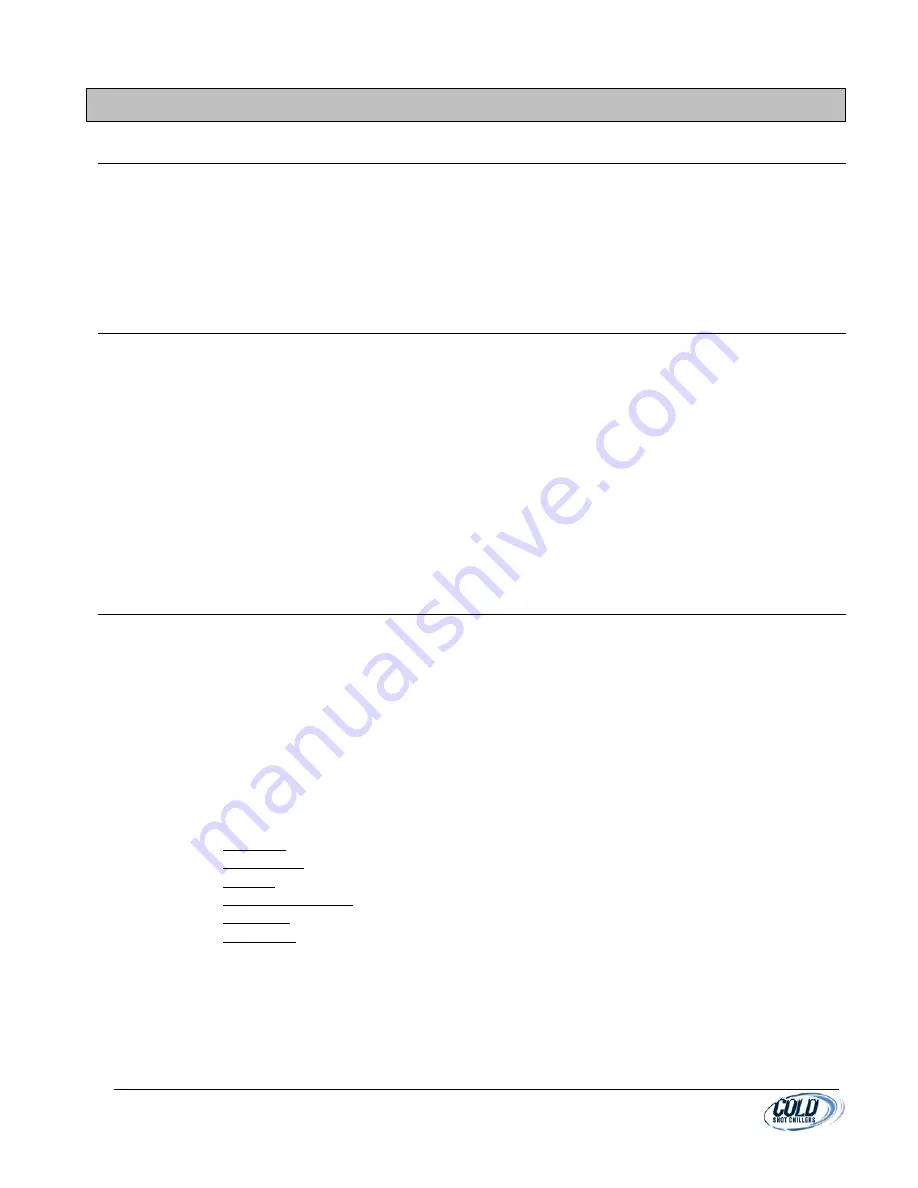
MNL_Standard-NoSpecs_ACWC-18to240-E-_(0713).docx
- 4 -
II.
INSTALLATION
A.
MOVEMENT/RIGGING
1.
The preferred method for movement of the chiller while on the pallet is with forklift or pallet jack.
2.
For rigging, overhead rigging with spreader bars above the unit is preferred. Protect unit from being crushed.
CAUTION! All panels must be in place when rigging. Failure to follow these requirements could result in personal
injury or equipment damage.
3.
Maneuvering of the system must be done with care to prevent damage to the panels or the internal components
mounting.
4.
See specification sheets for physical data and unit dimensions.
B.
PLACEMENT
1.
Select a location for air-cooled units with adequate air circulation that is as dust free as possible.
2.
There must be a minimum of 3 ft of space for service and for unrestricted airflow on all sides of unit, and a
minimum of 8 ft clear air space above unit. Select a location where air is not recirculated back into condenser.
For multiple units, allow additional separation between units for airflow and service.
3.
Verify ambient conditions that the system is suitable.
a)
IND - Indoor units are suitable for indoor use only. No wet environments.
b)
40 - Outdoor units to 40°F (same as above) and are suitable for outdoors to 40°F ambient temperature
and suitable for wet environments.
c)
0 - Outdoor units to 0°F (same as above) and suitable for outdoors to 0°F ambient temperature.
d)
M20 - Outdoor units to -20°F (same as above) and suitable for outdoors to -20°F ambient temperature.
4.
Avoid environments which may be corrosive to the chiller.
5.
Avoid locations that may have direct spray such as from roof edges or sprinklers.
6.
Select location as near to the process as possible to reduce the system piping / pressure drop.
C.
MOUNTING
1.
Level the unit to ensure proper oil return to compressors and fluid draining.
2.
When unit is in proper location, secure unit to foundation or on vibration isolators, as needed/required by local
requirements. Fasteners for mounting unit are field supplied.
3.
PIPING
a)
Connect piping or hoses to unit, making sure that the inside diameter (I.D.) of the pipe or hose is the
same as or greater than unit connections and that the material is designed for the expected fluid
conditions.
b)
The fluid circuits must contain a bypass to prevent a “dead head” condition for the pump and to allow
return process water to chiller tank. A bypass valve is required in the system to ensure proper flow
through the evaporator and to provide adjustment of the pressure and flow to the process.
(1)
Refer to the system Flow Diagram for details, or to the actual unit.
c)
Typical Chiller Fluid Flow Designs:
(1)
Stationary: Chilling system with evaporator.
(2)
Reverse Flow: Chilling system with evaporator and circulating pump.
(3)
Portable: Chilling system with evaporator, circulating pump, and reservoir tank.
(4)
Extra Heat Exchanger: Same as Portable along with an extra chilled fluid heat exchanger.
(5)
Dual Pump: Same as Portable and includes a second pump typically for process use.
(6)
Dual Return: Same as Portable yet includes a second return direct to tank for some flow.
d)
System Recommendations:
(1)
Valves installed throughout the system, as needed. Typical at each load for isolation and
flow/pressure balancing purposes through system.
(2)
Use low pressure drop design components. (Such as long radius 90s or 45s elbows)
(3)
Add piping and valve to the tank drain port.
(4)
Temperature and pressure gauges throughout system at ideal locations for monitoring.
(5)
Vent and drain valves to provide ability to bleed air and drain fluids from system, as needed.