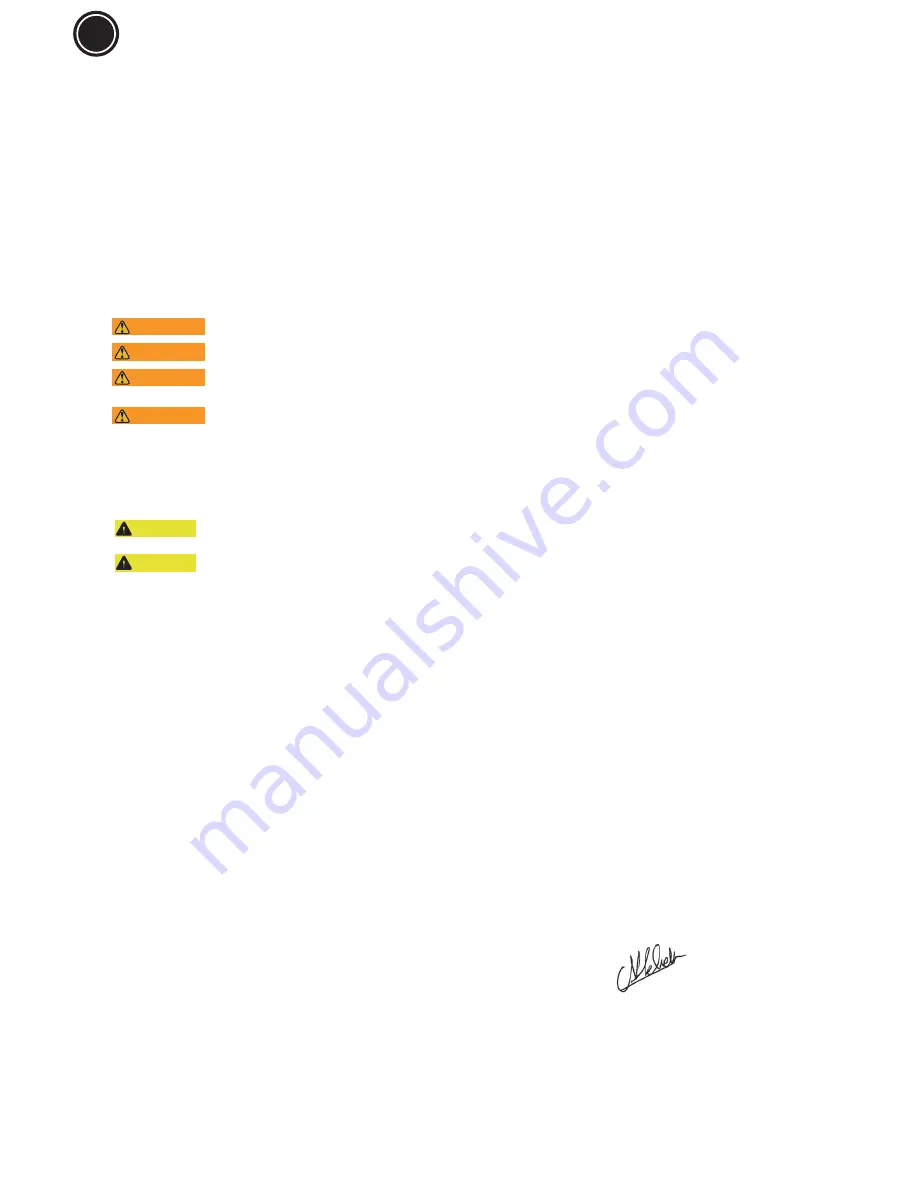
5. Maintenance instruction
Document Ref: 8940169914_REV: 01 _ 05-2012
Scale: 1:1
Caution
Do not use damaged/deformed product. If abnormal noise or vibration occurs, stop use immediately, then inspect and ask
manufacturer for help.It is recommended that this inspection be made by a manufacturer’s or supplier’s authorized repair facility.
Document Ref: 8940169914_REV: 01 _ 05-2012
Scale: 1:1
Caution
The greatest single cause of failure in hydraulic units is dirt.
Keep the service jack clean and well lubricated
to prevent foreign matter from entering the system. If the jack has been exposed to rain, snow, sand, or grit, it must be cleaned before it is
used.
Store the jack, with pistons completely retracted, in a well-protected area where it will not be exposed to corrosive vapors, abrasive dust, or
any other harmful elements.
Periodically check the condition of the product.
Store the product in dry and non-corrosion environment.
Owners and/or operators should be aware that repair of this equipment may require specialized knowledge and facilities. It is recommended
that an annual inspection of the product be made by a manufacturer’s or supplier’s authorized repair facility and that any defective parts,
decals, or safety labels or signs be replaced with manufacturer’s or supplier’s specified parts. A list of authorized repair facilities is available
from the manufacturer or supplier, please call them for help.
Any product that appears to be damaged in any way, is found to be worn, or operates abnormally SHALL BE REMOVED FROM SERVICE
UNTIL REPAIRED. It is recommended that necessary repairs be made by a manufacturer’s or supplier’s authorized repair facility if repairs
are permitted by the manufacturer or supplier.
Only attachments and/or adapters supplied by the manufacturer shall be used.
Original Instructions are in English. Other languages are a translation of the original instructions.
Copyright 2015, Chicago Pneumatic Tools
All rights reserved. Any unauthorized use or copying of the contents or part thereof is prohibited. This applies in particular to trademarks, model
denominations, part numbers and drawings. Use only authorized parts. Any damage or malfunction caused by the use of unauthorized parts is
not covered by Warranty or Product Liability.
4.2 Operation Instruction for CP86100
4.2.1 Two ways of operation:
• Operate manually: Insert the handle tube (50) into the handle sockets. 2 handle sockets are provided. The upper one(P31) is for high
pressure and low speed; and the lower one(P43) is for low pressure and faster speed. Fig.12.
• Operate by air: Depress the air foot valve(61,Fig.08)
4.2.2 Piston‘s retraction and Extension
• 3 positions for the handle lever of selector valve: When it is in position 1, the piston rod is retracting;When it is in position 2, the piston rod is
stopping moving;When it is in position 3, the piston rod is extending. Fig.13
4.2.3 Operation
• Turn the handle lever (99) to position 3, then depress the air foot valve (P54), and the piston rod will extend quickly.Warning:NEVER operate
manually (Manual Low Pressure) simultaneously.
• When the serrated saddle gets close to the work piece, change to manual operation.
• Adjust the position of work piece to make sure the work piece and piston rod are aligned properly.
• Start to press the work piece. Insert the handle tube into the high pressure socket (P31) and pump the handle tube, the piston rod extends
slowly and press the work piece. Operator can press by air ,or press by air and manually simultaneously.
• Release the pressure: turn the handle lever (99) to position 2, the pressure on the piston rod will release automatically.
• Retraction of pistion rod:turn the handle lever (99) to position 1, operate by air or manual.NEVER operate manually (Manual Low Pressure)
at the same time.
• When complete, disconnect the air hose from the compressor and clean the machine.
WARNING
Do not exceed the working load limit / rated capacity of the dolly.
WARNING
Make sure that the operator must wear protective cloth, gloves, safety helmet, shoes and ear protector during operating.
WARNING
To avoid accidents, always be aware of any on-going work on the machine. Also, always stay focused on the job to be
done.
WARNING
The product and its accessories must not be modified.
EN
English
CP86750/CP86100
Hydraulic press
7. Declaration of conformity
We :
CHICAGO PNEUMATIC Tool Co. 1800 Overview Drive Rock Hill, SC 29730 - USA
Declare that the product(s):
CP86750/CP86100
Serial: 00001 to 99999
Machine type(s):
Hydraulic press
Origin of the product:
China
is in conformity with the requirements of the council Directives on the approximation of the laws of the Member States relating : to
“Machinery“
2006/42/EC (17/05/2006)
applicable harmonised standard(s) :
EN 693
Name and position of issuer:
Nicolas Lebreton ( R&D Manager)
Place & Date:
Saint-Herblain, 10/04/2015
Technical file available from EU headquarter. Nicolas Lebreton R&D manager CP Technocenter 38, rue Bobby Sands - BP10273 44800 Saint
Herblain - France
The design has been validated according to: ASME ASP-2010
Содержание CP86100
Страница 2: ...V block Frame Table Pin Feet Fig 01 Fig 02 Fig 03 Fig 04 Fig 05 Fig 06 ...
Страница 3: ...Fig 12 Fig 13 Oil Hose A A B B C C Air bleed Valve Release Valve Fig 07 Fig 08 Fig 09 Fig 10 Fig 11 ...
Страница 4: ...FIG 15 Fig 03 Fig 14 FIG 16 OK NOK 1000 1000 1000 1000 Fig 17 Fig 18 ...
Страница 62: ...Internet www cp com ...