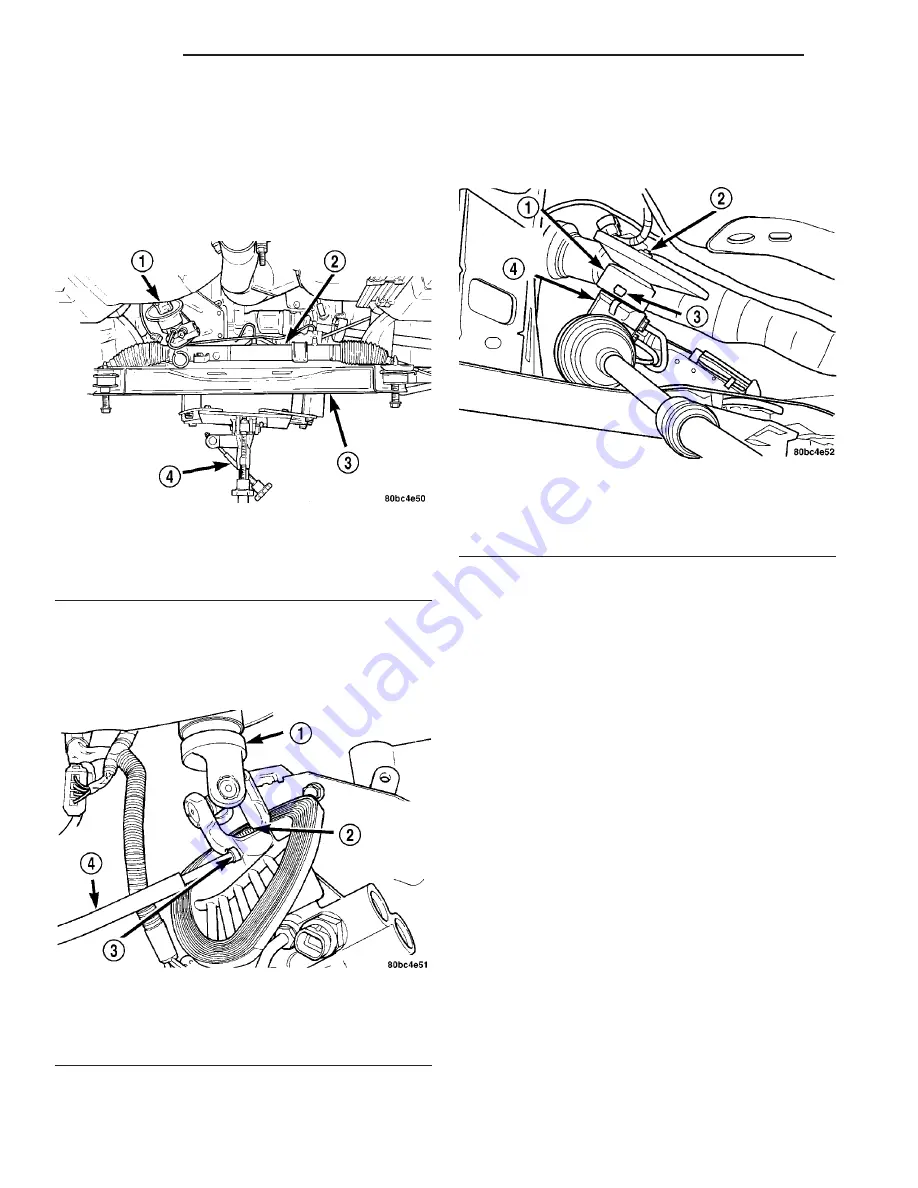
(21) Lower
the
front
suspension
crossmember
using the transmission jack enough to allow the
power steering gear to be removed from the rear of
the crossmember (Fig. 12). When lowering front sus-
pension crossmember, do not let crossmember hang
from lower control arms. The weight should be sup-
ported by the transmission jack.
(22) Remove the roll pin securing the steering col-
umn lower coupling to the power steering gear pinion
shaft using a roll pin punch (Fig. 13). Push the steer-
ing column lower coupling up and off of the power
steering gear pinion shaft.
(23) Release the pinion shaft dash cover seal from
the tabs cast into the power steering gear housing
and remove the seal from the power steering gear
(Fig. 14).
(24) Loosen and remove the four bolts attaching
the power steering gear to the front suspension cross-
member (Fig. 1). Remove the power steering gear
from the front suspension crossmember.
REMOVAL - RHD
Right-Hand-Drive power steering gear is typical of
Left-Hand-Drive. (Refer to 19 - STEERING/GEAR -
REMOVAL - LHD)
INSTALLATION
INSTALLATION
(1) Install the steering gear on the front suspen-
sion crossmember (Fig. 1). Install the four power
steering gear mounting bolts. Tighten the mounting
bolts to a torque of 61 N·m (45 ft. lbs.).
(2) Install the pinion shaft dash cover seal over
the power steering pinion shaft and onto the power
steering gear housing. Align the holes on each side of
the seal with the tabs cast into the power steering
gear housing (Fig. 14).
(3) With
the
steering
column
lower
coupling
pushed partway up through its hole in the dash
panel, match the flat on the inside of the steering
column lower coupling to the flat on the power steer-
ing gear pinion shaft and slide the coupling onto the
top of the pinion shaft. Align the roll pin hole in the
coupling with the groove in the pinion shaft and
Fig. 12 Crossmember Lowered
1 - STEERING COLUMN LOWER COUPLING
2 - POWER STEERING GEAR
3 - FRONT SUSPENSION CROSSMEMBER
4 - TRANSMISSION JACK
Fig. 13 Coupling Roll Pin
1 - STEERING COLUMN LOWER COUPLING
2 - POWER STEERING GEAR PINION SHAFT
3 - ROLL PIN
4 - ROLL PIN PUNCH
Fig. 14 Pinion Shaft Dash Cover Seal
1 - SEAL
2 - PINION SHAFT
3 - TAB
4 - POWER STEERING GEAR
19 - 32
GEAR
PT
GEAR (Continued)
Содержание PT Cruiser
Страница 2: ......
Страница 5: ...Fig 3 FASTENER IDENTIFICATION PT INTRODUCTION 3 FASTENER IDENTIFICATION Continued...
Страница 6: ...Fig 4 FASTENER STRENGTH 4 INTRODUCTION PT FASTENER IDENTIFICATION Continued...
Страница 9: ...Fig 6 METRIC CONVERSION CHART PT INTRODUCTION 7 METRIC SYSTEM Continued...
Страница 28: ......
Страница 31: ...Fig 1 Front Suspension System PT FRONT SUSPENSION 2 3 FRONT SUSPENSION Continued...
Страница 202: ......
Страница 300: ......
Страница 336: ......
Страница 382: ......
Страница 396: ......
Страница 416: ......
Страница 422: ......
Страница 456: ......
Страница 482: ......
Страница 522: ......
Страница 542: ......
Страница 544: ......
Страница 546: ...Fig 1 WIRING DIAGRAM EXAMPLE 1 8W 01 2 8W 01 WIRING DIAGRAM INFORMATION PT WIRING DIAGRAM INFORMATION Continued...
Страница 547: ...Fig 2 WIRING DIAGRAM EXAMPLE 2 PT 8W 01 WIRING DIAGRAM INFORMATION 8W 01 3 WIRING DIAGRAM INFORMATION Continued...
Страница 548: ...Fig 3 WIRING DIAGRAM SYMBOLS 8W 01 4 8W 01 WIRING DIAGRAM INFORMATION PT WIRING DIAGRAM INFORMATION Continued...
Страница 560: ......
Страница 564: ......
Страница 565: ......
Страница 566: ......
Страница 567: ......
Страница 568: ......
Страница 569: ......
Страница 570: ......
Страница 571: ......
Страница 572: ......
Страница 573: ......
Страница 574: ......
Страница 575: ......
Страница 576: ......
Страница 577: ......
Страница 578: ......
Страница 579: ......
Страница 580: ......
Страница 581: ......
Страница 582: ......
Страница 583: ......
Страница 584: ......
Страница 585: ......
Страница 586: ......
Страница 587: ......
Страница 588: ......
Страница 589: ......
Страница 590: ......
Страница 591: ......
Страница 592: ......
Страница 593: ......
Страница 594: ......
Страница 596: ......
Страница 597: ......
Страница 598: ......
Страница 599: ......
Страница 600: ......
Страница 601: ......
Страница 602: ......
Страница 603: ......
Страница 604: ......
Страница 605: ......
Страница 606: ......
Страница 607: ......
Страница 608: ......
Страница 609: ......
Страница 610: ......
Страница 611: ......
Страница 612: ......
Страница 613: ......
Страница 614: ......
Страница 616: ......
Страница 617: ......
Страница 618: ......
Страница 619: ......
Страница 620: ......
Страница 621: ......
Страница 622: ......
Страница 623: ......
Страница 624: ......
Страница 625: ......
Страница 626: ......
Страница 627: ......
Страница 628: ......
Страница 629: ......
Страница 630: ......
Страница 631: ......
Страница 632: ......
Страница 633: ......
Страница 634: ......
Страница 635: ......
Страница 636: ......
Страница 637: ......
Страница 638: ......
Страница 639: ......
Страница 640: ......
Страница 641: ......
Страница 642: ......
Страница 644: ......
Страница 645: ......
Страница 646: ......
Страница 647: ......
Страница 648: ......
Страница 650: ......
Страница 651: ......
Страница 652: ......
Страница 653: ......
Страница 654: ......
Страница 655: ......
Страница 656: ......
Страница 658: ......
Страница 659: ......
Страница 660: ......
Страница 662: ......
Страница 663: ......
Страница 664: ......
Страница 665: ......
Страница 666: ......
Страница 667: ......
Страница 668: ......
Страница 669: ......
Страница 670: ......
Страница 671: ......
Страница 672: ......
Страница 673: ......
Страница 674: ......
Страница 675: ......
Страница 676: ......
Страница 677: ......
Страница 678: ......
Страница 679: ......
Страница 680: ......
Страница 681: ......
Страница 682: ......
Страница 683: ......
Страница 684: ......
Страница 685: ......
Страница 686: ......
Страница 687: ......
Страница 688: ......
Страница 689: ......
Страница 690: ......
Страница 691: ......
Страница 692: ......
Страница 693: ......
Страница 694: ......
Страница 695: ......
Страница 696: ......
Страница 697: ......
Страница 698: ......
Страница 699: ......
Страница 700: ......
Страница 701: ......
Страница 702: ......
Страница 703: ......
Страница 704: ......
Страница 705: ......
Страница 706: ......
Страница 707: ......
Страница 708: ......
Страница 709: ......
Страница 710: ......
Страница 712: ......
Страница 713: ......
Страница 714: ......
Страница 715: ......
Страница 716: ......
Страница 717: ......
Страница 718: ......
Страница 720: ......
Страница 721: ......
Страница 722: ......
Страница 723: ......
Страница 724: ......
Страница 725: ......
Страница 726: ......
Страница 728: ......
Страница 729: ......
Страница 730: ......
Страница 732: ......
Страница 733: ......
Страница 734: ......
Страница 735: ......
Страница 736: ......
Страница 737: ......
Страница 738: ......
Страница 739: ......
Страница 740: ......
Страница 741: ......
Страница 742: ......
Страница 743: ......
Страница 744: ......
Страница 746: ......
Страница 747: ......
Страница 748: ......
Страница 749: ......
Страница 750: ......
Страница 751: ......
Страница 752: ......
Страница 753: ......
Страница 754: ......
Страница 755: ......
Страница 756: ......
Страница 757: ......
Страница 758: ......
Страница 759: ......
Страница 760: ......
Страница 761: ......
Страница 762: ......
Страница 764: ......
Страница 765: ......
Страница 766: ......
Страница 768: ......
Страница 769: ......
Страница 770: ......
Страница 771: ......
Страница 772: ......
Страница 773: ......
Страница 774: ......
Страница 775: ......
Страница 776: ......
Страница 778: ......
Страница 779: ......
Страница 780: ......
Страница 781: ......
Страница 782: ......
Страница 784: ......
Страница 785: ......
Страница 786: ......
Страница 787: ......
Страница 788: ......
Страница 790: ......
Страница 791: ......
Страница 792: ......
Страница 794: ......
Страница 796: ......
Страница 797: ......
Страница 798: ......
Страница 800: ......
Страница 801: ......
Страница 802: ......
Страница 803: ......
Страница 804: ......
Страница 805: ......
Страница 806: ......
Страница 807: ......
Страница 808: ......
Страница 810: ......
Страница 811: ......
Страница 812: ......
Страница 813: ......
Страница 814: ......
Страница 815: ......
Страница 816: ......
Страница 817: ......
Страница 818: ......
Страница 820: ......
Страница 821: ......
Страница 822: ......
Страница 823: ......
Страница 824: ......
Страница 826: ......
Страница 827: ......
Страница 828: ......
Страница 830: ......
Страница 831: ......
Страница 832: ......
Страница 833: ......
Страница 834: ......
Страница 836: ......
Страница 837: ......
Страница 838: ......
Страница 839: ......
Страница 840: ......
Страница 841: ......
Страница 842: ......
Страница 843: ......
Страница 844: ......
Страница 846: ......
Страница 847: ......
Страница 848: ......
Страница 849: ......
Страница 850: ......
Страница 851: ......
Страница 852: ......
Страница 854: ......
Страница 855: ......
Страница 856: ......
Страница 857: ......
Страница 858: ......
Страница 860: ......
Страница 862: ......
Страница 863: ......
Страница 864: ......
Страница 985: ...Fig 20 DIESEL ENGINE PT 8W 91 CONNECTOR GROUND SPLICE LOCATION 8W 91 29 CONNECTOR GROUND SPLICE LOCATION Continued...
Страница 987: ...Fig 22 2 0L 2 4L ENGINE PT 8W 91 CONNECTOR GROUND SPLICE LOCATION 8W 91 31 CONNECTOR GROUND SPLICE LOCATION Continued...
Страница 1000: ...Fig 35 INSTRUMENT PANEL JUMPER 8W 91 44 8W 91 CONNECTOR GROUND SPLICE LOCATION PT CONNECTOR GROUND SPLICE LOCATION Continued...
Страница 1001: ...Fig 36 CENTER CONSOLE PT 8W 91 CONNECTOR GROUND SPLICE LOCATION 8W 91 45 CONNECTOR GROUND SPLICE LOCATION Continued...
Страница 1002: ...Fig 37 SUNROOF 8W 91 46 8W 91 CONNECTOR GROUND SPLICE LOCATION PT CONNECTOR GROUND SPLICE LOCATION Continued...
Страница 1003: ...Fig 38 FRONT DOOR EXCEPT EXPORT PT 8W 91 CONNECTOR GROUND SPLICE LOCATION 8W 91 47 CONNECTOR GROUND SPLICE LOCATION Continued...
Страница 1004: ...Fig 39 FRONT DOOR EXPORT 8W 91 48 8W 91 CONNECTOR GROUND SPLICE LOCATION PT CONNECTOR GROUND SPLICE LOCATION Continued...
Страница 1005: ...Fig 40 REAR DOOR PT 8W 91 CONNECTOR GROUND SPLICE LOCATION 8W 91 49 CONNECTOR GROUND SPLICE LOCATION Continued...
Страница 1006: ...Fig 41 RIGHT FRONT BODY 8W 91 50 8W 91 CONNECTOR GROUND SPLICE LOCATION PT CONNECTOR GROUND SPLICE LOCATION Continued...
Страница 1007: ...Fig 42 RIGHT REAR BODY PT 8W 91 CONNECTOR GROUND SPLICE LOCATION 8W 91 51 CONNECTOR GROUND SPLICE LOCATION Continued...
Страница 1008: ...Fig 43 RIGHT REAR QUARTER 8W 91 52 8W 91 CONNECTOR GROUND SPLICE LOCATION PT CONNECTOR GROUND SPLICE LOCATION Continued...
Страница 1011: ...Fig 48 BATTERY DIESEL PT 8W 91 CONNECTOR GROUND SPLICE LOCATION 8W 91 55 CONNECTOR GROUND SPLICE LOCATION Continued...
Страница 1012: ...Fig 49 FUEL TANK 8W 91 56 8W 91 CONNECTOR GROUND SPLICE LOCATION PT CONNECTOR GROUND SPLICE LOCATION Continued...
Страница 1078: ...Fig 92 Oil Lubrication System 9 58 ENGINE 1 6L SOHC PT LUBRICATION Continued...
Страница 1287: ...Fig 7 ENGINE COMPARTMENT SIDE AND BOTTOM VIEW PT FRAMES BUMPERS 13 5 FRAME Continued...
Страница 1288: ...Fig 8 REAR FRAME SECTION SIDE AND BOTTOM VIEW 13 6 FRAMES BUMPERS PT FRAME Continued...
Страница 1289: ...Fig 9 WINDSHIELD OPENING DIMENSIONS Fig 10 FRONT AND REAR DOOR OPENING DIMENSIONS PT FRAMES BUMPERS 13 7 FRAME Continued...
Страница 1296: ......
Страница 1412: ......
Страница 1616: ...Neutral Speed Over 8 MPH 21 204 41TE AUTOMATIC TRANSAXLE PT 41TE AUTOMATIC TRANSAXLE Continued...
Страница 1617: ...Reverse PT 41TE AUTOMATIC TRANSAXLE 21 205 41TE AUTOMATIC TRANSAXLE Continued...
Страница 1618: ...Reverse Block Shift to Reverse W Speed Over 8 mph 21 206 41TE AUTOMATIC TRANSAXLE PT 41TE AUTOMATIC TRANSAXLE Continued...
Страница 1619: ...First Gear PT 41TE AUTOMATIC TRANSAXLE 21 207 41TE AUTOMATIC TRANSAXLE Continued...
Страница 1620: ...Second Gear 21 208 41TE AUTOMATIC TRANSAXLE PT 41TE AUTOMATIC TRANSAXLE Continued...
Страница 1621: ...Second Gear EMCC PT 41TE AUTOMATIC TRANSAXLE 21 209 41TE AUTOMATIC TRANSAXLE Continued...
Страница 1622: ...Direct Gear 21 210 41TE AUTOMATIC TRANSAXLE PT 41TE AUTOMATIC TRANSAXLE Continued...
Страница 1623: ...Direct Gear CC On PT 41TE AUTOMATIC TRANSAXLE 21 211 41TE AUTOMATIC TRANSAXLE Continued...
Страница 1624: ...Overdrive 21 212 41TE AUTOMATIC TRANSAXLE PT 41TE AUTOMATIC TRANSAXLE Continued...
Страница 1625: ...Overdrive EMCC PT 41TE AUTOMATIC TRANSAXLE 21 213 41TE AUTOMATIC TRANSAXLE Continued...
Страница 1626: ...Overdrive CC On 21 214 41TE AUTOMATIC TRANSAXLE PT 41TE AUTOMATIC TRANSAXLE Continued...
Страница 1723: ...PT TIRES WHEELS 22 11 TIRES Continued...
Страница 1779: ...Fig 15 INSTRUMENT PANEL ASSEMBLY PT INSTRUMENT PANEL 23 51 INSTRUMENT PANEL ASSEMBLY Continued...
Страница 1826: ...Fig 3 WINDSHIELD OPENINGS Fig 4 REAR WINDOW AND LIFTGATE OPENINGS 23 98 BODY STRUCTURE PT OPENING DIMENSIONS Continued...
Страница 1828: ...Fig 5 BODY LOCATIONS 23 100 BODY STRUCTURE PT SEALER LOCATIONS Continued...
Страница 1829: ...Fig 6 LOAD BEAM STRUT TOWER COWL and DASH PANEL 1 THUMBGRADE SEALER PT BODY STRUCTURE 23 101 SEALER LOCATIONS Continued...
Страница 1830: ...Fig 7 COWL and DASH PANEL 1 SPRAYABLE NON PAINTABLE SEALER 23 102 BODY STRUCTURE PT SEALER LOCATIONS Continued...
Страница 1831: ...Fig 8 FLOOR PAN and DASH PANEL 1 SPRAYABLE NON PAINTABLE SEALER PT BODY STRUCTURE 23 103 SEALER LOCATIONS Continued...
Страница 1832: ...Fig 9 ROOF 1 THUMBGRADE SEALER 23 104 BODY STRUCTURE PT SEALER LOCATIONS Continued...
Страница 1833: ...Fig 10 INNER WHEELHOUSE 1 SPRAYABLE NON PAINTABLE SEALER PT BODY STRUCTURE 23 105 SEALER LOCATIONS Continued...
Страница 1834: ...Fig 11 COWL PLENUM 1 PUMPABLE SEALER 23 106 BODY STRUCTURE PT SEALER LOCATIONS Continued...
Страница 1836: ...Fig 13 COWL PLENUM and DASH PANEL 1 EXPANDABLE SEALER 23 108 BODY STRUCTURE PT SEALER LOCATIONS Continued...
Страница 1837: ...Fig 14 COWL SIDE 1 PUMPABLE SEALER PT BODY STRUCTURE 23 109 SEALER LOCATIONS Continued...
Страница 1838: ...Fig 15 BODY SIDE APERTURE 1 SEALER TAPE 2 THUMBGRADE SEALER 3 PUMPABLE SEALER 23 110 BODY STRUCTURE PT SEALER LOCATIONS Continued...
Страница 1840: ...Fig 17 REAR FLOOR PAN 1 PUMPABLE SEALER 23 112 BODY STRUCTURE PT SEALER LOCATIONS Continued...
Страница 1841: ...Fig 18 CARGO AREA 1 SEALER TAPE 2 THUMBGRADE SEALER PT BODY STRUCTURE 23 113 SEALER LOCATIONS Continued...
Страница 1844: ...Fig 20 DASH PANEL AND FLOOR PAN 1 STRUCTURAL ADHESIVE TAPE 23 116 BODY STRUCTURE PT STRUCTURAL ADHESIVE LOCATIONS Continued...
Страница 1845: ...Fig 21 REAR FLOOR PAN 1 STRUCTURAL ADHESIVE TAPE PT BODY STRUCTURE 23 117 STRUCTURAL ADHESIVE LOCATIONS Continued...
Страница 1852: ...Fig 26 FRONT SIDE RAIL REAR TO DASH AND COWL SIDE PANELS 1 WELDING OF TWO PARTS 23 124 BODY STRUCTURE PT WELD LOCATIONS Continued...
Страница 1854: ...Fig 28 STRUT TOWER TO DASH PANEL 1 WELDING OF TWO PARTS 23 126 BODY STRUCTURE PT WELD LOCATIONS Continued...
Страница 1856: ...Fig 30 COWL TOP TO COWL PLENUM 1 WELDING OF TWO PARTS 23 128 BODY STRUCTURE PT WELD LOCATIONS Continued...
Страница 1857: ...Fig 31 COWL PLENUM TO DASH PANEL 1 WELDING OF TWO PARTS PT BODY STRUCTURE 23 129 WELD LOCATIONS Continued...
Страница 1858: ...Fig 32 COWL PLENUM TO COWL SIDE PANEL 1 WELDING OF TWO PARTS 23 130 BODY STRUCTURE PT WELD LOCATIONS Continued...
Страница 1859: ...Fig 33 OUTER LOAD BEAM TO COWL SIDE PANEL 1 WELDING OF TWO PARTS PT BODY STRUCTURE 23 131 WELD LOCATIONS Continued...
Страница 1861: ...Fig 35 WINDSHIELD WIPER REINFORCEMENT GUSSET 1 WELDING OF TWO PARTS PT BODY STRUCTURE 23 133 WELD LOCATIONS Continued...
Страница 1862: ...Fig 36 INSTRUMENT PANEL REINFORCEMENT TO COWL SIDE PANEL 1 WELDING OF TWO PARTS 23 134 BODY STRUCTURE PT WELD LOCATIONS Continued...
Страница 1863: ...Fig 37 COWL PLENUM WATER DEFLECTOR TO COWL PLENUM PANEL 1 WELDING OF TWO PARTS PT BODY STRUCTURE 23 135 WELD LOCATIONS Continued...
Страница 1865: ...Fig 39 BRAKE PEDAL SUPPORT BRACKET TO COWL PLENUM 1 WELDING OF TWO PARTS PT BODY STRUCTURE 23 137 WELD LOCATIONS Continued...
Страница 1866: ...Fig 40 FRONT FLOOR PAN TO DASH PANEL AND COWL SIDE PANEL 1 WELDING OF TWO PARTS 23 138 BODY STRUCTURE PT WELD LOCATIONS Continued...
Страница 1871: ...Fig 45 FRONT HINGE PILLAR TO BODY SIDE APERTURE PANEL 1 WELDING OF TWO PARTS PT BODY STRUCTURE 23 143 WELD LOCATIONS Continued...
Страница 1875: ...Fig 49 INNER QUARTER PANEL TO BODY SIDE APERTURE PANEL 1 WELDING OF TWO PARTS PT BODY STRUCTURE 23 147 WELD LOCATIONS Continued...
Страница 1878: ...Fig 52 OUTER LOAD BEAM TO FRONT HINGE PILLAR 1 WELDING OF TWO PARTS 23 150 BODY STRUCTURE PT WELD LOCATIONS Continued...
Страница 1880: ...Fig 54 INNER QUARTER PANEL TO LIFTGATE SIDE DRAIN TROUGH 1 WELDING OF TWO PARTS 23 152 BODY STRUCTURE PT WELD LOCATIONS Continued...
Страница 1883: ...Fig 57 INNER B PILLAR TO INNER ROOF SIDE REINFORCEMENT 1 WELDING OF TWO PARTS PT BODY STRUCTURE 23 155 WELD LOCATIONS Continued...
Страница 1885: ...Fig 59 UPPER INNER C PILLAR TO INNER QUARTER PANEL 1 WELDING OF TWO PARTS PT BODY STRUCTURE 23 157 WELD LOCATIONS Continued...
Страница 1895: ...Fig 69 D S I BEAM TO FRONT FLOOR PAN AND INNER SIDE SILL 1 WELDING OF TWO PARTS PT BODY STRUCTURE 23 167 WELD LOCATIONS Continued...
Страница 1896: ...Fig 70 D S I BEAM TO FRONT FLOOR PAN AND INNER SIDE SILL 1 WELDING OF TWO PARTS 23 168 BODY STRUCTURE PT WELD LOCATIONS Continued...
Страница 1935: ...Fig 29 Blower Motor Electrical Diagnosis PT HEATING AIR COND LHD 24 29 BLOWER MOTOR Continued...
Страница 1990: ...Fig 28 BLOWER MOTOR ELECTRICAL DIAGNOSIS 24 84 HEATING AIR COND RHD PT BLOWER MOTOR Continued...
Страница 2044: ......
Страница 2078: ...Dealer Technical Operations 800 Chrysler Drive CIMS 486 02 76 Auburn Hills MI 48326 2757...