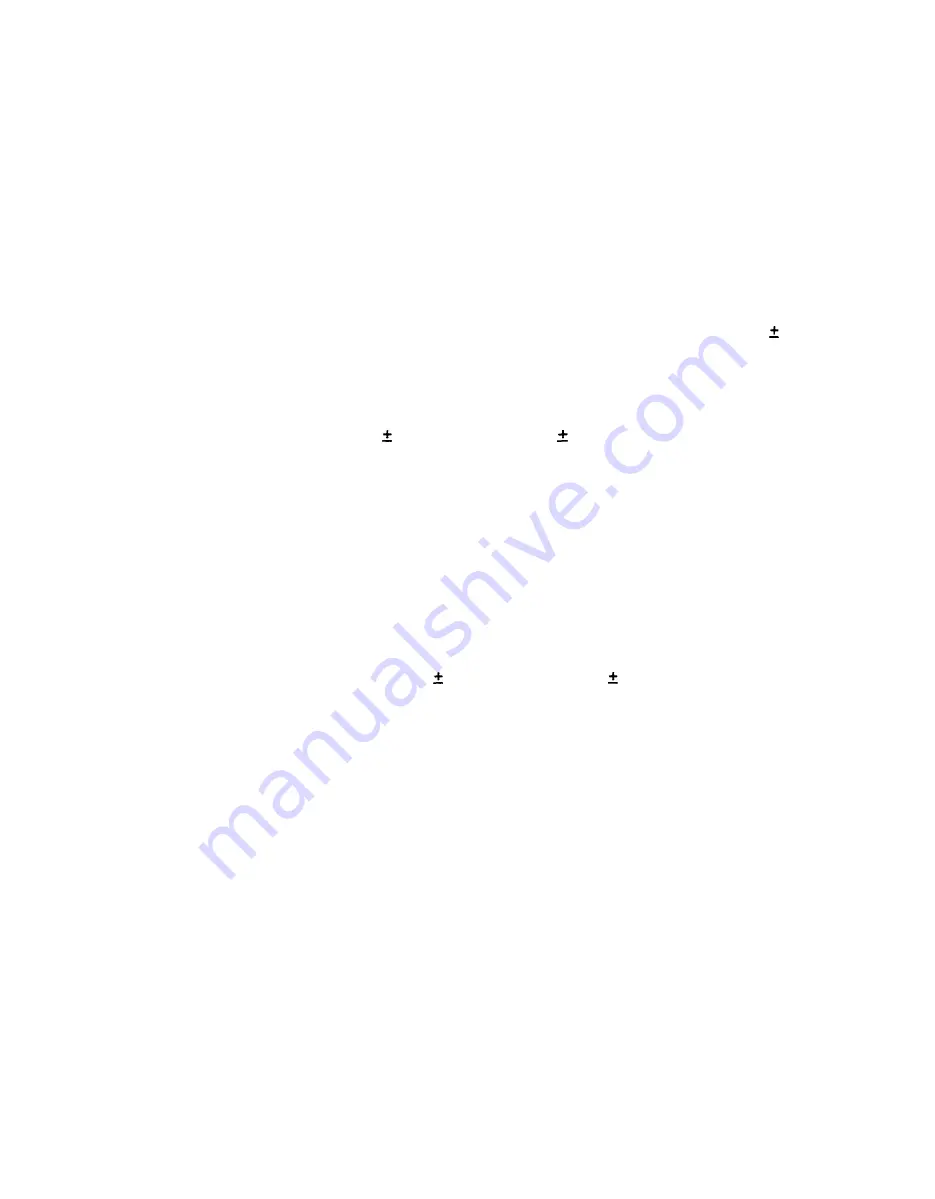
Service Bulletin NTR SB 026 96
Magnum Hitch Diagnostic Codes and Service Manual update
Page 12 of 26
HITCH CALIBRATION PROCEDURE CONTINUED
9. Press the hitch switch to the MOMENTARY position and release. “11” should appear on the diagnostic
1 0 .
11.
12.
13.
display. Note: The control module is asking you if the tractor has an upper limit knob.
Press the hitch switch to the MOMENTARY position and release to answer “yes”. A “8” should appear on
the diagnostic display. Note: The “8” means the system is ready to calibrate.
Hold the hitch switch in the MOMENTARY position until the hitch has completely lowered, then release.
Do
not release switch before hitch is fully lowered. A “6” should appear on the diagnostic display.
With the hitch in the FULLY LOWERED position and the test box at position 2, set D.C. voltage to .9
.1
volts, at the hitch rockshaft pot above the right rear axle housing. See Service Manual section 8009-9 steps
24 & 25.
Test Rockshaft pot:
Set the DVM to the 2 decimal place range, do not perform test with the DVM in the
auto ranging mode. View the DVM voltage while the hitch is being raised in step 16. As the hitch raises the
voltage should smoothly increase from .9 .1 to approximately 4.70 .2 volts D.C. in the fully raised
position.
14. Move the hitch lever to the full raise position. Raise the hitch by pressing the hitch switch to the
MOMENTARY position and releasing the switch (The hitch position lever should still be in the transport
position). A “9” should appear on the diagnostic display. The hitch should raise after a delay. If any reason
occurs where the hitch movement should be stopped during this process, toggle the switch to the UP
position.
15. Move the hitch position lever to the fully lowered position. Make sure the stop is not in the way. The lever
must be all the way down.
16. Test Rockshaft pot:
Set the DVM to the 2 decimal place range, do not perform test with the DVM in the
auto ranging mode. View the DVM voltage while the hitch is being lowered in step 19. As the hitch lowers
the voltage should smoothly decrease from 4.70 .2 to approximately to .9 .1 volts D.C. in the fully
lowered position.
17.
18.
19.
Lower the hitch by pressing the hitch switch to the MOMENTARY position and release. After a delay, the
hitch will lower to full down. A
“U”
should appear on the diagnostic display.
If
any reason occurs for the
hitch movement to be stopped during the process, toggle the hitch switch to the UP position.
When the hitch has fully lowered, press the hitch switch to the MOMENTARY position and release. “0”
should appear on the diagnostic display, meaning calibration has been successful.
Check for and clear any error codes from memory.
SEE PAGE 20 FOR INFORMATION ON TESTING THE ROCKSHAFT AND
POSITION LEVER POTENTIOMETERS
Содержание Magnum 7210
Страница 24: ......