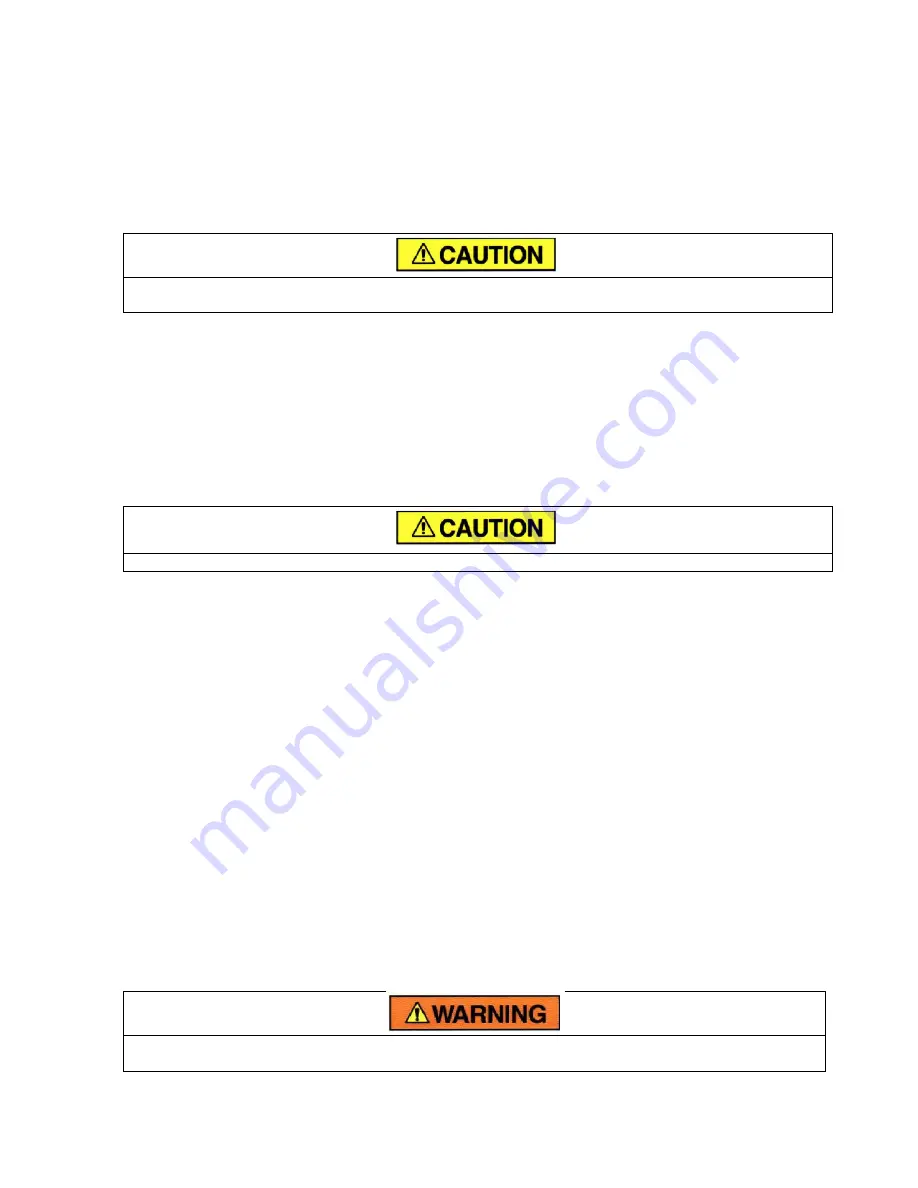
11
EVERY 90 DAYS OR 500 HOURS MAINTENANCE
1.
Change compressor crankcase oil and oil filter. Use only Champlub recip lubricant.
2.
Check entire system for air leakage around fittings, connections, and gaskets, using soap solution
and brush.
3.
Tighten nuts and cap screws as required.
4.
Check and clean compressor valves as required. Replace when worn or damaged parts.
Valves must be replaced in original position. Valve gaskets should be replaced each time valves
are serviced.
5.
Pull ring on all pressure relief valves to assure proper operation.
GENERAL MAINTENANCE NOTES
PRESSURE RELIEF VALVE:
The pressure relief valve is an automatic pop valve. Each valve is properly
adjusted for the maximum pressure of the unit on which it is installed. If it should pop, it will be
necessary to drain all the air out of the tank in order to reseat properly, or drop pressure in line. Do
not readjust.
BELTS:
Drive belts must be kept tight enough to prevent slipping. If belts slip or squeak, see V-belt
maintenance in preceding section.
If belts are too tight, overload will be put on motor and motor bearings.
COMPRESSOR VALVES:
If compressor fails to pump air or seems slow in filling up tank, disconnect unit
from power source and remove valves and clean thoroughly, using compressed air and a soft wire
brush. After cleaning exceptional care must be taken that all parts are replaced in exactly the same
position and all joints must be tight or the compressor will not function properly. When all valves are
replaced and connections tight, close hand valve at tank outlet for final test. Valve gaskets should
be replaced each time valves are removed from pump.
CENTRIFUGAL UNLOADER AND PRESSURE RELEASE VALVE:
The centrifugal unloader is
operated by two governor weights. It is totally enclosed and lubricated from the crankcase of the
compressor. When compressor starts the governor weights automatically open compressing the
main spring, allowing the unloader pressure release valve to close. When the compressor stops,
the main spring returns the governor weights to normal position opening the unloader pressure
release valve and unloading the compressor. This prevents overloading the engine when starting.
If air continues to escape through the governor or unloader pressure release valve while operating,
this is an indication that the unloader pressure release valve is not closing tightly and may be held
open by foreign substance which has lodged on the seat. In order to correct this, remove the
governor release valve cap, giving access to release valve spring and ball. Clean thoroughly and
return parts in the same order in which they were removed. Loose drive belts can also cause
unloader to leak by preventing the compressor from reaching proper speed. (See
“BELTS” above).
CHECK VALVE:
The check valve closes when the compressor stops operating, preventing air from
flowing out of the tank through the pressure release. After the compressor stops operating, if air
continues to escape through the release valve, it is an indication that the check valve is leaking.
This can be corrected by removing check valve and cleaning disc and seat. If check valve is worn
badly, replace same.
Before removing check valve be sure all air is drained out of tank and power is disconnected.
Failure to do so may result in injury or equipment damage.
Содержание BDR5K
Страница 2: ......
Страница 32: ...30 UNIT HAZARD DECALS ...