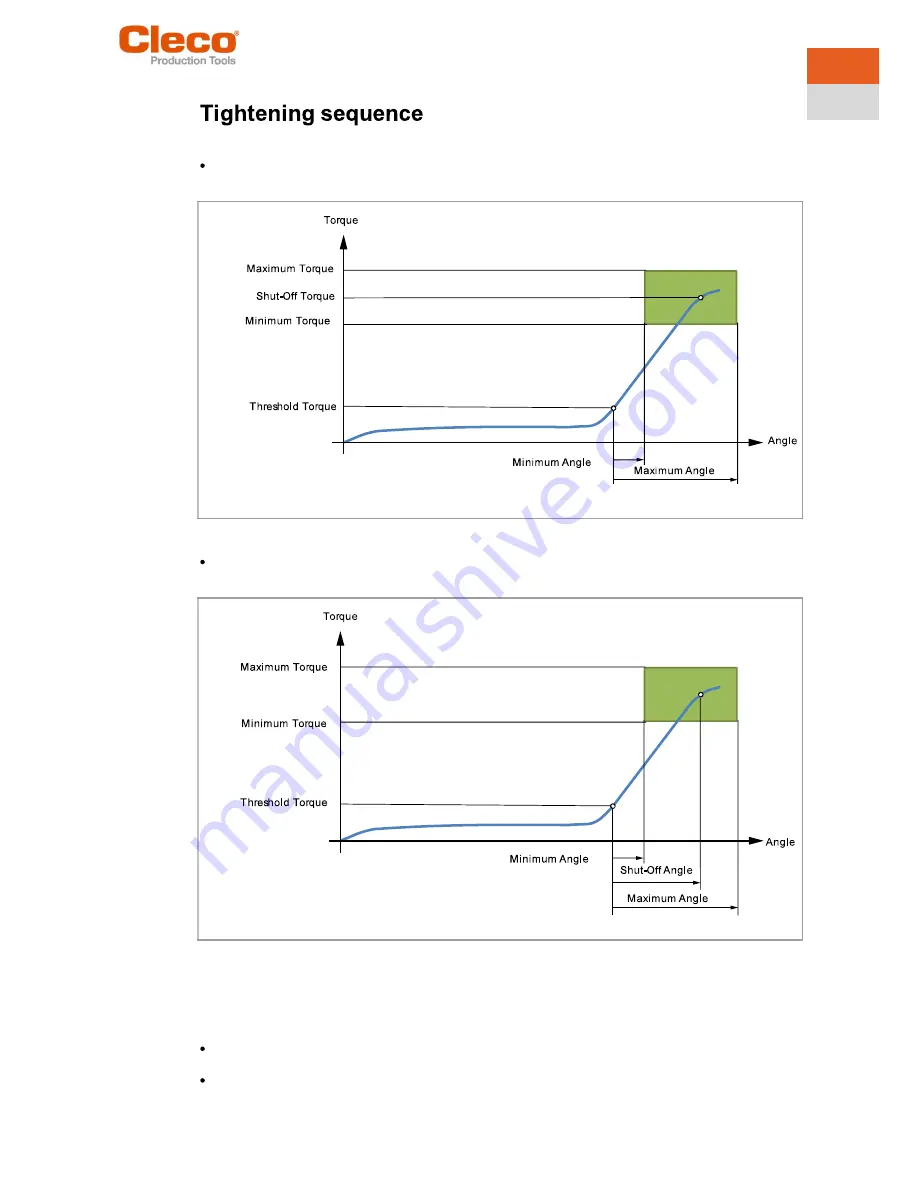
Tightening sequence
Apex Tool Group
P2398PM | 2022-07
59
4
EN
4
In the FastApps mode, there is a choice between two tightening sequences:
Torque shutoff: Sequence 31 torque controlled, extended monitoring
Shut-off torque-controlled tightening sequence with torque and angle check.
Fig. 4-1: Representation of torque shutoff
Angle shutoff: Sequence 51 angle-controlled, extended monitoring
Shut-off angle-controlled tightening sequence with angle and torque check.
Fig. 4-2: Representation of angle shut-off
The following description applies to both tightening sequences.
For the speed, select a second speed parameter
Final Speed
. The behavior at the Final Speed is different
in FastApps and mPro mode:
FastApps mode: If the
Final Speed
is programmed, the speed immediately changes from the start
speed to the final speed up to the maximum torque.
mPro mode: If the
Final Speed
is programmed, the speed is reduced from the starting speed to the
final speed starting from the threshold torque to the maximum torque.
Содержание CellCore S169262 CCBA
Страница 13: ...Menus And Functions Apex Tool Group P2398PM 2022 07 13 3 EN 3 3 Menu structure overview...
Страница 69: ......