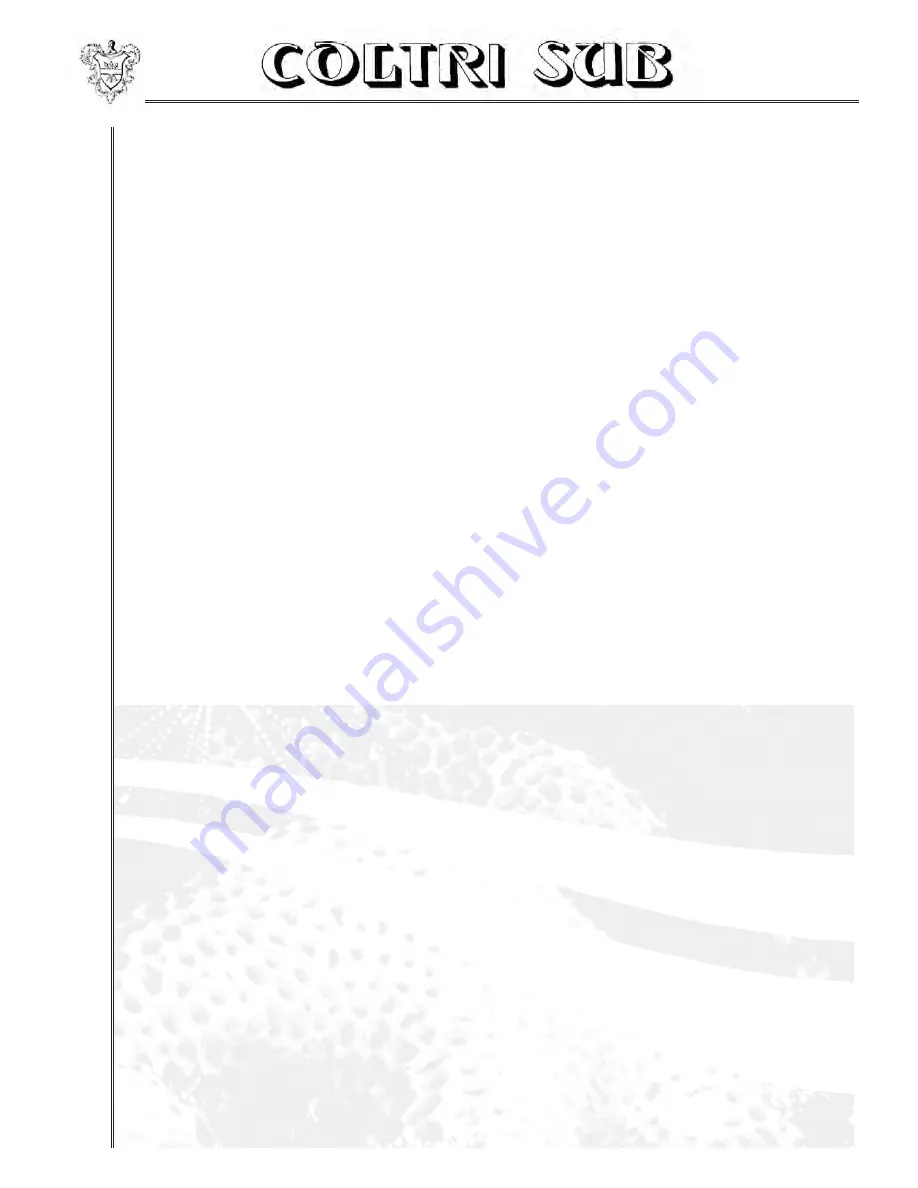
Revision:
I
NSTRUCTION
M
ANUAL
VERSION: English
Special equipment and compressors for underwater activities
High Pressure Compressors
High Pressure Compressors
DOC. STANDARD-06-00
MCH 8/EM
MCH 13-16/DH
MCH 13-16/ETC
MCH 13-16/ET
MCH 13-16/DY
MCH 13-16/SH
STANDARD
MCH 8/EM
MCH 13-16/DH
MCH 13-16/ETC
MCH 13-16/ET
MCH 13-16/DY
MCH 13-16/SH
STANDARD
Содержание MCH 13/DH
Страница 93: ...93 13 2 Electricals diagrams Machine diagrams...
Страница 94: ...94 Machine diagrams...
Страница 100: ...100 126 124 125 123 017 018 015 019 021 002 002 A 022 007 038 037 039 043 043 A 190 191 024 Spare parts Cylinders unit...
Страница 106: ...106 153 152 156 155 154 158 097 157 159 160 198 188 187 189 Spare parts Filtering system...
Страница 110: ...110 MCH 13 16 ETC Spare parts 006 007 008 009 005 012 013 010 011 002 001 003 004...
Страница 112: ...112 MCH 13 16 ET Spare parts 006 007 008 009 005 012 013 010 011 002 001 003 004 015 014 016...
Страница 114: ...114 MCH 8 EM Spare parts 006 007 008 009 017 012 013 010 011 002 001 003 004 015 014 016...
Страница 116: ...116 MCH 13 16 SH Spare parts 006 007 008 009 018 012 013 019 020 002 001 003 004...
Страница 118: ...118 MCH 13 16 DY Spare parts 015 014 003 004 002 001 022 023 009 016 007 008 021 006 012 013...