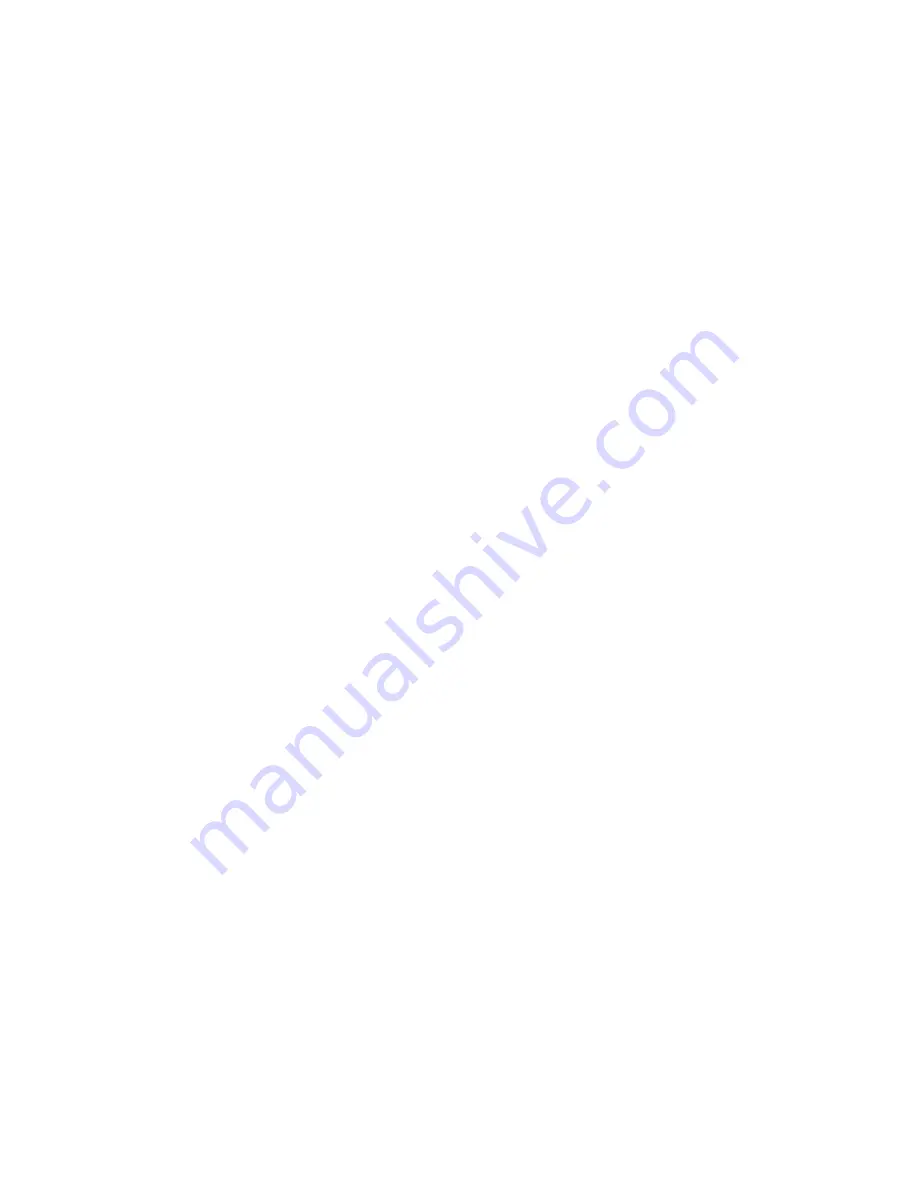
In order to preserve the various agency safety
certification (UL, A.G.A., CSA. CGA, NSF,
ASME/Ntl. Bd., etc.), only factory-supplied
replacement parts should be used. The use of
other than factory-supplied replacement parts
will void the warranty.
KETTLE VENTING INSTRUCTIONS
If the vacuum/pressure gauge reading is in the
"vent air" zone, it means that air has entered
the steam/water jacket, resulting in little or no
vacuum. This reduces kettle efficiency by
slowing its heating process. To remedy this
situation, the following venting procedures
should be followed:
1.
With the temperature control knob set
at number 9, heat the empty kettle until
the vacuum/pressure gauge indicates
5-10 psi.
2.
Release steam and air from the
steam/water jacket by pulling out on
the pin of the safety valve for
approximately 10-15 seconds.
The kettle's steam and air from the
steam/water jacket should now be free of air.
At room temperature, the pressure gauge
needle should rest in the green zone,
indicating a vacuum in the kettle's jacket. To
check the gauge for proper vacuum after
venting, the temperature can be quickly
reduced by filling the kettle with cold water.
If the kettle will not hold vacuum, have a
qualified service technician test for leaks at the
water fill plug, sight gauge, safely valve, probe,
and vacuum/pressure gauge fittings. We
suggest mixing a 50/50 solution of liquid
detergent and water while heating the kettle to
at least 5 psi pressure. Then, shut off power to
the kettle. The soapy solution should be
applied to the suspected area while the
gauge shows at least 5 psi pressure. Any
bubbles which appear will indicate a leak.
RESERVOIR FILL PROCEDURES
The reservoir's water level must be maintained
at the proper level. Under normal operating
conditions, the sealed water reservoir should
not require the addition of water. If the red "low
water" light comes on during use, the water
level has reached a critically low level. The low
water protection control has automatically shut
off the gas burners. The following procedure
must be completed before further use:
WARNING:
Insure there is no pressure
IN
the
unit before removing filler cap.
1.
Shut off
power to the kettle.
2.
Remove water fill cap located at the
rear of the kettle.
3.
Add distilled water until the water level
is between the "HI" and "LO'' markings
on the sight gauge glass.
4.
Replace the water fill cup and carefully
tighten. Do not over-tighten.
5.
Restore power to the kettle.
6.
The kettle must now be vented. Refer
to the "Kettle Venting Instructions".
CAUTION:
It is recommended that only
distilled water be used when adding water to a
partially filled water reservoir. Local tap water
conditions may cause kettle damage which is
not covered under warranty. Add water until
the level is between the "HI" and "LO" marks
on the sight gauge.
6
Содержание KGL
Страница 11: ...GAS CONTROL ASSEMBLY KETTLE...
Страница 13: ...SIDE BOX ASSEMBLY KETTLE...
Страница 16: ......