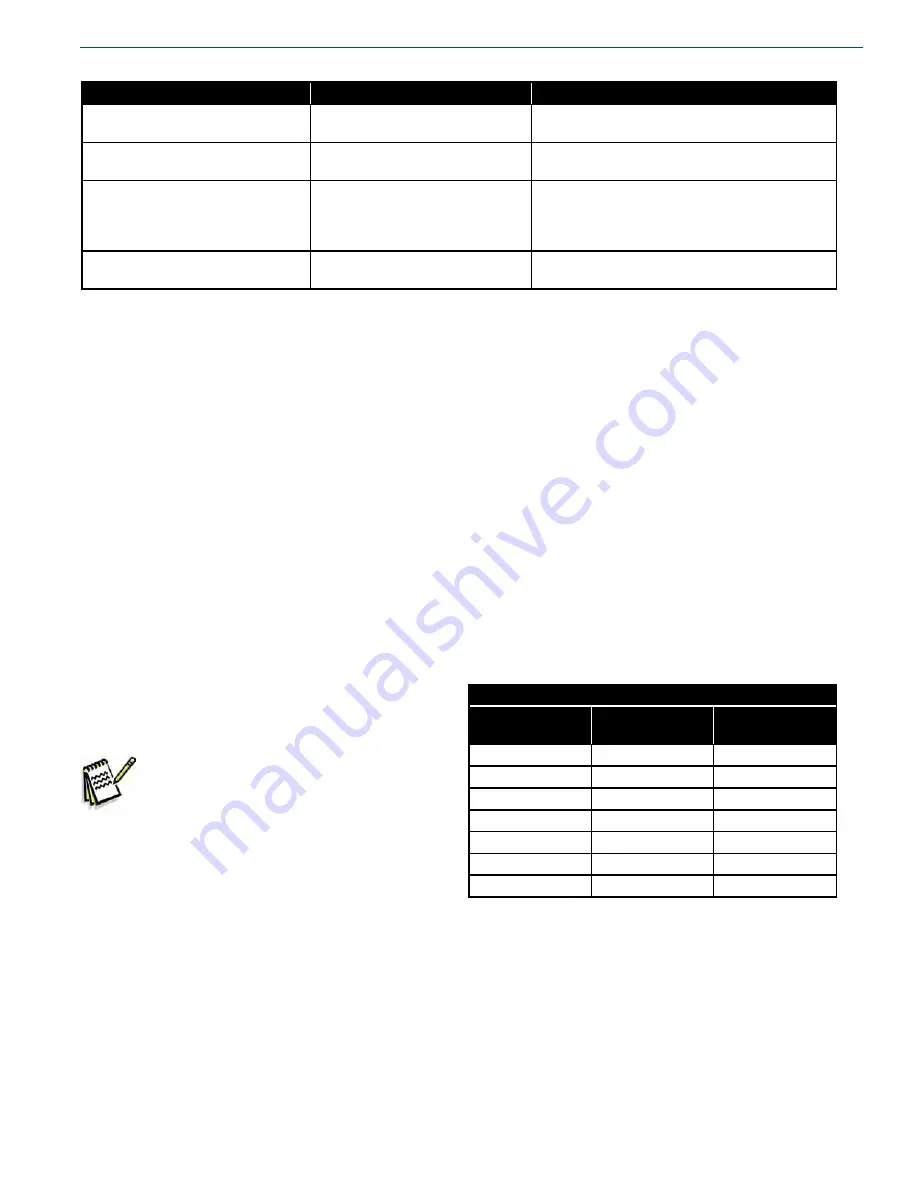
31
Maintenance
Product Manual - Liquid Cylinders
Trouble
Possible Cause
Remedy
Miscellaneous frost spots on
cylinders.
Cylinder may have internal
damage.
Call Chart for evaluation or repair/return
information.
Delivery gas is too cold.
Delivery rate exceeds
recommended delivery.
Refer to the Introduction section for
recommended maximum delivery rates.
In liquid delivery liquid is mixed with
high amount of gas.
Cylinder pressure is higher than
optimum for liquid withdrawal.
Refer to the Repairs section titled ‘Changing
Operating Pressure’ for instruction on resetting
the cylinder pressure for liquid use. Also, use a
phase separator on the end of the transfer hose.
In CO
2
service, cylinder does not
deliver product properly.
Possible dry ice blocks have
formed in the system.
Refer to the Repairs section titled ‘Reliquefying
Solid CO
2
’ for instructions.
Repairs
Reliquefying Solid CO
2
In the event the Dura-Cyl
®
HP/Cryo-Cyl
®
HP Liquid
Cylinder loses pressure and the contents become solidified,
the following procedure should be used:
1
Locate and correct the reason for the pressure loss; refer
to the Troubleshooting table in this section
2
Connect the proper gas source to the vent valve on the
frozen Dura-Cyl HP/Cryo-Cyl HP
3
Open the vent and gas source valve on the frozen liquid
cylinder and monitor its pressure.
4
Pressure in a frozen Dura-Cyl HP/Cryo-Cyl HP should
rise to 60 psig (4.1 barg) and remain there. When the
pressure starts to rise above 60 psig, it is an indication
that the solid has reliquefied. Continue to raise the
pressure to 200-300 psig (13.8-20.7 barg).
Note: Depending on length of time contents have
been frozen, the time to reliquefy could last
from six minutes to two weeks. This should
be done as soon as possible. It could take
up to two full liquid cylinders to reliquefy a
fully solidified tank.
Changing the Service Pressure
The inner pressure vessel used in the Dura-Cyl/Cryo-
Cyl liquid cylinders is designed and rated to a maximum
operating pressure by the DOT. All of the vessels have been
proof tested for that rating. The maximum pressure rating
is shown in the Specification section of this manual and on
the individual liquid cylinder’s data plate. DO NOT install
a relief valve with a higher pressure than specified. Lower
pressures are commonly used for limiting the maximum
pressure of the liquid.
The relief valve can be changed in the following manner:
1
Open the vent valve and release all pressure from the
vessel If the liquid cylinder is in CO
2
service the vessel
must be emptied of product.
2
Remove the relief valve. DO NOT attempt to repair or
reset the relief valve
3
Remove the metal identification tag.
4
Install the new identification tag and relief valve; use
oxygen compatible thread sealant or Teflon tape.
5
Pressurize the container and leak test with oxygen
compatible snoop solution.
The following relief valve parts list shows the various
pressure settings that are offered. The relief valves that are
marked for CO
2
and N
2
O are specially designed for those gas
products.
Relief Valves
Rego PN
Generant PN
Pressure Setting
(PSIG)
1810012
11884770
22
1810022
13382941
35
1810032
11531510
50
1810042
11868374
100
1810652
11868374
125
1811412
11884796
230
1810462
11884788
350
*Standard relief valves currently supplied are Generant. The above Rego
valves are also supplied upon request.
Changing Operating Pressure
The Dura-Cyl/Cryo-Cyl Liquid Cylinders have preset
operating pressure and preset pressure building and
economizer regulators These settings can be changed using
the procedures that follow.
Содержание Cryo-Cyl80HP
Страница 2: ......
Страница 6: ......
Страница 12: ......
Страница 32: ......
Страница 50: ...44 Specifications Product Manual Liquid Cylinders MCR Plumbing Configuration...
Страница 52: ...46 Specifications Product Manual Liquid Cylinders LCCM Plumbing Configuration...
Страница 54: ......
Страница 56: ......
Страница 57: ...51 Product Manual Liquid Cylinders Appendix 1 Troubleshooting Guides Cutaway Explanation...
Страница 62: ...56 Appendix 1 Product Manual Liquid Cylinders Troubleshooting Flow Chart 3...