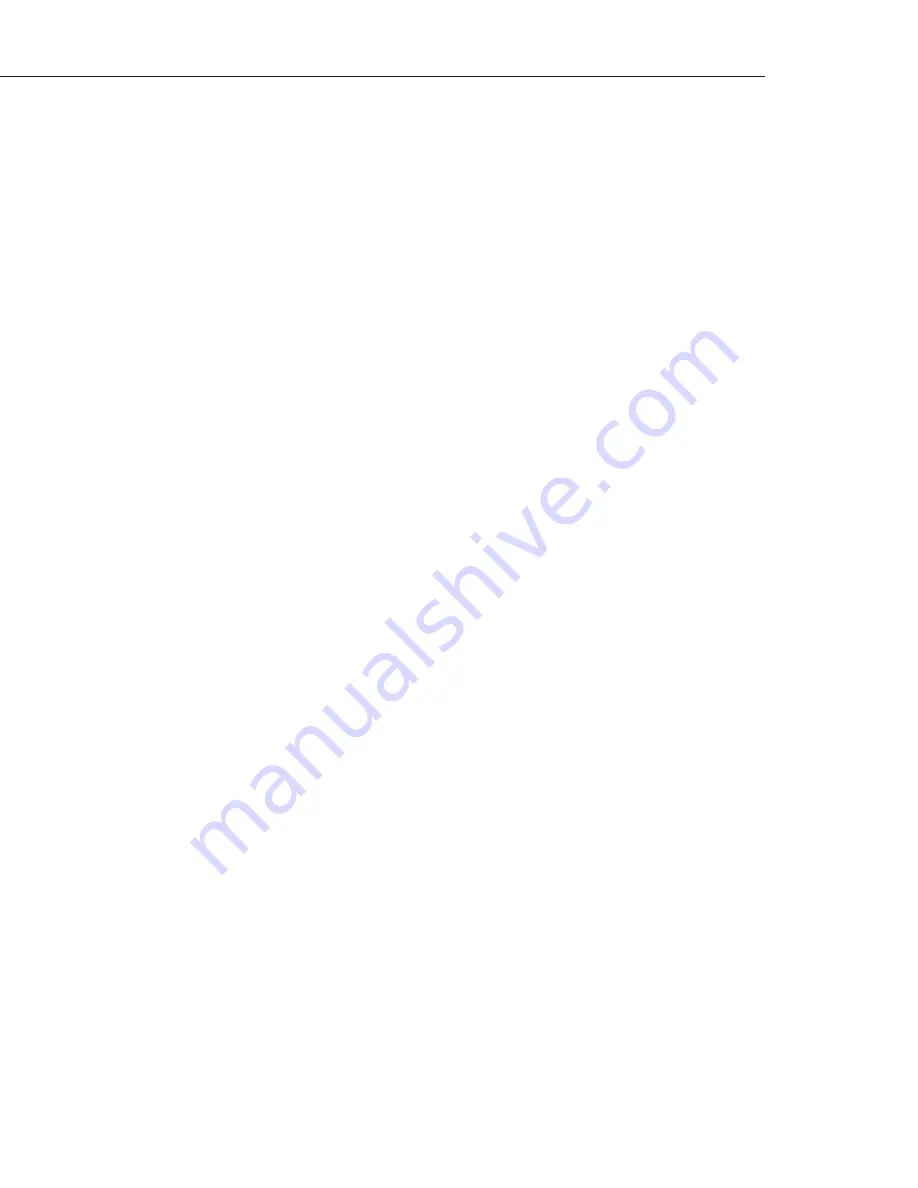
www.cellarcool.com | Page 37
CM2500
Insulate the 3/8” suction line with cork tape.
Evacuation
Connect four-valve manifold to high- and low-pressure service valve ports on the condensing unit. The valve stems should be
mid-seated (as when leak testing). Install service caps on the valves and tighten them. Energize the liquid line solenoid valve
(make sure there is fresh oil in the vacuum pump). Connect a micron gauge directly to the pump, blank off, and start the pump
to verify that it is capable of 200-micron vacuum and the gauge is capable of reading that vacuum. Connect the micron gauge
to the access valve installed in the suction line at the evaporator unit. Remove the Schrader valve depressors from the gauge
hoses to reduce restriction and connect gauges to the suction and liquid line service valve service ports on the condensing unit.
Connect the pump to the 3/8” hose on the manifold set. Start the pump and run it until the micron gauge reads 200 microns.
When a 200-micron-level evacuation is achieved, break the vacuum with R-134a and add enough refrigerant to pressurize the
system with a few psi of positive pressure.
Charging
Remove the vacuum pump and the micron gauge. Install a spare low-pressure gauge on the access valve at the evaporator unit.
With the power off to the condensing unit, place the cylinder of R-134a on a digital scale. Admit liquid refrigerant to the system
through the high-pressure side (liquid line service valve) until about 11/2 lbs have been added. Shut off refrigerant flow to system.
Fill a wine bottle 75% full with water between 60 and 75°F. Insert the bottle probe into the neck of the bottle as far as possible.
(It is important the bottle probe stopper is compressed by the neck of the bottle to ensure water will not leak out). Verify that
the bottle probe is properly installed and the set point on the controller is low enough to allow the system to run continuously
for 30 minutes or more. Turn on power to the condensing unit. The compressor should start if suction pressure is above 6 psi. If
the system pumps down and the compressor shuts off, set the five-minute time-delay relay time to the lowest setting to avoid
having to wait. Add refrigerant as a vapor through the low-pressure side of the system (suction service valve port).
Observe the sight glass when the compressor starts. If bubbles are present, slowly add more refrigerant (in vapor form) to the low
side. The suction pressure and head pressure should increase as the sight glass clears. Check the superheat during the charging
process. If the superheat drops to 4-5°F and sight glass still has bubbles, let the unit run until the wine cellar temperature drops
and approaches 55°F. Observe the sight glass. If bubbles are present, add additional refrigerant in small increments. Let the
system stabilize for about 5 minutes and check the sight glass for bubbles before adding additional refrigerant. Once the sight
glass is clear, check the superheat at the outlet of the evaporator unit (evaporator superheat should be between 8 and 12°F). If
superheat is not between 8 and 12°F, make an adjustment to the expansion valve. Depending on the temperature, the high side
should be approximately 175 lbs, and the low side should be 28 lbs or more to keep the evaporator unit from icing.
Measure Superheat
If superheat is high and bubbles are present, add more refrigerant until it is clear. If superheat is low (around 4 to 6°F) and
bubbles are present in the sight glass, check for liquid refrigerant entering the compressor (as evidenced by a cool crankcase
temperature of less than 100-110°F and low discharge superheat). Adjust TXV setting in small increments to increase superheat
and stop liquid from going to the compressor. Check this before adding more refrigerant. If the temperature of the air entering
the condenser is cold enough to cause the condenser fan to cycle, block about 60% of the coil to raise the head pressure and
allow time for stabilization. Reduce blockage if the condensing temperature is above 115°F. Retain blockage if necessary to
maintain stability for the performance test listed in the split system warranty checklist. If the air entering the condenser is cold
(below 60°F) and the sight glass is clear, allow the system to run for a while until the cellar cools off, then measure and record
data on the split system warranty checklist.
Confirm the controller is displaying the correct temperature and that the controller is not displaying an alarm. If the controller
is displaying an alarm, refer to page 42 for corrective action. Confirm that the suction line is completely insulated from TXV to
compressor. Confirm that the sight glass has no bubbles and the ambient temperature around the condensing unit is not getting
excessively hotter. Confirm that both king valves have been back-seated and the nuts have been installed back on the king
service ports.
INSTALLING THE CONDENSING UNIT (continued)