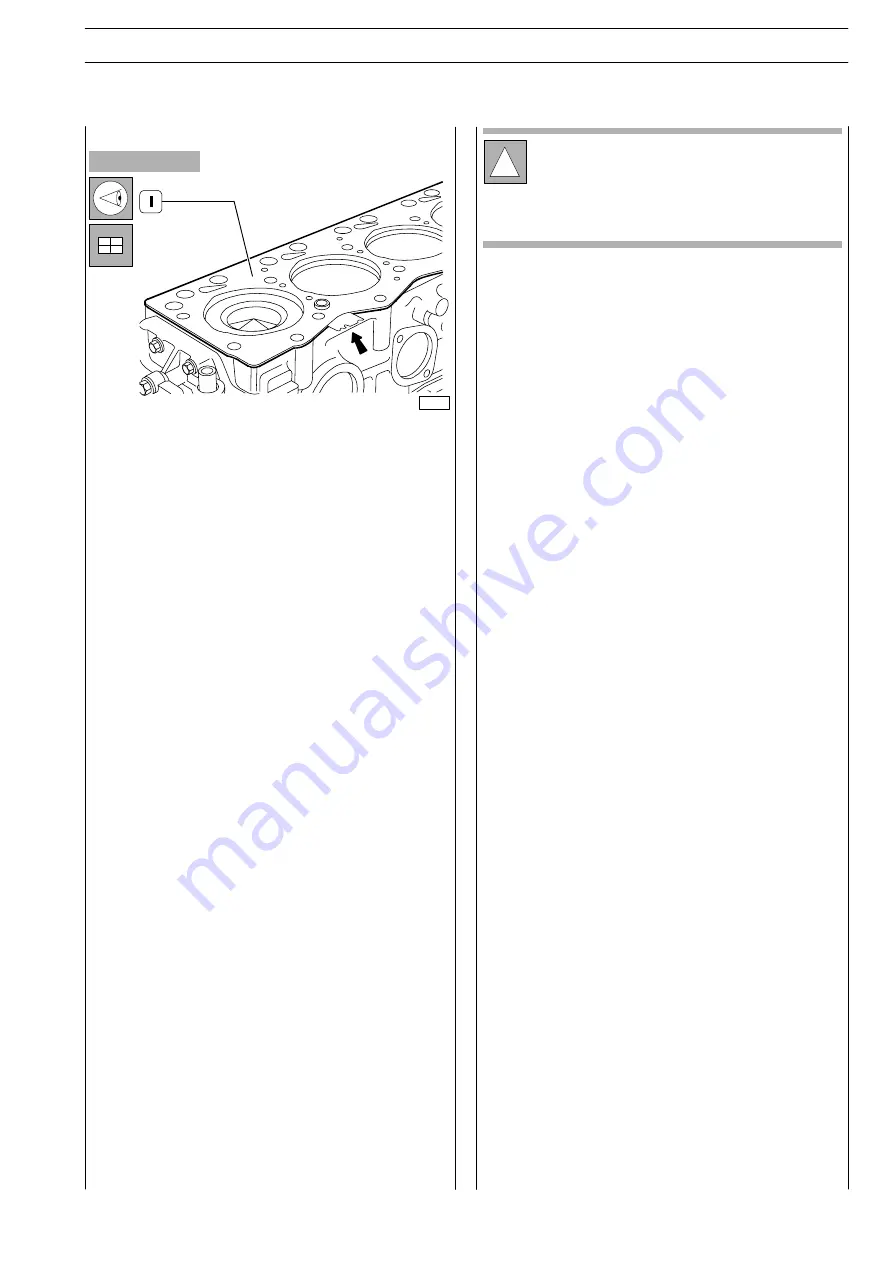
Check cleanness of cylinder head and engine block coupling
surface.
Take care not to foul the cylinder head gasket.
Set the cylinder head gasket (1) with the marking “N. of
component” (1) facing the head.
The arrow shows the point where the gasket thickness is given.
70335
Figure 85
Refitting the cylinder head
!
Before re
−
utilising the fixing screws for the cylinder
head, verify there is no evidence of wear or
deformation and in that case replace them.
SECTION 4
−
OVERHAUL AND TECHNICAL SPECIFICATIONS
ENGINES
35
ED. FEBUARY 2003
Содержание 445/M2
Страница 1: ...CASE ENGINES 445 M2 445T M2 668T M2 SERVICE MANUAL Part Number 6 74500...
Страница 2: ...Issued December 2003 6 74500 Bur Copyright 2003 Case LLC All Rights Reserved...
Страница 4: ...ENGINES 2 ED FEBUARY 2003...
Страница 7: ...ENGINES 5 ED FEBUARY 2003 UPDATING SECTION DESCRIPTION PAGE DATE OF REVISION...
Страница 8: ...ENGINES 6 ED FEBUARY 2003...
Страница 10: ...ENGINES 8 ED FEBUARY 2003...
Страница 12: ...ENGINES 2 ED FEBUARY 2003 SECTION 1 GENERAL SPECIFICATIONS...
Страница 18: ...ENGINES 8 ED FEBUARY 2003 SECTION 1 GENERAL SPECIFICATIONS...
Страница 22: ...ENGINES 12 ED FEBUARY 2003 SECTION 1 GENERAL SPECIFICATIONS...
Страница 24: ...ENGINES 2 SECTION 2 FEED ED FEBUARY 2003...
Страница 30: ...ENGINES 8 SECTION 2 FEED ED FEBUARY 2003...
Страница 40: ...SECTION 3 DUTY INDUSTRIAL APPLICATION 6 ENGINES ED FEBUARY 2003...
Страница 41: ...PART ONE MECHANICAL COMPONENTS SECTION 3 DUTY INDUSTRIAL APPLICATION MOTORI 7 ED FEBUARY 2003 DIAGNOSI...
Страница 42: ...SECTION 3 DUTY INDUSTRIAL APPLICATION 8 MOTORI ED FEBUARY 2003 DIAGNOSI...
Страница 104: ...SECTION 3 DUTY INDUSTRIAL APPLICATION 70 ENGINES ED FEBUARY 2003 zs...
Страница 107: ...PART TWO ELECTRICAL EQUIPMENT SECTION 3 DUTY INDUSTRIAL APPLICATION ENGINES 73 ED FEBUARY 2003 DIAGNOSI...
Страница 108: ...SECTION 3 DUTY INDUSTRIAL APPLICATION 74 ENGINES ED FEBUARY 2003 DIAGNOSI...
Страница 117: ...PART THREE TROUBLESHOOTING SECTION 3 DUTY INDUSTRIAL APPLICATION MOTORI 83 ED FEBUARY 2003 DIAGNOSI...
Страница 118: ...SECTION 3 DUTY INDUSTRIAL APPLICATION 84 MOTORI ED FEBUARY 2003 DIAGNOSI...
Страница 125: ...PART FOUR MAINTENANCE PLANNING SECTION 3 DUTY INDUSTRIAL APPLICATION ENGINES 91 ED FEBUARY 2003 DIAGNOSI...
Страница 126: ...SECTION 3 DUTY INDUSTRIAL APPLICATION 92 ENGINES ED FEBUARY 2003 DIAGNOSI...
Страница 134: ...SECTION 3 DUTY INDUSTRIAL APPLICATION 100 ENGINES ED FEBUARY 2003...
Страница 144: ...SECTION 4 OVERHAUL AND TECHNICAL SPECIFICATIONS 10 ENGINES ED FEBUARY 2003...
Страница 171: ...SECTION 5 TOOLS ENGINES 1 ED FEBUARY 2003 Tools SECTION 5 TOOLS 3 Page...
Страница 172: ...SECTION 5 TOOLS ENGINES 2 ED FEBUARY 2003...
Страница 174: ...SECTION 5 TOOLS ENGINES 4 ED FEBUARY 2003...
Страница 175: ...APPENDIX ENGINES 1 ED FEBUARY 2003 HYDRAULIC SYSTEM BRAKES APPENDIX Pagina SAFETY PRESCRIPTIONS 3...
Страница 176: ...APPENDIX 2 ENGINES ED FEBUARY 2003...