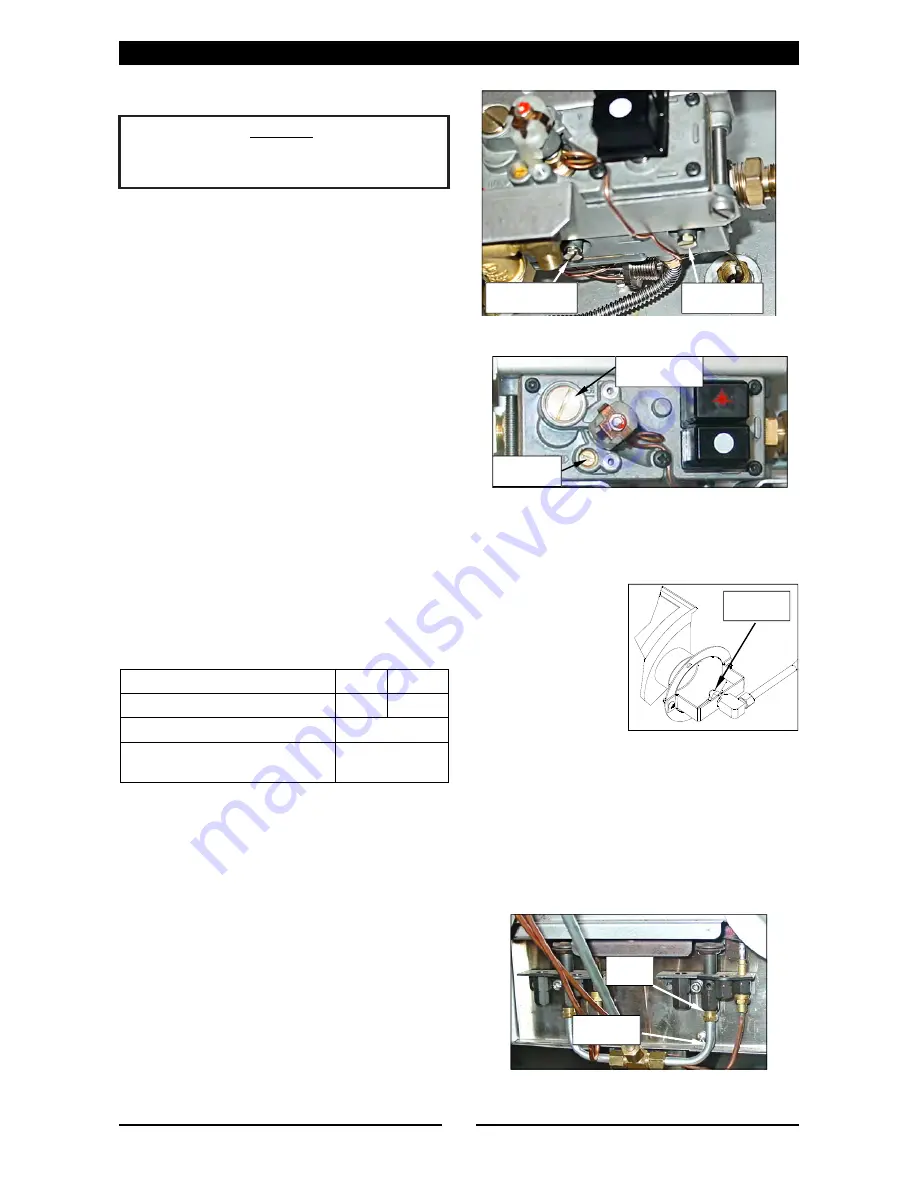
14
Part 7 Gas Conversion
Gas Conversion Procedure
NOTE:
These conversions should only be carried out
by qualified service persons. All connections
must be checked for leaks before
re-commissioning the appliance.
For all relevant information and specifications
refer to the table at the end of this section.
Flexible Hose Connection;
If a Gas Hose assembly is used to connect this
appliance, the hose and all fittings must have
a minimum
¾
” (Natural Gas) or ½” (LPG)
inside bore diameter to ensure gas flow rate
capacity required by this appliance is
achieved.
This must be verified by the operating pressure
testing at the maximum gas supply demand
condition.
The Gas Hose assembly should also be
classified for use in the commercial kitchen
conditions, the appliance will be used in.
Recommended Gas Hose Assembly Specification:-
- AS/NZS 1869 Class B or D compliant or
equivalent, that meets the following
requirements:-
1. Ensure that the gas supply has been turned 'Off'.
2. Open the front door of the unit to access the
main burner and pilot burner injectors.
3. Remove the 4 screws securing the front control
panel to the fryer and remove the front control
panel to access the gas control valve.
4. Remove the Temperature Control Knob from the
front of the gas valve to reveal the Pilot
Adjustment Screw (See 'Gas Specifications' table
for adjustment details) and the Low Fire Blanking
Screw (Screwed fully 'In').
5. Connect a manometer to the Inlet pressure test
point (Line Pressure) on the gas control valve
located on the underside of the valve. Turn on
the gas supply and ensure that the pressure is
within the specification shown in the ‘Gas
Specifications Table’ at the rear of this section.
Main Burner Injectors
1. Unscrew and remove the main burner injectors
(12.7 mm A/F) located in front of main burner
venturi openings.
2. Determine the
correct injectors for
the corresponding
gas from the table
overleaf.
3. Screw in the correct
sized injectors and
tighten.
Pilot Burner Injectors
1. Unscrew the pilot supply tube from the pilot
burner fitted to the mounting bracket and
remove the pilot injector.
2. Determine the correct sized pilot injectors for the
corresponding gas from the table overleaf.
3. Fit the correct sized injector into the pilot burner
and re-connect the gas supply tube to the pilot
burner.
Pilot Screw
Adjustment
Main Burner
Injector
Pilot Supply
Tube
Pilot
Injector
C
AUTION
:
Ensure that the Unit is isolated from the gas
supply before commencing servicing
Inlet Pressure
Test Point
Outlet Pressure
Test Point
Low Fire
Blanking Screw
Class B
D
Max Working Pressure at 23 ± 2
ºC
7.0 kPa 2.6 MPa
Working Temperature Range
- 20
ºC to + 125ºC
Resistance to Oil
Oil resistant lining
and cover.
Содержание cf4
Страница 15: ...13 Part 6 Wiring Schematic CF4 GAS FRYER Wiring Schematic ...
Страница 20: ......