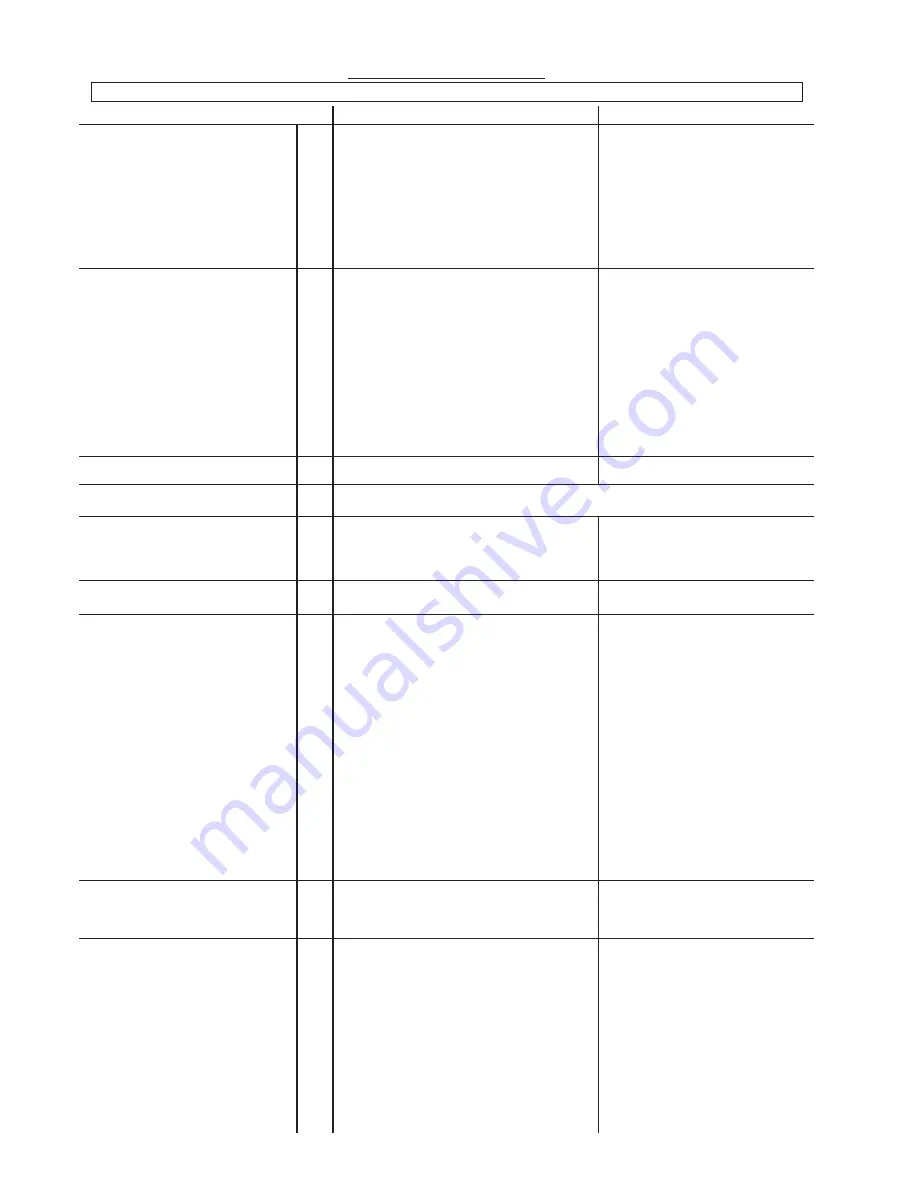
TROUBLESHOOTING
FAULT
POSSIBLE CAUSES
REMEDIES
NO WEDGES ARE INSERTED
INTO THE MOULDING
THE WEDGE IS NOT FULLY
INSERTED INTO THE
MOULDING
THE WEDGE BREAKS
MOULDINGS DIFFICULT
TO MOVE
STAINS ON BACK
POOR JOINING
- Corner open on inside
- Corner open on outside
- Opening on top and bottom
of joint
- Mouldings marked by
triangle rubber top pressor
THE WEDGE DRIVER BLADE
DOES NOT LOWER
- The wedge cartridge is empty
- The wedge distributor is clogged
- The wedge spring is broken or relaxed
- The wedge driver blade is broken
- Top clamp / Moulding distance not
within permissible maximum
- Moulding not adequately secured on the
table
- Wedge driver blade damaged
- Hard wood
ANGLE OFFSET
- The first moulding was not pushed firmly against the left stop (page 5)
- The rebate clamp is too tight against the
mouldings.
- Too much grease on the wedge driver
blade
- Bad cut
- Incorrect setting
- Incorrect setting of stops
- Triangle rubber top pressor for hard
wood used on soft wood
- Misalignment
- Fit a new wedge cartridge
- Clean it
- Check the condition of the spring
and replace if necessary
- Change the wedge driver blade
(page 10)
- Reposition the plunger within
permissible maximum distance
(page 6)
- Secure the moulding firmly on
the table
- Change the wedge driver blade
- Use hard wood wedges (page 7)
- When the rebate clamp is tight-
ened do not push it towards the
mouldings
- Clean the wedge driver blade
- Repeat the cut
- Loosen the AS screw (page 2-4)
to compensate for opening
- Check the self-adjusting
backfences before starting under-
pinning
- Use a suitable triangle rubber top
pressor (page 6)
- Contact after-sales service
IF THE PROPOSED REMEDIES DO NOT SOLVE THE PROBLEM CONTACT THE AFTER-SALES SERVICE
THE PLUNGER DOES NOT
LIFT
- Limit screw incorrectly set
- Check the setting of the limit
screw
- Air supply pressure less than 6 bar
- Increase the pressure
- Wedge jammed in the wedge distributor
- Dismantle the wedge driver blade
to remove the wedge (page 10)
- Limit screw incorrectly set
- Reset the limit screw (page 11)
- Distance between bottom of top clamp
and top of moulding outside permissible
maximum
- Reposition the plunger and expel
any wedge that may have gone
into the wedge distributor using
the tool supplied (page 9)
12
88-89
89
88-89
88-89
88-89
88-89
88-89
88-89
88-89
88-89
88-89
89
88-89
88-89
88-89
88-89
88-89
88-89
88-89
88-89
89
Содержание CS 88
Страница 17: ......