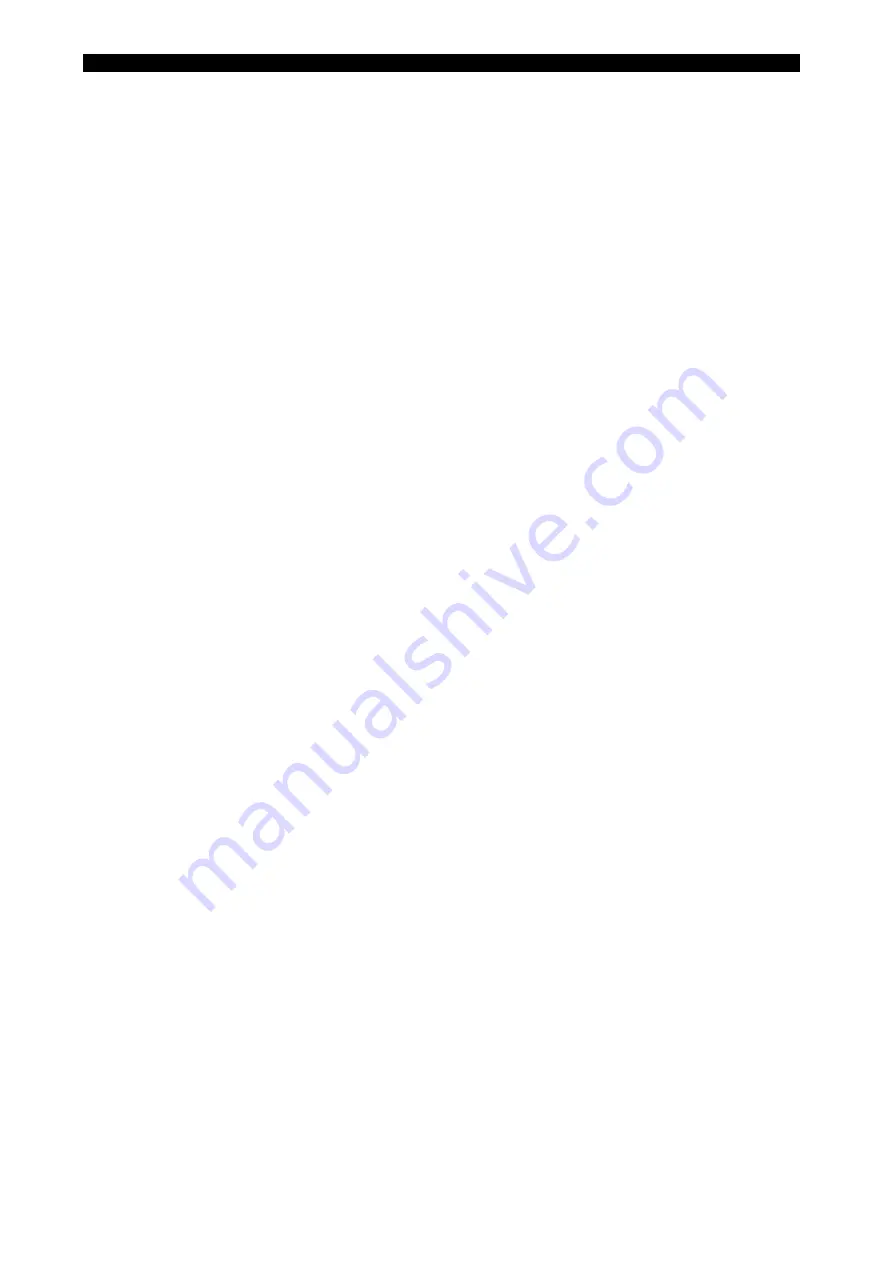
instruction for the service people
22
PROBLEMS
TROUBLE SHOOTING
e)make sure that the plugs of the
spray arms are fitted correctly
f)if the pump is not running; check
the following:
- the overload relay of the motor
protector has not excluded the
respective pump; in this case
reset it (this fault is signalled by
the lamp "H03" being illuminated)
- the coil of the relevant
contactor are not faulty
- the pump itself is not blocked, and is
not going in the wrong direction or has
a worn or broken impeller.
Insufficient tank temperature
a)make sure that the thermostat is
not damaged.
b)make sure that the water supply
temperature is as prescribed
(50/55°C)
c)check that the fuses and the coils
of the contactor relating to the
heating elements are not interrupted
(only for machines with electric
heating).
d)check the elements are heating
and that no limescale deposit has
formed.
e)for machines with steam heating
check the steam solenoid valves,
the steam traps are clear and the
steam pressure at the machine.
Check the installation of the
condense recovery by detaching the
discharge tube of the steam
condense and discharge it into
an open drain.
Содержание ACS122
Страница 1: ...INSTRUCTION MANUAL FOR DISHWASHING Mod ACS122 ACS151 ACS152 ACS181 ACS182 ACS201 ACS202 ACS241 ACS242 ...
Страница 2: ......
Страница 4: ...instruction for the user 4 ...
Страница 7: ...instruction for the user 7 INSTRUCTIONS FOR USE ...
Страница 26: ...ACS 122 eng 03 2003 ...