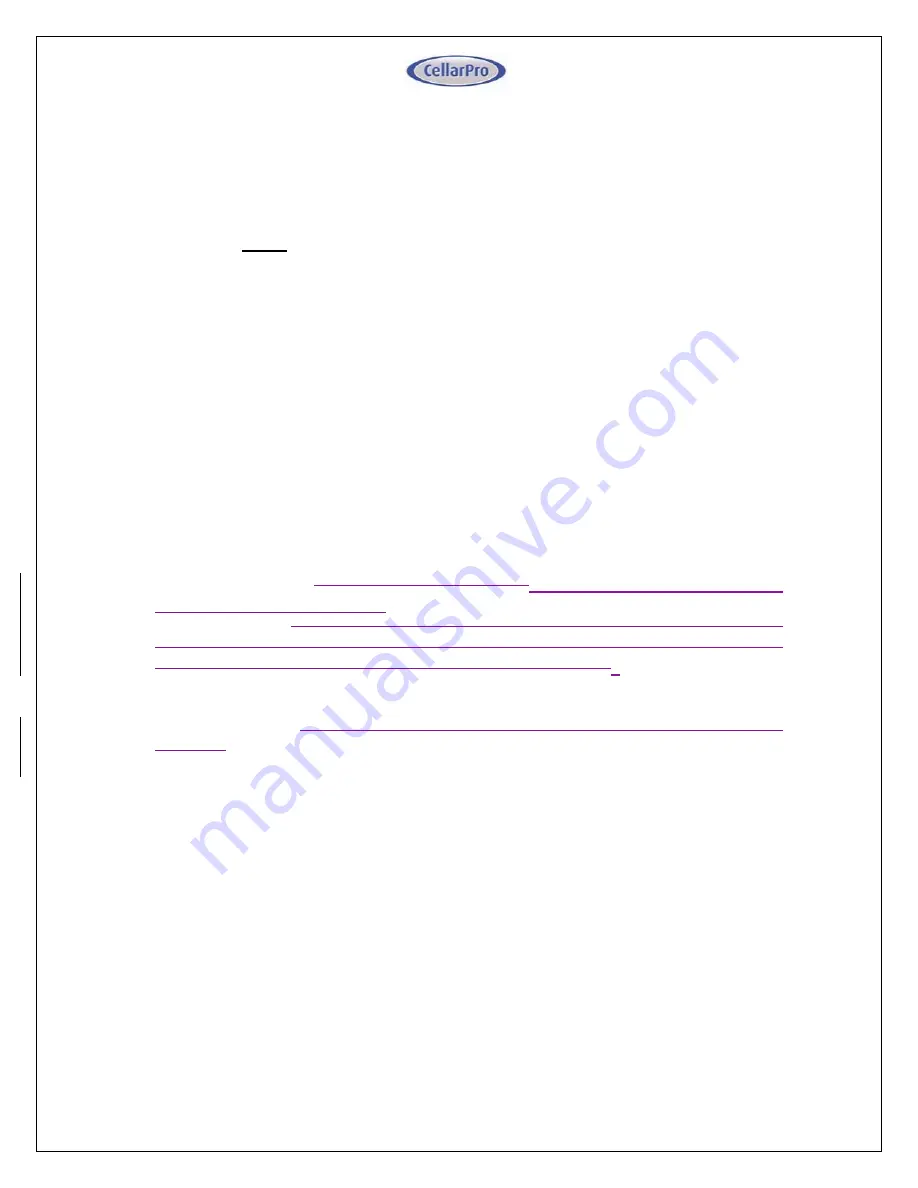
26
V10.19
the end of this manual. Do not run the system if the suction superheat at the
condensing unit is below 20°F.
12. It may be necessary to slightly adjust the charge amount after weighing in the
recommended initial charge. 1) Not enough refrigerant: If the Evaporator is not
providing enough cooling, the system may be undercharged. If liquid subcooling
is below 10°F and the suction superheat is well above the minimum of 20°F,
slowly add vapor refrigerant though the suction service valve until the subcooling
is within specifications. 2) Too much refrigerant: If the suction superheat is
below 20°F, remove refrigerant until the superheat is above this minimum limit.
13. (Optional) It should not be necessary to manually adjust the thermostatic
expansion valve superheat from the factory default setting. However if desired,
the superheat may be adjusted as follows: 1) Remove the cork tape insulation
from the expansion valve body to locate the cap on the superheat stem, and
unscrew the cap using a 5/32 in. Allen wrench. 2) Using a 5/32 in. Allen wrench,
locate the setting spindle inside the superheat stem and make superheat
adjustments ¼ turn at a time (¼ turn≈1°F). Turning clockwise increases
superheat. Turning counter-clockwise decreases superheat. The target
superheat at the evaporator is 10°F +/- 2°F. 3) Reinstall the cap and cork tape
insulation.
14. If your unit is setup for
Valve Control Systems
, the condensing unit dual
pressure control is configured with the high pressure tap factory installed. The
low pressure tap is
capped and not connectedinstalled on an access valve on
the compressor process port
. If the system has a liquid solenoid valve (Valve
Control option),
the low pressure tap of the dual pressure control must be
attached to either the service port on the suction Rotolock valve, or a field
provided access valve port on the field suction piping
.
Vv
erify that the system
pumps down and the low pressure switch turns off the compressor. The low
pressure set point is adjustable, but should not need to be changed from the
factory settings.
Note: This connection is not required for electronic control
systems.
15. Confirm that the compressor and evaporator fan(s) are energized. Allow the
system to balance for 30 minutes, then record all readings on the Data Sheet
and submit to CellarPro for warranty activation review.
16. Observe that the compressor turns on when the “snowflake” icon on the
temperature display is lit solid (not blinking), and turns off when the “snowflake”
icon turns off. It may be necessary to temporarily raise the set point to force the
unit to cycle off. If the condensing unit does not cycle on/off in conjunction with
the “snowflake” icon, please contact the factory for assistance.
17. Once the system is confirmed to be running properly, enter the following
programming change so that the startup delay increases from 3 to 30 minutes:
a. On the control panel, press and hold the "SET" and "DOWN ARROW"
buttons AT THE SAME TIME for 3 seconds (the display will briefly flash).
Содержание 4000Shwc
Страница 1: ...V10 19 ControltheElements SplitWaterCooled RefrigerationSystems Owner sManual...
Страница 6: ...6 V10 19 Evaporator Cut Sheets...
Страница 7: ...7 V10 19 Condensing Unit Cut Sheets...
Страница 16: ...16 V10 19 Wiring Diagrams Option A Dual Power Valve Control Models 4000Swc 4000Shwc...
Страница 17: ...17 V10 19 Wiring Diagrams Option A Dual Power Valve Control Model 8000Swc...
Страница 19: ...19 V10 19 Wiring Diagram Option B Single Power Electronic Control Models 4000Swc 4000Shwc...
Страница 20: ...20 V10 19 Wiring Diagram Option B Single Power Electronic Control Models 8000Swc...