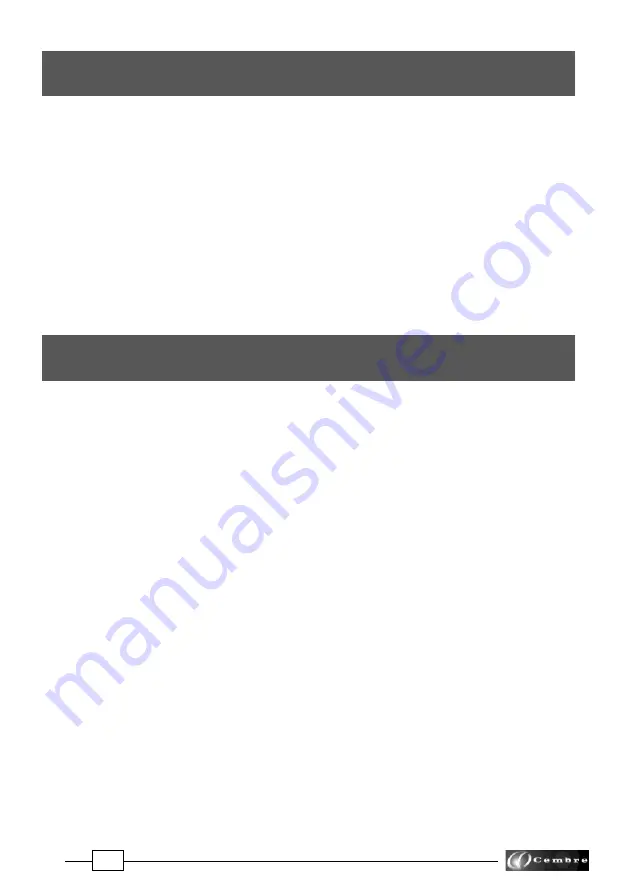
35
14.1)
Regularly check for correct tightening (torque) of the fixing screws of the drilling tools and
positioning templates.
14.2)
Avoid pressure jolts on the advancing lever during drilling.
14.3)
Always make sure that the drilling swarf is properly removed before starting to drill a new
hole.
14.4)
Incomplete clamping of the drill on the rail to be drilled may lead to the breakage or ac-
celerated wear of the drilling tool and damage to the spindle shaft bearings.
14.5)
If it is necessary to operate the drill without the cutter inserted, remove the locking grub
screws from the spindle shaft.
14.6)
Avoid leaving the
SR5000
tank under pressure and exposed to sunlight for long periods of
time.
14.7)
Should the
DBG-F2
clamping device be removed, make sure that by reassembling it, the
two locking screws are firmly fastened.
14. WARNINGS
15. RETURN TO
Cembre
FOR OVERHAUL
In the case of a breakdown contact our Area Agent who will advise you on the problem and give
you the necessary instructions on how to dispatch the tool to our nearest service Centre; if pos-
sible, attach a copy of the Test Certificate supplied by
Cembre
together with the tool or fill in
and attach the form available in the “ASSISTANCE” section of the
Cembre
website.
APPENDIX “A”
Factors which influence the number of holes that can be made according to the tool used:
– Hardness of the material to be drilled.
– Thickness to be drilled.
– Stability of the drill clamping
and correct assembly of the drilling tool.
– Suitable lubrocooling (lubrication/cooling)
to keep the temperature of the tool low so as not
to compromise the efficiency of the cutting edges, whilst at the same time facilitating the
removal of the swarf.
– Contact time of the cutting edges of the tool with the material to be drilled;
bear in mind
that the faster the hole is made, the greater the efficiency.
– Observance of these basic rules:
1)
Commence drilling by exerting light pressure on the advancing lever, progressively
increasing and then relaxing it when the tool is in the exit phase.
2) Avoid pressure surges and advance according to the diameter of the drilling diameter, to
avoid scratching the material or damaging the cutting edges of the tool.
3) Remember that a tool with efficient cutting edges requires a lower application pressure
than one that has already made a certain number of holes.
4)
When holes are made close to raised lettering on the rails, commence drilling with very
light pressure
until the lettering disappears, to avoid possible breakage of the tool.
5) Bear in mind that when operating on very hard rails, as in the case of quality 1100 steel, it
is advisable to increase the lubrocoolant flow rate.