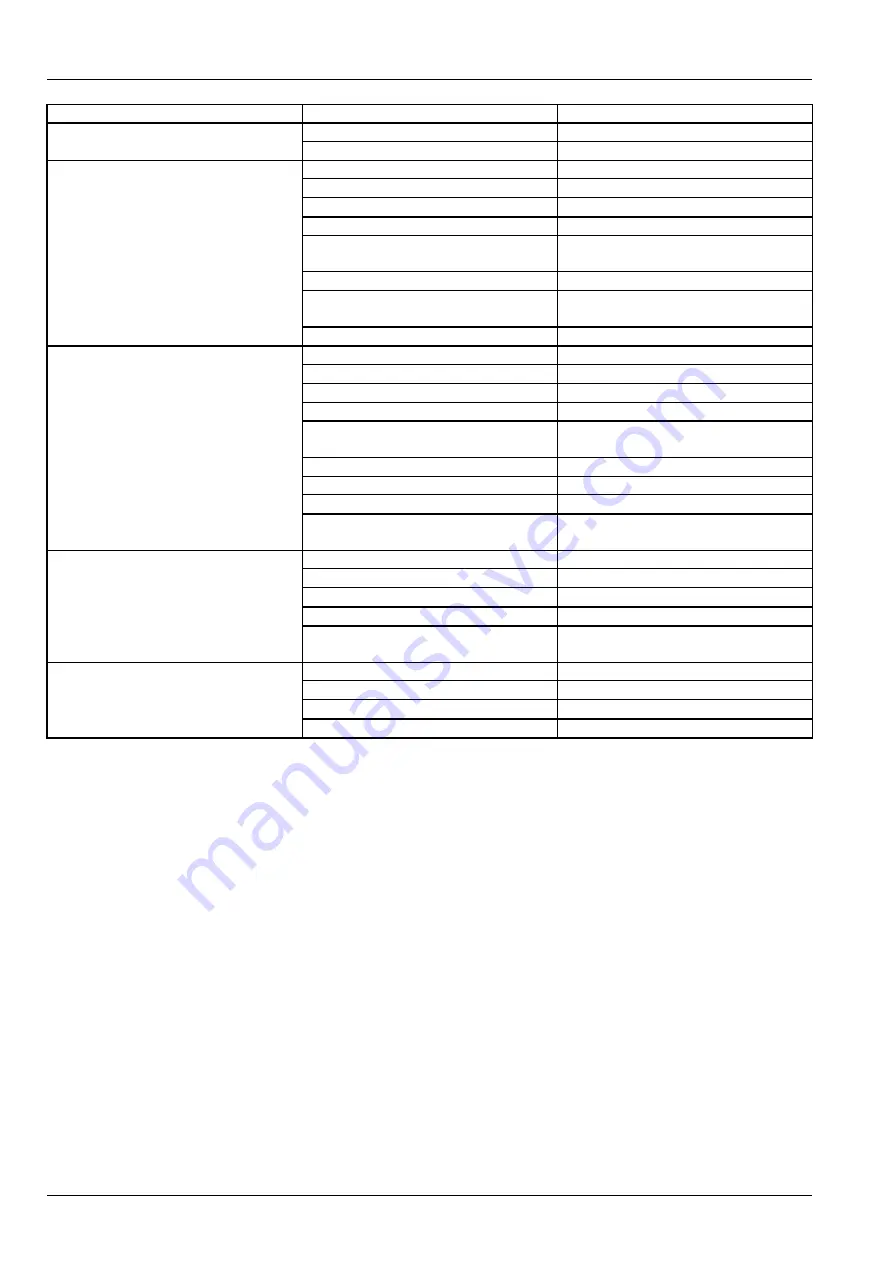
8 - TROUBLESHOOTING
PROBLEM
POSSIBLE CAUSE
CORRECTION
Incorrect installation.
Correct the installation.
No differential action; jamming while
steering.
Bent or broken axle shaft.
Replace the axle beam.
Incorrect installation.
Correct the installation.
Defective axle.
Inspect and repair.
Wrong weight distribution.
Distribute the weight differently.
Overload.
Remove the excessive load.
Incorrect tyre rotation radius.
Replace the tyre or adjust pressure
on both tyres.
Bent or broken axle shaft.
Replace the axle beam.
Incorrect wheel alignment.
Check that the structure and the
bearings are in good conditions.
Excessive noise.
Incorrect axle part installation.
Check the installation.
Incorrect installation.
Correct the installation.
Defective axle.
Inspect and repair.
Wrong weight distribution.
Distribute the weight differently.
Overload.
Remove the excessive load.
Incorrect tyre rotation radius.
Replace the tyre or adjust pressure
on both tyres.
Bent or broken axle shaft.
Replace the axle beam.
Blocked differential.
Check the installation.
Excessive steering angle.
Reduce the steering angle.
Excessive wear of the tyre.
Incorrect wheel alignment.
Check that the structure and the
bearings are in good conditions.
Incorrect installation.
Correct the installation.
Bent or broken axle shaft.
Replace the axle beam.
Damaged or worn axle parts.
Replace the damaged axle parts.
Incorrect axle part installation.
Check the installation.
Friction noise.
Incorrect adjustment of the bevel
gear set.
Adjust the bevel gear set.
Incorrect installation.
Correct the installation.
Defective axle.
Inspect and repair.
Wrong weight distribution.
Distribute the weight differently.
Vibrations during travel.
Bent or broken axle shaft.
Replace the axle beam.
8-14
Содержание 580ST
Страница 8: ......
Страница 20: ...1 GENERAL INFORMATION LEEN11T0031AA_2 2 1 Front side 3 Right hand side 2 Rear side 4 Left hand side 1 12 ...
Страница 24: ...1 GENERAL INFORMATION 1 16 ...
Страница 49: ...2 SAFETY INFORMATION Extend telescopic dipper If fitted MOLI12LBB0092AA 24 2 25 ...
Страница 101: ...3 CONTROLS AND INSTRUMENTS Setup menu LEIL12TLB00006I 1 3 39 ...
Страница 144: ...3 CONTROLS AND INSTRUMENTS 3 82 ...
Страница 164: ...4 OPERATING INSTRUCTIONS 4 20 ...
Страница 166: ...5 TRANSPORT OPERATIONS RAIL14TLB1181GA 1 5 2 ...
Страница 178: ...5 TRANSPORT OPERATIONS 4WS 12 For towing purposes Road type steering 1 must be selected LEEN11T0206AA 5 5 14 ...
Страница 222: ...6 WORKING OPERATIONS 6 44 ...
Страница 247: ...7 MAINTENANCE Fuel tank capacity 145 L 38 30 US gal 2WS 124 L 32 76 US gal 4WS 7 25 ...
Страница 341: ...7 MAINTENANCE Fuses and relays Power Shuttle canopy 580T mechanical engine MOLI12LBB0488CA 4 7 119 ...
Страница 343: ...7 MAINTENANCE Fuses and relays Power Shuttle cab 580T mechanical motor MOLI12LBB0489CA 5 7 121 ...
Страница 345: ...7 MAINTENANCE Fuses and relays Power Shuttle cab 580ST 590ST electronic motor MOLI12LBB0490CA 6 7 123 ...
Страница 347: ...7 MAINTENANCE Fuses and relays Powershift cab 2WS MOLI12LBB0491CA 7 7 125 ...
Страница 349: ...7 MAINTENANCE Fuses and relays Powershift cab 4WS MOLI12LBB0492CA 8 7 127 ...
Страница 390: ...8 TROUBLESHOOTING 8 28 ...
Страница 418: ...9 SPECIFICATIONS 4WS LEEN11T0039FA 2 9 28 ...
Страница 420: ...9 SPECIFICATIONS 2WS 590ST LEEN11T0041FA 5 4WS 695ST LEEN11T0042FA 6 9 30 ...
Страница 433: ......