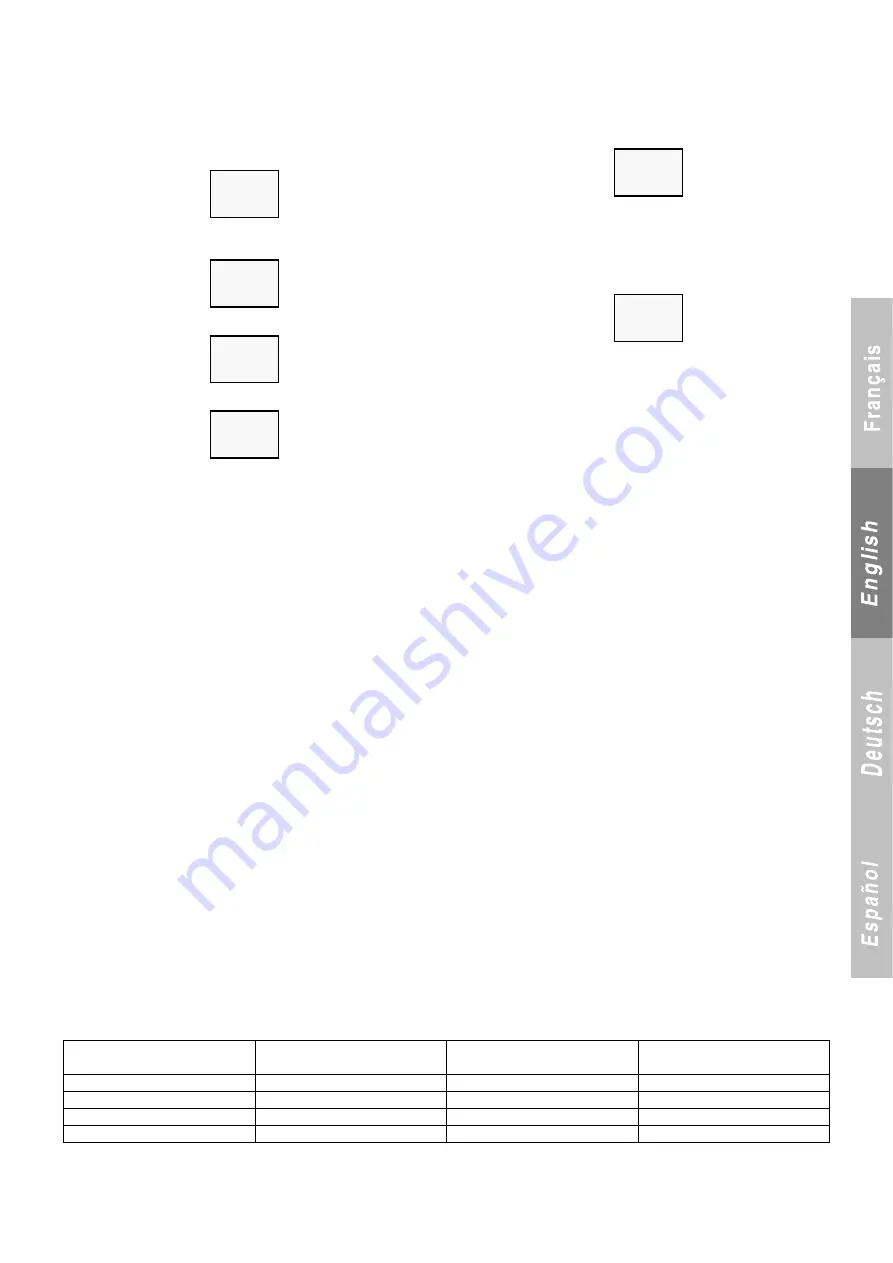
EN - 55
Code
000
Code
100
Net
3bl
COM
adr
000
COM
adr
010
COM
adr
011
22 ASSIGNING A COMMUNICATION ADDRESS TO THE DIRIS ENERGY METER
Follow the procedure described below when replacing a DIRIS
energy meter already installed on a machine.
Turn on the meter and press the PROG button for 5 seconds. The
following message is displayed:
Press the P PF button until the 0 on the left starts flashing. Press
the
▲
or
▼
button until the following screen appears:
Confirm by pressing
OK
. The following message appears:
Press the
▲
or
▼
button until the following message appears:
Now press the P PF button twice so that the 0 in the middle starts
flashing. Press
▲
or
▼
until 1 appears on the display.
If the DIRIS meter is installed on a 2-circuit machine, confirm by
pressing
OK
then exit the configuration menu by pressing the
PROG
button for 5 seconds.
If the DIRIS meter is installed on module 2 of a 3-circuit machine,
press the P PF button a third time so that the 0 on the right starts
flashing. Select 1 so that the message is as follows:
Confirm by pressing OK and exit the configuration menu by
pressing the PROG button for 5 seconds. The measured values will
appear on the display.
Now enter the measured values menu of one of the circuits and
make sure that the electrical quantities screen (last screen) appears
when P15 = Yes. If so, communication between the meter and the
controller has been established. If the screen does not appear,
check the continuity of the Bus.
23 MANAGEMENT OF THE PROTECTIONS FOR 3-CIRCUIT AIR-TO-WATER UNITS (MODULES 1
AND 2)
- A link fault between modules 1 and 2 may indicate that the RS485
cable is not connected correctly or a lack of voltage on module 2
(circuit 3 off only).
- It is recommended to energise both modules at the same time to
ensure adequate warming of the oil before starting up the machine
and to prevent the time delays on each module from activating
together.
- The oil warm-up time is activated if module 1 and module 2 do not
turn on (link fault).
- Phase controller, water flow, and water outlet faults are managed
independently for each module. They only shut off the module on
which they occur, not the entire machine.
- Water outlet sensor faults are also managed independently on the
two modules. Also, if the manifold water outlet sensor is controlled
and a fault occurs on the sensor, module 1 switches to standalone
mode and uses its own water outlet sensor to make adjustments.
Other faults (compressor, electronic expansion valve, high
pressure, low pressure, discharge, desuperheat, lubrication and
freon frost protection) are managed on the 2-circuit machines and
only affect the refrigerating circuit in question.
24. TIME SCHEDULES
24.1 Overview
This function is used to manage liquid chillers on a weekly basis by
selecting:
- 6 program steps (maximum).
- 6 holiday bands (maximum).
24.2 Definition of program steps
Settings:
- Start time,
- End time
- Selected days (M.T.W.T.F.S.S)
- Control mode: setpoint 1 - off/setpoint 2 - off/setpoint 1 - setpoint
2/setpoint 2 - setpoint 1/disabled.
Default setting:
- Start time: 00.00
- End time: 00.00
- Enabled days: none
- Control mode disabled.
24.3 Definition of holiday bands.
Settings:
- Band type: Disabled, off, operate per setpoint 1, operate per
setpoint 2.
- Start date dd-mm
- End date dd-mm
- Default setting: Disabled, from 01-01 to 01-01
24.4 Operation
- When the controller is powered up or the time is set, the unit
status information is updated to reflect the schedule settings.
- Users may change the unit's settings (on/off - setpoint 1 or 2
control). However, if a time range or holiday band is on, this
information is updated at the start or end of the schedule.
- If at least one time range or holiday band is enabled, parameter
P120 is set to '2 via console or BMS' and cannot be modified.
- The schedule is disabled when test mode is activated. The unit
status information is updated to the schedule settings when test
mode is deactivated.
- If periods or bands overlap, On takes priority over Off and setpoint
1 takes priority over setpoint 2
- If a program step is active (
#
disabled) and the current day is selected, the unit status is as follows :
Program type
State before start time
State between start time
and end time
State after end time
STP1-off
Off
Start per setpoint 1
Off
STP2-off
Off
Start per setpoint 2
Off
STP1-STP2
Start per setpoint 2
Start per setpoint 1
Start per setpoint 2
STP2-STP1
Start per setpoint 1
Start per setpoint 2
Start per setpoint 1