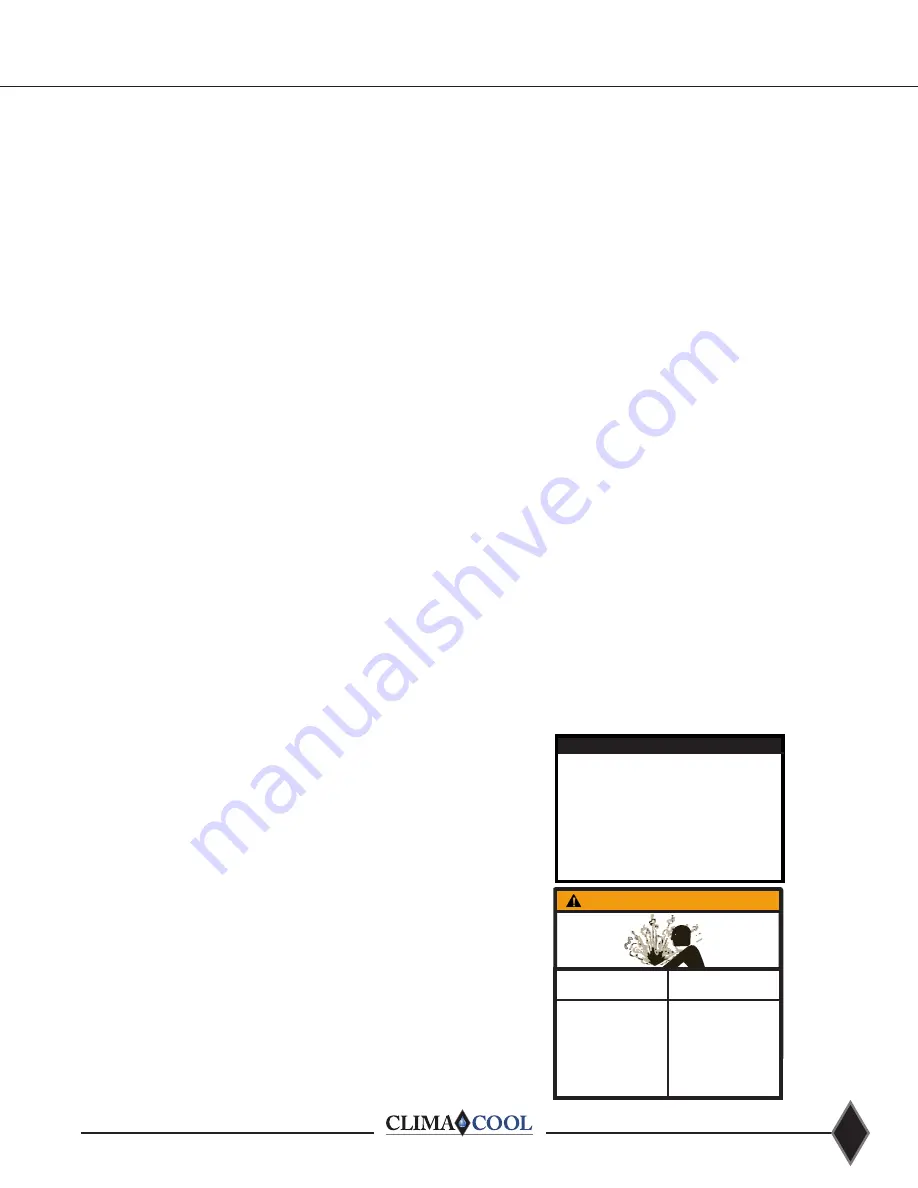
39
®
www.climacoolcorp.com
Conforming to local and national codes is the responsibility
of the service technician or installing contractor . The service
technician should be familiar with the following codes:
• ASHRAE Standard Safety Code for Mechanical
Refrigeration, ANSI/ASHRAE 15-1978
• American National Standard Code for Pressure Piping,
ANSI B31 .5-1974
Factory Tested
ClimaCool modular chillers have been pressure-tested,
evacuated, fully charged and run tested at design water
flow rates prior to shipment. In the unlikely event that
a refrigerant leak is detected at startup, the following
guidelines should be consulted before reprocessing the
refrigeration systems .
Refrigerant System Reprocessing
Debris and moisture can enter copper tubing in a matter
of minutes . All tubing, coil connections or any refrigerant
containing portions should be temporarily capped or sealed
to keep contaminants to a minimum . Filter driers should
be opened just prior to brazing into the system to prevent
moisture infiltration whenever possible, and flood the
system with low pressure dry nitrogen while brazing to
prevent oxidation inside the copper piping .
After all of the repairs have been made to the refrigeration
system, a pressure test using refrigerant and nitrogen
should be performed . Pressurize the system with dry
nitrogen to 20 psi and check for any obvious leaks . If no
leaks are present, introduce a “trace” amount of refrigerant
to the system (raise system pressure to 30-40 psi). With a
dry nitrogen tank equipped with a regulator set to 150 psi,
continue to pressurize the system to 150 psi . Using a leak
detector, carefully check the system for any remaining leaks .
If the system is free of leaks you may release the pressure .
Evacuating the System
The compressors should never run while the system is
in a vacuum.
This could cause immediate failure to the
compressors . After the system has been leak tested and
sealed, any moisture that entered the system should be
dehydrated and removed . While the pressure is reduced
under a vacuum, the boiling point of moisture trapped
inside the lines is also reduced . A pressure of .0095 psia, or
500 microns absolute pressure or better must be reached
and sustained for several hours in order for the system to
be considered free from moisture . It is necessary to use a
micron meter equipped with an absolute pressure gauge (or
transducer) to take this reading . ClimaCool recommends the
triple evacuation process to ensure the proper removal of
moisture and contaminants from the refrigeration system .
After the initial vacuum is reached and held on the system,
allow dry nitrogen back into the system until the pressure
reaches zero psig or slightly higher . Then, repeat the entire
evacuation process described above . The evacuation
process is considered complete
ONLY
after a successful
“blank-off” test is performed.
A “blank-off” test is defined as:
•
Pulling a vacuum level less than 500 microns on the
system and holding it for several hours .
•
Record the vacuum level in the system in microns,
then close off the vacuum pump from the system for
15 minutes, and continue to monitor the micron level
inside the refrigeration system .
•
If the vacuum level inside the system does NOT rise
more than 400 microns above the recorded vacuum
level at the start of the 15 minute period, then the
evacuation process is complete .
If the vacuum level rises more than 400 microns in 15
minutes, then continue to evacuate the system for 1-2 hours,
and repeat a “blank-off” test.
Recharging the System
After all repairs have been completed, the system has
been leak tested and proper vacuum pressures have been
reached and maintained, refrigerant may be recharged
into the system . With a known weight of refrigerant in
the cylinder, use the gauge manifold set to connect the
cylinder’s liquid charging port to the charging access port
near the refrigerant liquid line valve . Open the compressor
suction and discharge line valves, if available . Gradually
meter the appropriate weight of liquid refrigerant into
the condenser side of the system first, until no additional
refrigerant can be dispensed . Accurate refrigerant charge
per circuit may be found in the Physical Data information
on page 3. Then continue the charging process by filling the
evaporator side of the system with refrigerant . Close the
refrigerant cylinder charging port, close all gauge manifold
ports and start the compressor . Be careful when continuing
to charge the balance of the refrigerant, constantly
maintaining a positive compressor suction pressure
(>25 psig) at all times.
Refrigeration System Re-Processing and Charging
ATTENTION
To avoid the release of refrigerant into the atmosphere, the
refrigerant circuit of this unit must be serviced only by
technicians who meet local, state and federal proficiency
requirements.
All refrigerant discharged from this unit must be recovered
WITHOUT EXCEPTION. Technicians must follow industry
accepted guidelines and all local, state and federal statues for
the recovery and disposal of refrigerants.
If a compressor is removed from the unit, system refrigerant
circuit oil will remain in the compressor. To avoid leakage of
compressor oil, the refrigerant lines of the compressor must be
sealed after it is removed.
WARNING/AVERTISSEMENT
WATER AND REFRIGERANT
SYSTEMS UNDER PRESSURE
•
Isolate/Lockout source
and relieve pressure
BEFORE servicing
equipment.
•
Failure to relieve pressure
may result in property
damage, serious bodily
injury or death!
EAU ET FRIGORIGÈNE
EQUIPEMENTS SOUS
PRESSION
•
Isoler la source / de
verrouillage et de
soulager la pression
avant entretien de
l’équipement.
•
Le défaut de soulager la
pression peut entraîner
des dommages matériels,
des blessures corporelles
graves ou la mort!
Содержание UCH 30
Страница 16: ... www climacoolcorp com 14 Voltage Phase Monitor Wiring ...
Страница 21: ...19 www climacoolcorp com Figure 23 Part Load Performance Advantage ...
Страница 57: ...55 www climacoolcorp com Wiring Diagrams 030 050 070 Cooling Only ...
Страница 58: ... www climacoolcorp com 56 Wiring Diagrams 030 050 070 Cooling Only ...
Страница 59: ...57 www climacoolcorp com Wiring Diagrams 030 050 070 Heat Pump ...
Страница 60: ... www climacoolcorp com 58 Wiring Diagrams 030 050 070 Heat Pump ...
Страница 61: ...59 www climacoolcorp com Wiring Diagrams 085 Cooling Only ...
Страница 62: ... www climacoolcorp com 60 Wiring Diagrams 085 Cooling Only ...
Страница 63: ...61 www climacoolcorp com Wiring Diagrams 085 Heat Pump ...
Страница 64: ... www climacoolcorp com 62 Wiring Diagrams 085 Heat Pump ...
Страница 65: ...63 www climacoolcorp com Wiring Diagrams Master Panel ...
Страница 66: ... www climacoolcorp com 64 Wiring Diagrams Master Panel ...
Страница 70: ... www climacoolcorp com 68 Notes ...
Страница 71: ...69 www climacoolcorp com Notes ...