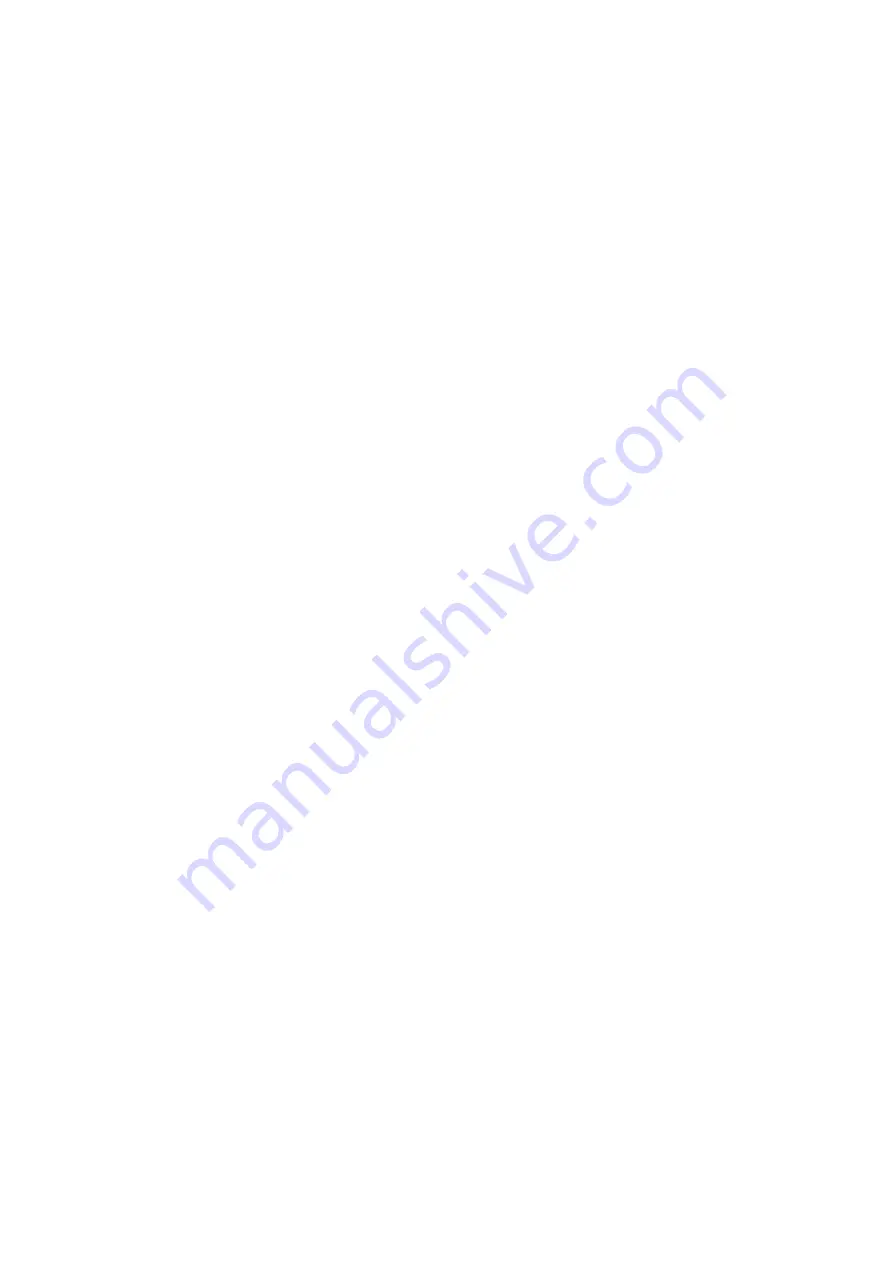
25
The diagrams in the appendix can obviously be used to
calculate the actual pressure drops for the piping under
consideration:
7. Based on the pipe diameter and the cooling capacity
find the equivalent length, producing 1.5 K pressure
drop in he graphs “Discharge piping” and “Liquid line
piping”.
8. Calculate the equivalent pipe length as described in
steps 1, 2, 3 and 5.
9. Calculate the length ratio from steps 8 and 7 (equiva-
lent length from step 8 DIVIDED by the equivalent
length from step 7).
10. Multiply this ratio by 1.5 to find the equivalent pressure
drops in K.
8.4 - Discharge pipe sizing
The discharge piping must be sized to achieve reasonable
pressure drops: a variation of 1.5 K of the saturated
tempe-rature is normally accepted (approx. 60 kPa
variation for a condensing temperature of 50°C).
For most applications the refrigerant gas velocity is suffi-
cient to entrain the liquid refrigerant/oil mixture. Neverthe-
less, Table 2 shows the minimum required cooling capacities
for different pipe diameters and different saturated
dis-charge temperatures.
This table is based on 8 K superheat, a saturated suction
temperature of 4°C and 8 K subcooling. Table 3 shows the
correction factors to be applied to the values from Table 2, if
the operating conditions are different from those previously
stated.
8.5 - liquid pipe sizing
The 30RWA compressors are supplied with an oil that is
fully miscible with refrigerant R-407C in the liquid phase.
Consequently low refrigerant velocities in the liquid lines
are not a problem.
The admissible pressure drops in the liquid lines depend
mainly on the subcooling level of the liquid refrigerant at
the condenser outlet. Pressure drops corresponding to 1.5°C
saturated temperature must not be exceeded.
Special attention must be paid to the liquid line sizing when
the expansion device ist positioned higher than the conden-
ser. It may now be necessary to increase the pipe diameter
to compensate for the additional pressure of the liquid
refrigerant column. If the liquid refrigerant head ist very
high, it may even be necessary to increase the subcooling
to prevent an phase change in the liquid line. This can be
done e.g. by a liquid-vapour heat exchanger or an additional
coil.
At 45°C the volume mass of refrigerant R-407C in the liquid
phase is approximately 1050 kg/m
3
. A pressure of 1 bar
corresponds to a liquid head of: 100 000/(1050 x 9.81) = 9.7 m.