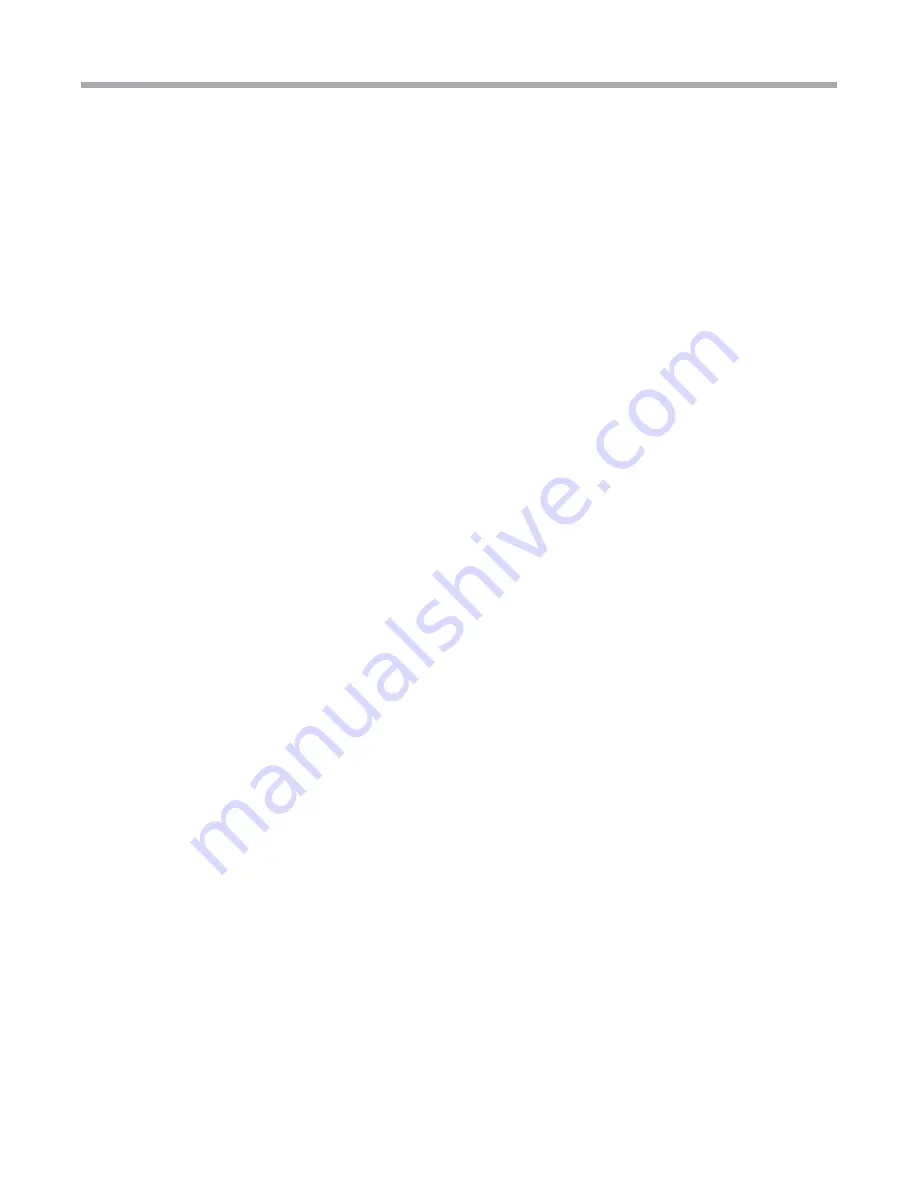
R e s i d e n t i a l H & V - 6 0 H z H F C - 4 1 0 A
R e v. : 9 M a r c h , 2 0 1 1 B
42
G e o t h e r m a l H e a t P u m p S y s t e m s
Preventive Maintenance
Water Coil Maintenance
(Direct ground water applications only) - If the system is
installed in an area with a known high mineral content
(125 P.P.M. or greater) in the water, it is best to establish a
periodic maintenance schedule with the owner so the coil
can be checked regularly. Consult the well water applications
section of this manual for a more detailed water coil material
selection. Should periodic coil cleaning be necessary, use
standard coil cleaning procedures, which are compatible
with the heat exchanger material and copper water lines.
Generally, the more water fl owing through the unit, the less
chance for scaling. Therefore, 1.5 gpm per ton [2.0 l/m per
kW] is recommended as a minimum fl ow. Minimum fl ow
rate for entering water temperatures below 50°F [10°C] is 2.0
gpm per ton [2.6 l/m per kW].
Water Coil Maintenance
(All other water loop applications)
Generally water coil maintenance is not needed for closed
loop systems. However, if the piping is known to have
high dirt or debris content, it is best to establish a periodic
maintenance schedule with the owner so the water coil can
be checked regularly. Dirty installations are typically the result
of deterioration of iron or galvanized piping or components
in the system. Open cooling towers requiring heavy chemical
treatment and mineral buildup through water use can also
contribute to higher maintenance. Should periodic coil
cleaning be necessary, use standard coil cleaning procedures,
which are compatible with both the heat exchanger material
and copper water lines. Generally, the more water fl owing
through the unit, the less chance for scaling. However, fl ow
rates over 3 gpm per ton (3.9 l/m per kW) can produce water
(or debris) velocities that can erode the heat exchanger wall
and ultimately produce leaks.
Hot Water Generator Coils
See water coil maintenance for ground water units. If the
potable water is hard or not chemically softened, the high
temperatures of the desuperheater will tend to scale even
quicker than the water coil and may need more frequent
inspections. In areas with extremely hard water, a HWG is
not recommended.
Filters
Filters must be clean to obtain maximum performance.
Filters should be inspected every month under normal
operating conditions and be replaced when necessary. Units
should never be operated without a fi lter.
Washable, high effi ciency, electrostatic fi lters, when dirty,
can exhibit a very high pressure drop for the fan motor and
reduce air fl ow, resulting in poor performance. It is especially
important to provide consistent washing of these fi lters (in
the opposite direction of the normal air fl ow) once per month
using a high pressure wash similar to those found at self-
serve car washes.
Condensate Drain
In areas where airborne bacteria may produce a “slimy”
substance in the drain pan, it may be necessary to treat the
drain pan chemically with an algaecide approximately every
three months to minimize the problem. The condensate pan
may also need to be cleaned periodically to insure indoor
air quality. The condensate drain can pick up lint and dirt,
especially with dirty fi lters. Inspect the drain twice a year to
avoid the possibility of plugging and eventual overfl ow.
Compressor
Conduct annual amperage checks to insure that amp draw
is no more than 10% greater than indicated on the serial
plate data.
Fan Motors
All units have lubricated fan motors. Fan motors should
never be lubricated unless obvious, dry operation
is suspected. Periodic maintenance oiling is not
recommended, as it will result in dirt accumulating in the
excess oil and cause eventual motor failure. Conduct annual
dry operation check and amperage check to insure amp
draw is no more than 10% greater than indicated on serial
plate data.
Air Coil
The air coil must be cleaned to obtain maximum
performance. Check once a year under normal operating
conditions and, if dirty, brush or vacuum clean. Care must
be taken not to damage the aluminum fi ns while cleaning.
CAUTION: Fin edges are sharp.
Cabinet
Do not allow water to stay in contact with the cabinet for
long periods of time to prevent corrosion of the cabinet sheet
metal. Generally, vertical cabinets are set up from the fl oor
a few inches [7 - 8 cm] to prevent water from entering the
cabinet. The cabinet can be cleaned using a mild detergent.
Refrigerant System
To maintain sealed circuit integrity, do not install service
gauges unless unit operation appears abnormal. Reference
the operating charts for pressures and temperatures. Verify
that air and water fl ow rates are at proper levels before
servicing the refrigerant circuit.