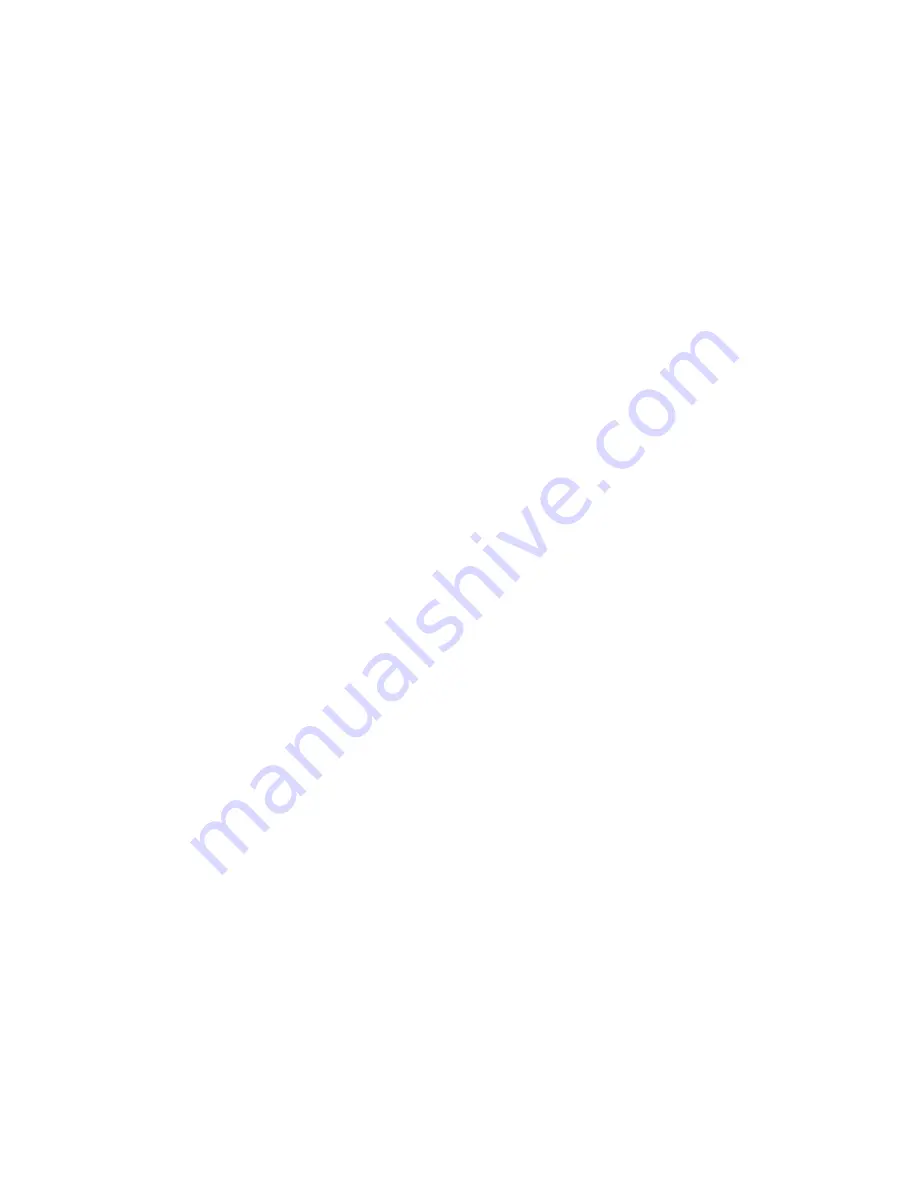
Page 6
4
Operation of the instrument
4.1 Connecting up the microDAQ.
The microDAQ has one connector and cable which supplies the unit with power and also provides
CAN and Ethernet comms. Ensure all the connections are made before powering up the
microDAQ.
The microDAQ should not be hot plugged with the power connector. Doing so can
cause permanent damage to the unit. Always switch the power at the power supply source.
Upon power up, the blue LED will light constantly while the microDAQ boots up. This boot-up
period will vary depending on the type of scanner and the number of channels. The boot up time is
also influenced by the Ethernet initialisation process. This process requires a valid network
connection to perform auto negotiation and link check status. If there isn’t a valid connection the
process waits until either a network is found or the timeout occurs. This timeout is configurable via
setup and ranges from 0 to 30 secs per check (2 checks).
When the microDAQ has finished booting, the blue LED will flash at a constant rate to show that
the system is running (unless auto hardware trigger enable has been set – see later).
4.3 Re-zeroing the microDAQ.
Before any measurements are made, the microDAQ should be re-zeroed. The microDAQ may
need further re-zeroing if the unit or scanner should be subject to significant thermal variations.
The microDAQ is re-zeroed by sending the appropriate command over the CAN or Ethernet link via
the Chell software. The system will then average a number of zero readings and perform a re-zero.
Naturally, there should be no pressure applied to the ports of the scanner when a re-zero is being
performed.
When a re-zero is being performed, the red LED will light momentarily.