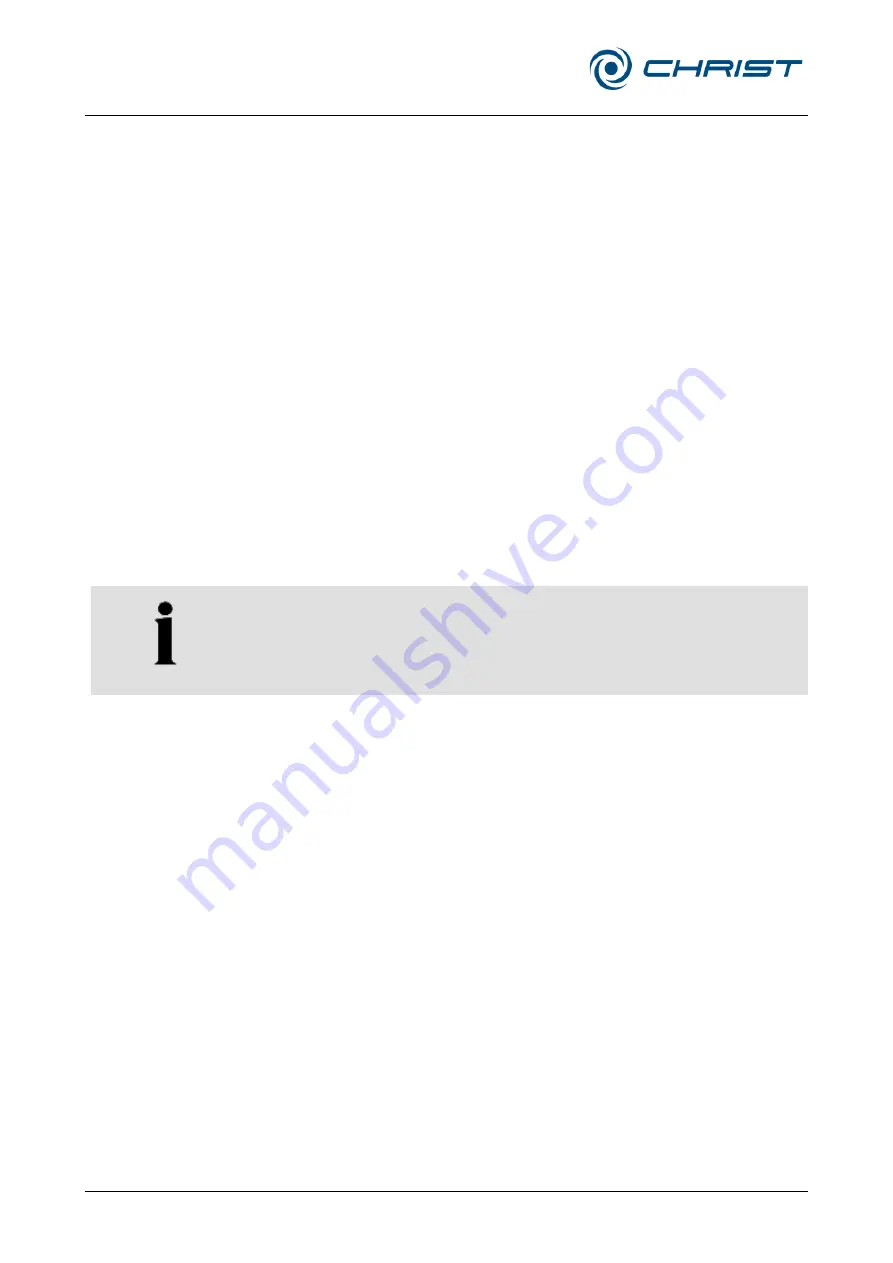
Freeze-dryer Alpha 3-4 LSCbasic
2 Layout and mode of operation
22 / 117
Version 11/2018, Rev. 1.9 of 01/12/2021
• sb
Translation of the original operating manuel
At the same time, the ice condenser is pre-cooled ("cool-down"). The ice
condenser temperature does not have any influence on the product
temperature. The sole purpose of the ice condenser is to bind the released
water vapour.
Pos : 30 / 010 U nivers almodule/ Leerz eile @ 0\m od_1202116244500_0. doc x @ 114 @ @ 1
Pos : 31 / 200 C hrist/ 361 GT-BA Labor-Pilot (PR OJEKT E)/Al pha/ Alpha 1-4_2- 4_3-4 Standard/Al pha 3-4 LSC basic /020 Auf bau und Wirkungsweis e/ 020- 0020-0020-0020 Gefrieren ( Lös ungsmittel zul ässig) Al pha 3- 4 LSC basi c @ 61\m od_1541587654730_68.docx @ 603248 @ 4 @ 1
→
2.2.2.2
Freezing
First, the product that is to be dried is frozen. Especially in the case of small
filling quantities, we recommend pre-cooling the shelves as well in order to
prevent the product from thawing during the evacuation.
Two very different structures of the frozen material can be distinguished:
•
crystalline structures with clearly distinguishable crystals
•
amorphous structures with no crystal junctions at all (e.g. glass)
The majority of the freeze-drying products have a crystalline form.
When freezing these kinds of products, one must take into consideration
that too deep and too quick freezing leads to smaller ice crystals, which has
a negative effect on the duration of the drying process.
For every product to be dried, the solidification point must be determined as
a first step. This is the point at which the water that is contained in the
product has completely crystallised. In order to ensure an optimum freeze-
drying process, the product temperature should be approximately 10°C
below the solidification point.
NOTE
In the case of a solvent-containing product or of a product with a high salt
concentration, the product may thaw during the freeze-drying process.
This is indicated by easily visible foaming. To prevent this, the product
must be frozen down to a very deep temperature, e.g. in liquid nitrogen,
prior to placing it in the freeze-dryer.
Pos : 32 / 010 U nivers almodule/ Leerz eile @ 0\m od_1202116244500_0. doc x @ 114 @ @ 1
Pos : 33 / 200 C hrist/ 360 GT-BA Labor-Pilot (ST ANDARDM ODU LE)/ 020 Auf bau und Wirk ungsw eise/020-0020-0020- 0030 Haupttrocknung @ 25\m od_1404983259260_68. docx @ 183117 @ 4 @ 1
→
2.2.2.3
Main drying
When the product is frozen, the main drying phase commences. The
vacuum pump is switched on. The pressure inside the drying chamber will
be lowered to the value that corresponds to the freezing temperature in
accordance with the vapour pressure curve for ice and water (sublimation
pressure curve). At the same time, thermal energy will be added to the
product. In the case of products in round-bottom flasks, wide-neck bottles,
etc., this is realised through the environment that is considerably warmer
(direct contact heat), in the case of unheated shelves by way of thermal
radiation from the environment, and in the case of temperature-controlled
shelves directly via the shelves. As a result, the sublimation process starts.
At the beginning of the drying process, the maximum drying rate will be
reached. The more the sublimation area recedes into the product, the
further the produced water vapour must pass through the layers that have
already been dried.
Under certain conditions, it is possible that the vacuum inside the ice
condenser chamber increases during the main drying phase (e.g. from 0.63
mbar to 0.47 mbar) although the valve towards the vacuum pump is closed.
From a physical point of view, this is due to the pumping effect of the ice
condenser ("cryo-pumping effect").