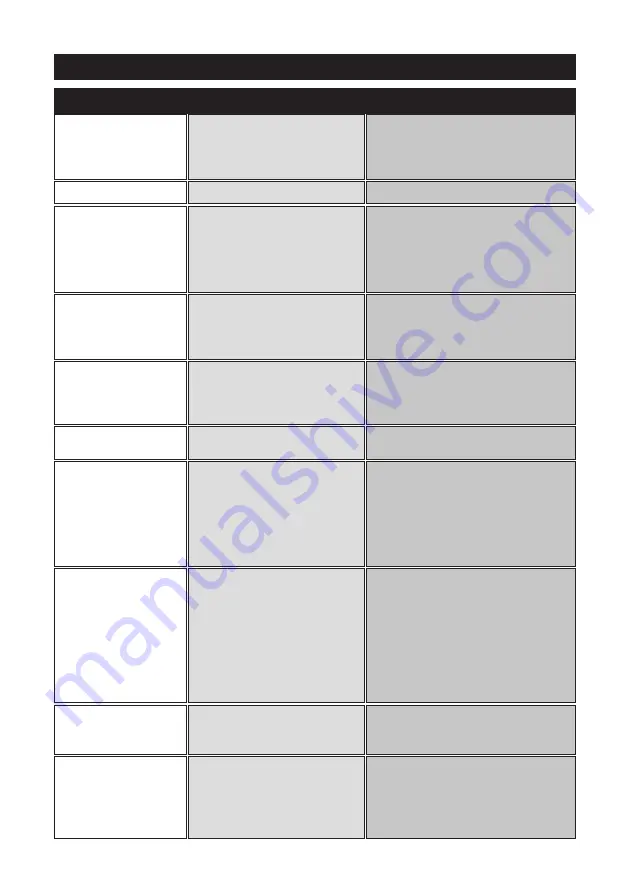
23
a) insufficient feed roller
pressure
b) Burr on end of wire
c) Liner blocked/damaged
d) Inferior wire
TROUBLE SHOOTING
1. No life from
welder
2. No wire feed
Check fuses and mains lead
a) Replace fuses as necessary.
If problem persists. return welder
to your local dealer.
b) Check fuse size.
Return welder to your local dealer.
Motor malfunction
a) Increase roller pressure
b) Re-cut wire square
c) Clear with compressed air or
replace liner.
d) Use only good dean wire
a) Unscrew tip cut wire and fit new
tip. Increase wire speed before
operating again.
b) Change tip size.
a) As above plus reduce feed roller
pressure so if blockage occurs
wire sleeps on roller. i.e. no feed
b) Renew wire liner.
Tighten drum brake DO NOT
OVERTIGHTEN
3. Feed motor
operates but wire
will not feed
4. Wire welds itself to
tip
a) Wire welded to tip.
b ) Wire liner damaged
preventing smooth
operation.
a) Wirefeed speed too low
b) Wrong size tip
5. Wire feeds into
birds nest tangle.
6. Tangled coils of
wire around drum
7. Erratic wire feed
8. Poor quality welds
9. Wire jams in tip
when welding
aluminium
Drum brake too slack.
a) Drum brake too light
b) Feed roller worn
c) Insufficient pressure on
feed roller
d) Wire dirty, rusty, damp or
bent
e) Liner partially blocked
a) Loosen drum brake slightly
b) Check and replace if necessary
c) Increase pressure on feed roller
DO NOT OVER TIGHTEN
d) Re-cut wire and ensure it is clean
e) Clear with compressed air
a) Check gas is not being blown
away by draughts, if so, move to
a sheltered area. If no draught,
increase gas supply.
b) Consult Mig Welding manual
c) Ensure wkpiece is clean and dry
d) Ensure wire is clean and dry
e) Check ground clamp/ wkpiece
connection.
Use slightly oversize tip i.e. for 0.8mm
wire use 1mm tip (Applies to
aluminium only)
Allow welder to cool for 10-30min
before continuing.
Note: If duty cycle
is continually exceeded, damage to
welder may result and welder output
is probably too small for application,
a) lnsufficient gas at weld
area
b) Incorrect gas/wire
combination
c) Rusty, painted, damp. oily
or greasy work piece
d) Rusty, dirty work.
e) Poor earth contact
Tip too small
Duty Cycle exceeded (auto
cut-out operates)
10. Welder cuts out
whilst in use
PROBLEM
PROBABLE CAUSE
REMEDY
Содержание 195TEC
Страница 1: ...MIG WELDER OPERATING MAINTENANCE INSTRUCTIONS Model Nos 195TEC 205TE 230TEC 0820 ISS6...
Страница 23: ...24 PARTS DRAWING MIG 195TEC...
Страница 25: ...26 PARTS DRAWING MIG 205TE...
Страница 27: ...28 PARTS DRAWING MIG 230TEC...
Страница 29: ...30 WIRING DIAGRAM MIG 195TEC MIG 230TEC...
Страница 30: ...WIRING DIAGRAM MIG 205TE 31...
Страница 31: ...DECLARATION OF CONFORMITY...
Страница 32: ......