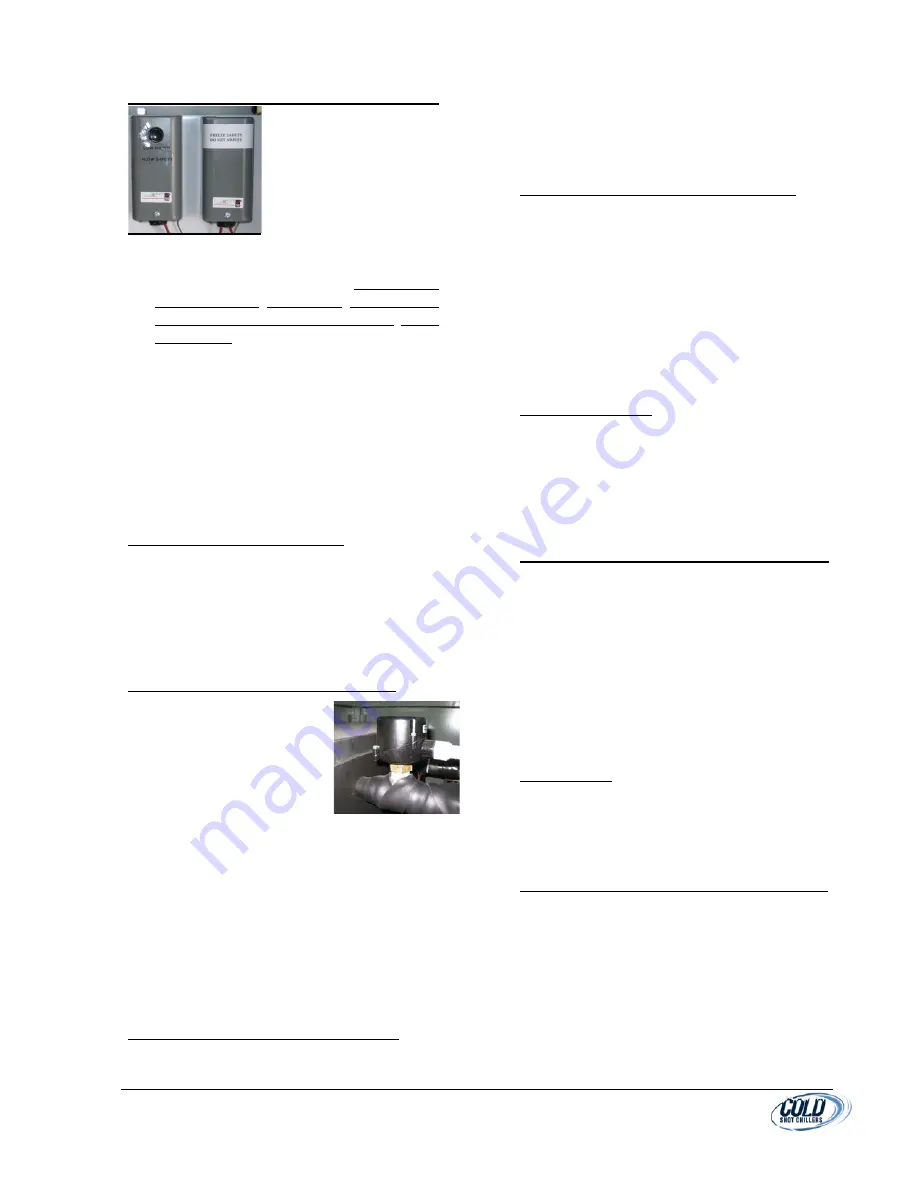
MNL_Standard-NoSpecs_ACWC-18to240-E-_(0713).docx
- 11 -
8.
FLOW SAFETY THERMOSTAT
(FS):
a.
Generally the cause will be low or insufficient
water flow caused by a clogged “Y” strainer or
restricted flow in the process. Resetting this
control and not determining the cause for
tripping can cause the evaporator to freeze
and rupture.
b.
Indoor chillers are normally equipped with a
Low Flow Safety temperature sensor that
detects temperature of the refrigerant. This
safety will automatically trip and requires
manual resetting before the cooling cycle will
resume. This safety can also be tripped by low
ambient conditions overnight or during
shipping.
c.
Do not reset this control unless the exact
cause for its tripping is determined.
9.
FREEZE SAFETY (FZ): (IF EQUIPPED)
a.
Indoor chillers are typically equipped with a
Freeze Safety temperature sensor that
detects low temperature of the fluid in the
system. This safety will automatically trip and
is reset automatically when the water
temperature returns to the higher sensor
setting difference.
10.
FLOW SWITCH SAFETY (FSS): (IF EQUIPPED)
a.
Refer to the LOW FLOW
SAFETY for explanation
and cautions.
b.
Outdoor units with Low
Ambient Kits are normally
equipped with a
mechanical flow switch
which monitors the
fluid
entering the
evaporator. This switch is automatically reset
when the fluid flow returns to the proper flow
rate. Adjustment should not be performed
unless necessary. If adjustments are made,
ensure that the flow entering the evaporator
is greater than 3 gallons per minute per ton of
refrigeration rating of the chiller. For
example, a 2 Ton chiller will need a minimum
of 6 gpm.
11.
REFRIGERANT LOW PRESSURE SAFETY (LPS)
a)
Monitors the pressure of the refrigerant
suction line and will automatically open
when the pressure drops below the set
point and will automatically reset when
pressure is above the non-adjustable
reset setting. (See specifications for
details)
12.
REFRIGERANT
HIGH PRESSURE SAFETY (HPS)
a)
Monitors the pressure of the refrigerant
and will automatically open when the
pressure rises above the sensor fixed set
point. (See specifications for details)
b)
Reset types are manual or automatic,
depending on design and system.
a)
Manual Reset - requires that a
button be pressed.
b)
Automatic Reset - automatically reset
when pressure is below the reset
setting.
13.
CAPACITY CONTROLS
a.
System with multiple compressor permit the
use of capacity control using the temperature
controller system.
b.
Hot Gas Bypass (Option) - A bypass valve in
the refrigerant system that permits that
cooling output capacity of the chiller to vary
based on the load of the system.
14.
LOW AMBIENT CONDITION CONTROLS
(OPTIONS)
a.
Low Ambient Conditions to 0°F Kit (Option)
b.
Temperature of the chiller’s ambient
condition is monitored and will change the
operation of the chiller fans to reduce the
possibility of freezing condenser fan cycling.
c.
NOTE: Low Ambient chillers typically do not
have the Low Flow Safety or a Freeze Safety.
They are equipped with a pressure controlled
fan control system which is used to operate
the fan (or Fan #2 or #3 only on multiple fan
unit chillers).
15.
WIND BAFFLES
(Depending on design)
a.
Panels mounted in or on the condenser coil
section to limit/control the amount of air
entering the coils. (Option)
b.
Typically used with Low Ambient kit systems
with controls down to -20°F Kit.
16.
LOW CHILLED WATER TEMPERATURE (Low LCWT)
a.
Low Temperature refers to the temperature
of the fluid leaving the chiller is lower than
the temperature of the standard temperature
machine’s Leaving Chill Water Temperature
(LCWT). Glycol or some other freeze
protected fluid is required.
b.
The temperature controller parameters must
be setup for the lower leaving temperatures
that the system will generate.
Figure 1 Low Flow
/ Freeze Safety
Figure 2 Flow Switch