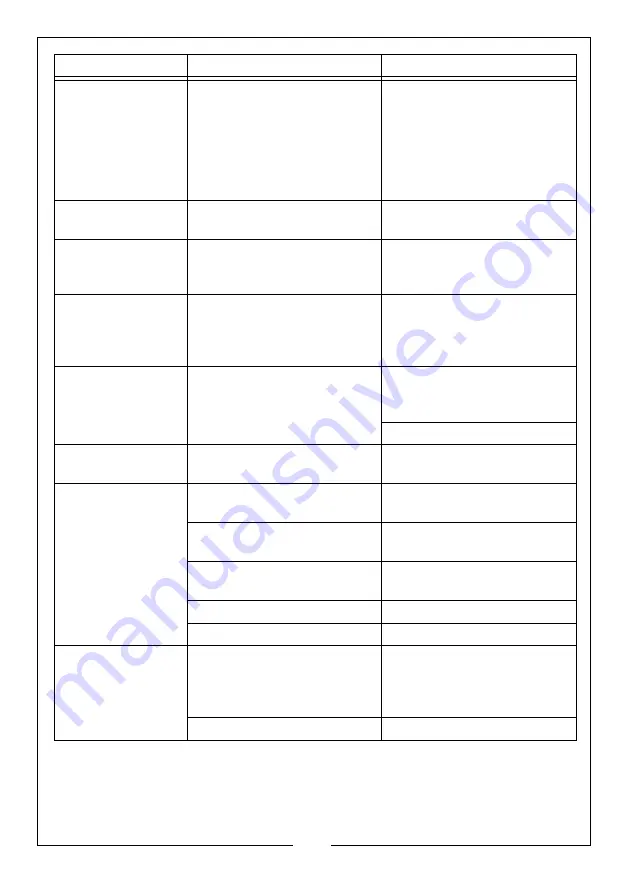
31
Parts & Service: 020 8988 7400 / E-mail: [email protected] or [email protected]
Profile defects
Welding parameters are
incorrect.
Pass rate is not related to
operating parameter
requirements.
Electrode not inclined
constantly while welding.
Follow basic and general
welding principles.
High Sprays
Electrode is too inclined.
Make appropriate
corrections.
Arc is unstable
Insufficient current.
Check condition of
electrode and earth wire
connection.
Electrode melts
obliquely
Electrode core is not
centred.
Magnetic blow
phenomenon.
Replace electrode.
Connect two earth wires
to opposite sites of the
work piece.
No response from
welder.
Check fuses and power
lead.
Replace fuses as necessary.
If problem persists return
welder to your local dealer.
Check fuse size.
Welder does not
feed wire.
Feed motor defective.
Return welder to your local
dealer.
Feed motor
running but no
wire being fed
from welder tip
Insufficient Feed Roller
pressure.
Increase roller pressure.
Burr on end of wire.
Re-cut wire square with no
burr.
Liner blocked or damaged.
Clean with compressed air
or replace liner.
Inferior wire
Use only good “clean” wire.
Roller worn out.
Replace roller.
Wire welds itself to
tip.
Wire feed speed too low.
Unscrew tip, cut wire and fit
new tip.
Increase wire speed before
operating again.
Wrong size tip.
Fit correct size tip.
DEFECT
CAUSES
SUGGESTIONS
Содержание 6015601
Страница 40: ......