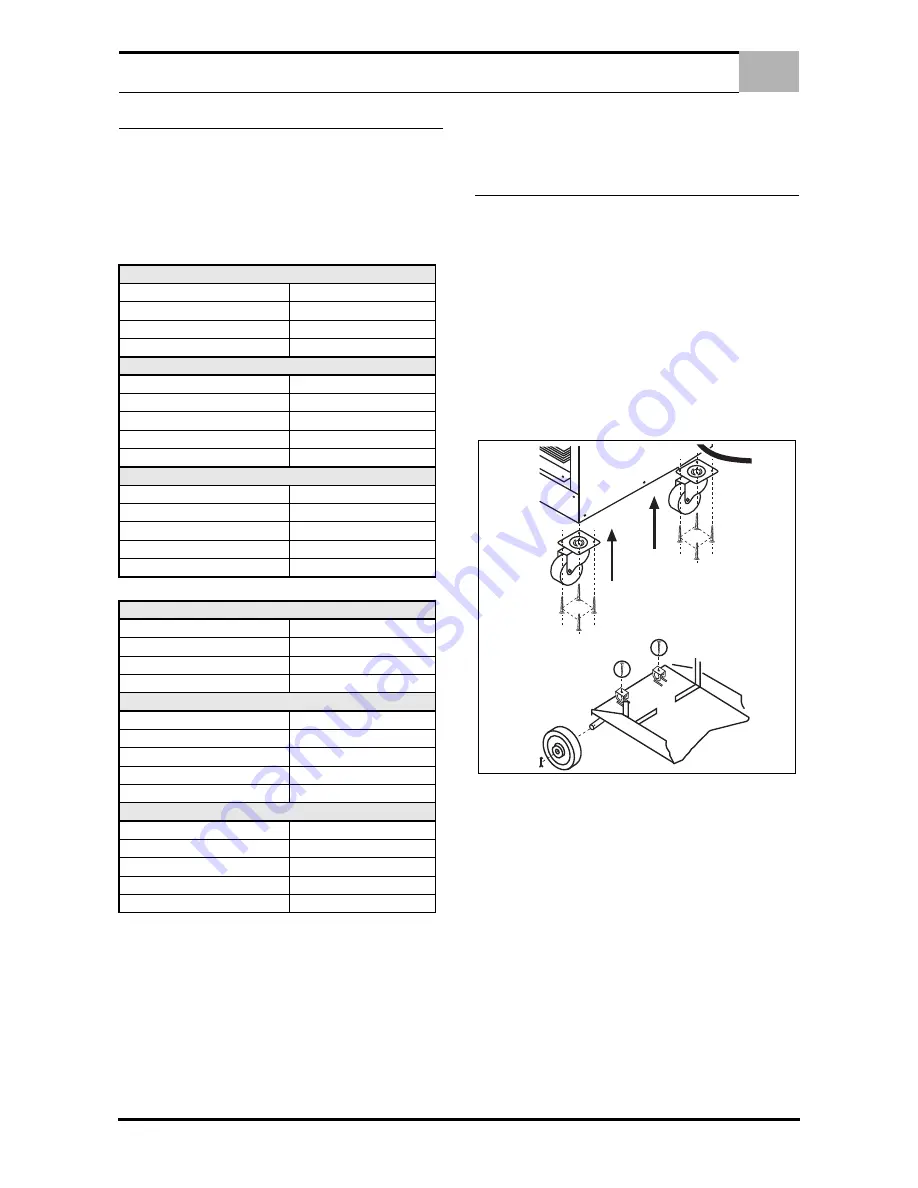
2 EN
TECHNICAL DESCRIPTION
EN
1.0
TECHNICAL DESCRIPTION
1.1
DESCRIPTION
MIG welders which can weld flux cored gasless wire or with gas
for the welding of mild steel, stainless steel and aluminium. MIG/
MAG welder swhich can weld mild steel, stainless steel and alu-
minium.
1.2
DATA PLATE
140 A / 140 A EURO CONNECTOR
180 A
1.3
DUTY CYCLE AND OVERHEATING
The duty cycle is the percentage of a 10 minute period for which
the welder can continue to weld without overheating. If the ma-
chine overheats, the welding current is shut off and the relative in-
dicator lamp illuminates. In this case, leave the machine to cool for
approx. 15 minutes and, before restarting, lower the welding cur-
rent value and relative voltage or reduce the work time.
Example: 250 A - 30% means working for 3 minutes at 250 A with
7 minutes rest time.
1.4
VOLT - AMPERE CURVES
Volt-ampere curves show the welder's maximum voltage and am-
perage output capabilities of the welding power source. Curves of
other settings fall under curves shown. See page XIII.
2.0
INSTALLATION
IMPORTANT: BEFORE CONNECTING, PREPARING OR USING
EQUIPMENT, READ SECTION 1.0 SAFETY PRECAUTIONS.
2.1
MACHINE ACCESSORIES
1.
Unpack the equipment and components to complete the ma-
chine assembly.
2.
Leave the machine on the wooden pallet, and use a 13 hex
wrench to remove the eight screws (four on the left and four
on the right) under the front panel; fit the two castor wheels
and refit the screws.
3.
Remove the two screws securing the machine to the pallet,
located on the cylinder support.
4.
Raise the rear section of the machine slightly to rotate the
pallet and thus release the rear section.
5.
Remove the screws from the axle and proceed with assem-
bly of the fixed wheels.
6.
Fit the handles.
2.2
CONNECTING THE POWER SOURCE TO THE MAINS
ELECTRICITY SUPPLY.
SERIOUS DAMAGE TO THE EQUIPMENT MAY RESULT IF
THE POWER SOURCE IS SWITCHED OFF DURING WELDING
OPERATIONS.
1.
Ensure that the power supply socket is equipped with the
fuse specified in the table.
2.
Before inserting the power plug, to avoid damage to the gen-
erator, check that the mains voltage corresponds to the re-
quired power supply.
2.3
HANDLING AND TRANSPORTING THE POWER
SOURCE
OPERATOR SAFETY: WELDER’S HELMET - GLOWES -
SHOES WITH HIGH INSTEPS.
The machine is easy to lift, transport and handle, though the fol-
lowing procedures must always be observed:
1.
Do not lift by means of the handle
2.
Always disconnect the power source and accessories from
main supply before lifting or handling operations.
3.
Do not drag, pull or lift equipment by the cables.
PRIMARY
Three phase supply
230 V
Frequency
50 - 60 Hz
Effective consuption
7,5 A
Maximum consuption
24 A
SECONDARY
Open circuit voltage
18 ÷ 32V
Welding current
30 A ÷ 170 A
Duty cycle 18%
140 A - 21 V
Duty cycle 60%
75 A - 18 V
Duty cycle100%
60 A - 17 V
Protection class
IP 21
Insulation class
H
Weight
Kg. 38,5
Dimensions
mm 440 x 670 x 750
European Standards
EN 60974.1 / EN 60974.10
PRIMARY
Three phase supply
230 V
Frequency
50 - 60 Hz
Effective consuption
12,4 A
Maximum consuption
32 A
SECONDARY
Open circuit voltage
17,5 ÷ 33V
Welding current
35 A ÷ 180 A
Duty cycle 15%
180 A - 23 V
Duty cycle 60%
100 A - 19 V
Duty cycle100%
75 A - 18 V
Protection class
IP 21
Insulation class
H
Weight
Kg. 43
Dimensions
mm 440 x 670 x 750
European Standards
EN 60974.1 / EN 60974.10