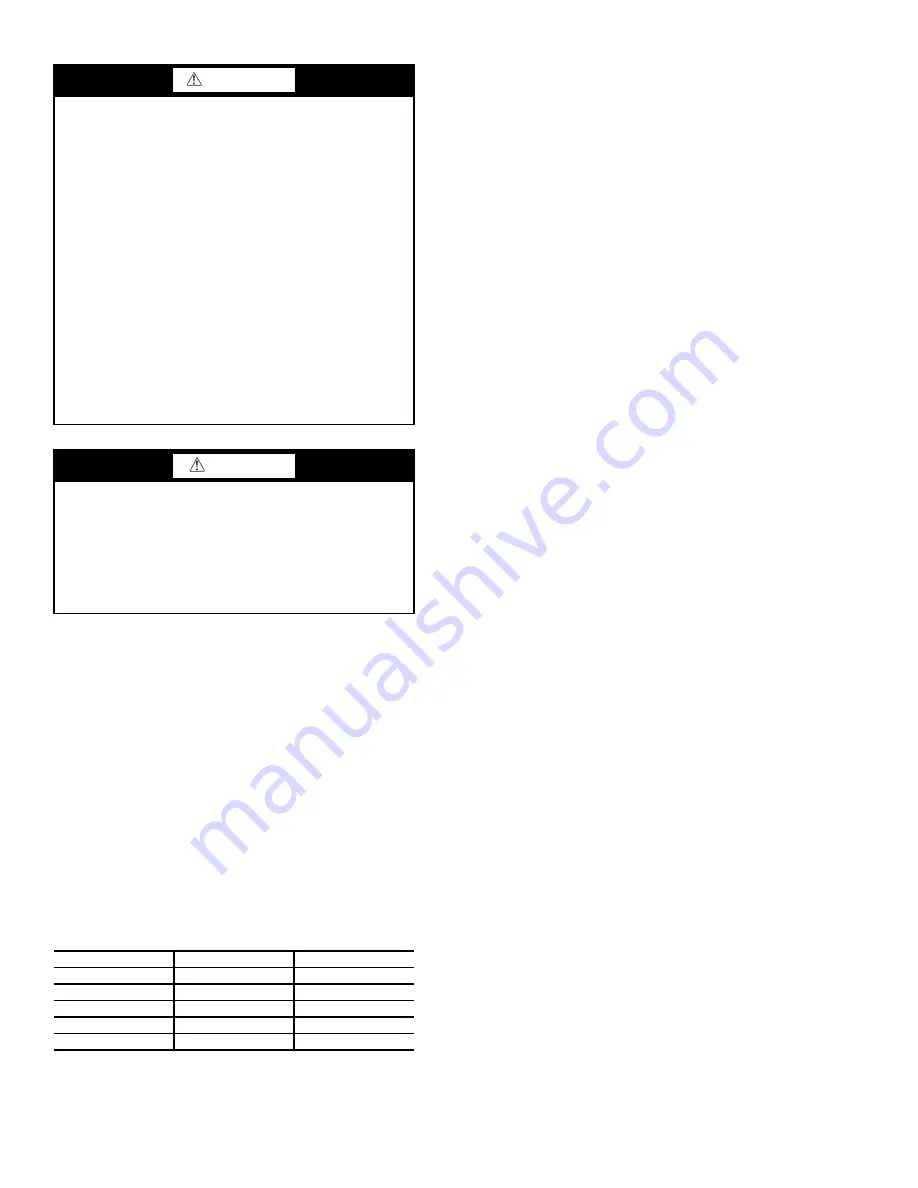
2
INTRODUCTION
These instructions cover installation of 30RB060-390 air-
cooled liquid chillers with electronic controls and units with
factory-installed options (FIOPs). See Fig. 1.
NOTE: The 30RB080-390 air-cooled chillers with Green-
speed
®
technology include high-efficiency variable condenser
fans. See Fig. 1.
NOTE: Unit sizes 315-390 are modular units that are shipped
in separate sections as modules A or B as noted in position 8 of
the unit model nomenclature. Installation directions specific to
these units are noted in these instructions. For modules 315A,
315B, 330A, 330B, 345A, 345B, and 360B, follow all general
instructions as noted for unit sizes 30RB160-170. For modules,
360A, 390A, and 390B follow instructions for 30RB190. See
Table 1 for a listing of unit sizes and modular combinations.
NOTE: The nameplate for modular units contains only the first
two digits in the model number. For example, 315A and 315B
nameplates read 31A and 31B.
Table 1 — Modular Combinations
NOTE: An “F” in the model number indicates the design series.
INSTALLATION
Storage —
If the unit is to be stored for a period of time
before installation or start-up, be sure to protect the machine
from construction dirt and moisture. Keep protective shipping
covers in place until machine is ready for installation.
Step 1 — Place, Rig and Mount the Unit
NOTE: Inspect the unit upon arrival for damage. If damage is
found, file a claim right away with the shipping company.
PLACING UNIT — When considering location for the unit,
be sure to consult National Electrical Code (NEC, U.S.A.) and
local code requirements. Allow sufficient space for airflow,
wiring, piping, and service. See Fig. 2-20. Be sure surface be-
neath the unit is level, and is capable of supporting the operat-
ing weight of the unit. See Fig. 21 and Tables 2-4B for unit lift-
ing points, mounting and operating weights.
Locate the unit so that the condenser airflow is unrestricted
both above and on the sides of the unit. Airflow and service
clearances are 6 ft (1.8 m) around the unit. Acceptable clear-
ance on the cooler connection side or end opposite the control
box unit can be reduced to 3 ft (1 m) without sacrificing perfor-
mance as long as the remaining three sides are unrestricted. Ac-
ceptable clearance on the side with a control box can be re-
duced to 4 ft (1.3 m) due to NEC regulations, without sacrific-
ing performance as long as the remaining three sides are
unrestricted. Provide ample room for servicing and removing
cooler. See Fig. 2-20 for required clearances. Local codes for
clearances take precedence over the manufacturer’s recom-
mendations when local codes call for greater clearances.
Modular units (30RB315-390) must be installed with a min-
imum separation end to end of 4 ft (1.3 m) for airflow and ser-
vice clearance along with NEC regulations.
If multiple units are installed at the same site, a separation of
10 ft (3 m) between the sides of the machines is required to
maintain proper airflow and minimize the chances of condens-
er air recirculation.
MOUNTING UNIT — The unit may be mounted on a level
pad directly on the base rails, on rails along the long axis of the
machine, or on vibration isolation springs. For all units, ensure
placement area is strong enough to support unit operating
weight. Mounting holes are provided for securing the unit to
the pad or vibration isolation springs. The base rail can be point
loaded at the mounting points. The base rail is made from steel,
which is formed into what is shown in Fig. 22. See Fig. 2-20
for locations of mounting points. At the mounting points, a U-
shaped channel is welded into the base rail to provide a flat
plate for mounting. See Fig. 23 for mounting plate dimensions.
The 1
9
/
16
in. (40 mm) dimension shown is to the mounting hole
from the outside edge of the rail.
NOTE: The 1
9
/
16
in. (40 mm) dimension in Fig. 23 is not the
same dimension as the 1.42 in. (36 mm) flange that is turned
under the base rail in Fig. 22.
Bolt the unit securely to pad or rails. If vibration isolators
(field-supplied) are required for a particular installation, refer to
unit weight distribution in Fig. 21 to aid in the proper selection
of isolators. The 30RB units can be mounted directly on spring
isolators. For each unit or module, the final unit location must
be level so that oil will equalize properly.
RIGGING UNIT — The 30RB060-390 units are designed for
overhead rigging and it is important that this method be
used. Holes are provided in frame base channels, marked for
rigging (see rigging label on unit). It is recommended that
field-supplied shackles be used to facilitate lifting. Secure the
shackles to the base rails at the points noted on the rigging
label. See Table 2 for the number of lifting points for each unit.
Do not use a forklift truck to move the units.
WARNING
DO NOT USE TORCH to remove any component. System
contains oil and refrigerant under pressure.
To remove a component, wear protective gloves and gog-
gles and proceed as follows:
a. Shut off electrical power to unit.
b. Recover refrigerant to relieve all pressure from sys-
tem using both high-pressure and low pressure ports.
c. Traces of vapor should be displaced with nitrogen
and the work area should be well ventilated. Refrig-
erant in contact with an open flame produces toxic
gases.
d. Cut component connection tubing with tubing cutter
and remove component from unit. Use a pan to catch
any oil that may come out of the lines and as a gage
for how much oil to add to the system.
e. Carefully unsweat remaining tubing stubs when nec-
essary. Oil can ignite when exposed to torch flame.
Failure to follow these procedures may result in personal
injury or death.
CAUTION
DO NOT re-use compressor oil or any oil that has been
exposed to the atmosphere. Dispose of oil per local codes
and regulations. DO NOT leave refrigerant system open to
air any longer than the actual time required to service the
equipment. Seal circuits being serviced and charge with
dry nitrogen to prevent oil contamination when timely
repairs cannot be completed. Failure to follow these proce-
dures may result in damage to equipment.
MODULE UNITS
MODULE A
MODULE B
30RBF315
30RBF160
30RBF160
30RBF330
30RBF170
30RBF160
30RBF345
30RBF170
30RBF170
30RBF360
30RBF190
30RBF170
30RBF390
30RBF190
30RBF190
Содержание MINIMUM LOAD CONTROL ACCESSORY 30RB060-390
Страница 36: ...36 Fig 24 Unit Rigging Label Detail 30RB060 150...
Страница 37: ...37 Fig 25 Unit Rigging Label Detail 30RB160 300...
Страница 74: ......
Страница 75: ......