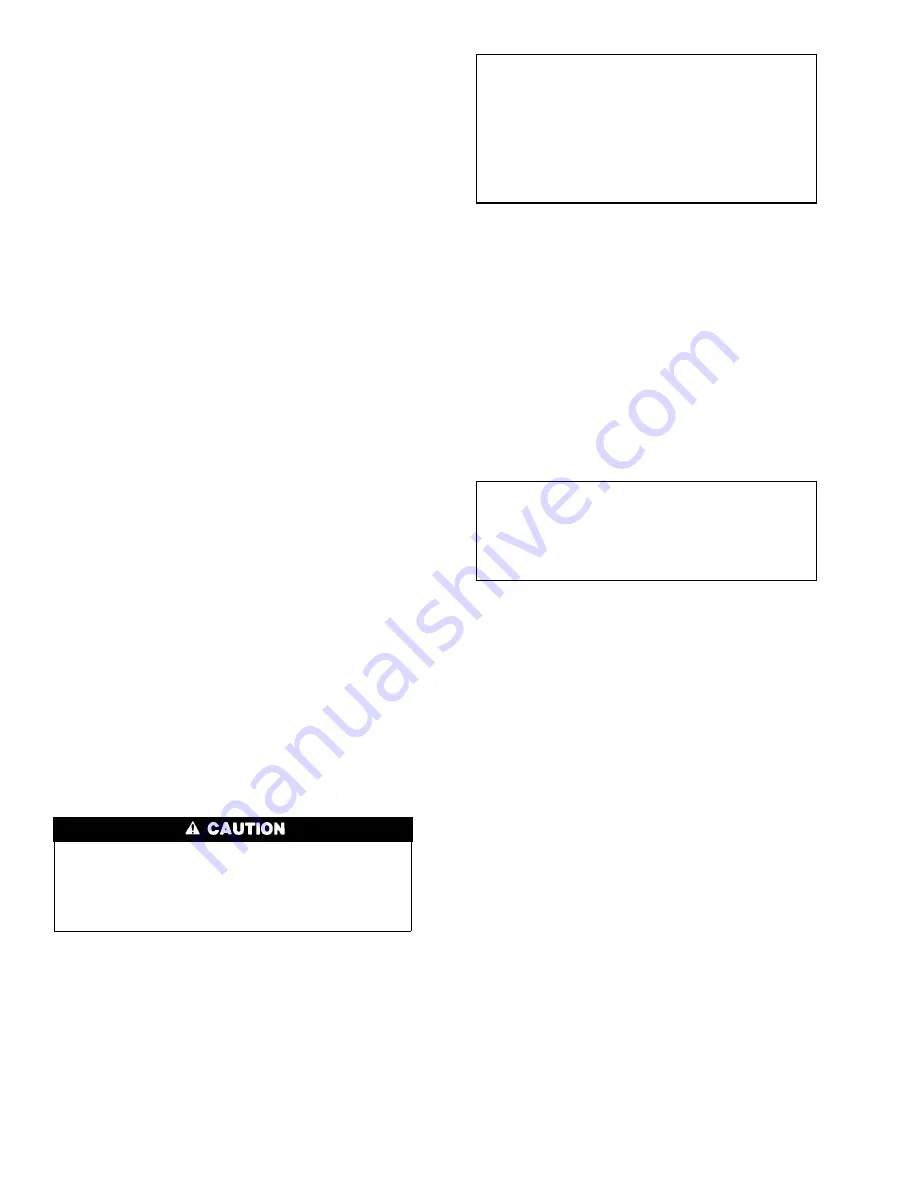
This feature helps diagnose a system problem in case of a
component failure. To initiate component test procedure, short
(jumper) the TEST 1/4-in. quick connect terminal on control
board (adjacent to diagnostic light) and the Com terminal on
thermostat connection block for approximately 2 sec. (See Fig.
11.)
NOTE:
Component test feature will not operate if any thermostat
signal is present at control center.
Component test sequence is as follows.
a. Momentarily jumper TEST and Com terminals until LED
goes off.
b. LED will display previous fault 4 times.
c. Inducer motor operates for 10 sec, then stops.
d. Hot surface ignitor is energized for 15 sec, then de-
energized.
e. Blower motor operates on cooling speed for 10 sec, then
stops.
f. Blower motor operates on heating speed for 10 sec, then
stops.
3. To operate furnace, follow procedures on operating instruction
label attached to furnace.
4. With furnace operating, set thermostat below room tempera-
ture and observe that furnace goes off. Set thermostat above
room temperature and observe that furnace restarts.
ADJUSTMENTS
1. Set gas input rate.
There are 2 methods of adjusting the gas input rate. The
preferred method is by using Table 7 and following instruc-
tions in item a. The second method is by clocking the gas
meter and following instructions in item b.
The gas valve regulator has been nominally set at 3.5-in. wc
for natural gas. When adjusting input rate, do not set manifold
pressure above 3.8-in. wc or below 3.2-in. wc.
a. Check gas input rate using Table 7.
(1.) Obtain average yearly heat value for local gas supply.
(2.) Obtain average yearly specific gravity for local gas
supply.
(3.) Verify furnace model. Table 7 can only be used for
model 58RAV Furnaces.
(4.) Check and verify orifice size in furnace. NEVER
ASSUME THE ORIFICE SIZE. ALWAYS CHECK
AND VERIFY.
DO NOT redrill burner orifices. Improper drilling (burrs,
out-of-round holes, etc.) can cause excessive burner noise and
misdirection of burner flames. This can result in flame
impingement of the burners and heat exchangers, causing
failure.
(5.) Find natural gas heat value and specific gravity in
Table 7.
(6.) Follow heat value and specific gravity lines to point of
intersection. Find orifice size and manifold pressure
settings for proper operation at given natural gas
conditions.
EXAMPLE:
Heat value 1070 Btu/cu ft
Specific gravity 0.58
Therefore; Orifice No. 44 *
Manifold pressure 3.6-in. wc
* The furnace is shipped with No. 43 orifices. Therefore, in
this example all main burner orifices must be changed and
the manifold pressure must be adjusted.
(7.) Proceed to item c to adjust manifold pressure.
b. Check gas input rate by clocking gas meter.
(1.) Obtain average yearly heat value for local gas supply.
(2.) Check and verify orifice size in furnace. NEVER
ASSUME THE ORIFICE SIZE. ALWAYS CHECK
AND VERIFY.
(3.) Turn off all other gas appliances and pilots.
(4.) Start furnace and let run for 3 minutes.
(5.) Measure time (in sec) for gas meter to complete 1
revolution.
(6.) Refer to Table 8 for cu ft of gas per hr.
(7.) Multiply gas rate (cu ft/hr) by heating value (Btu/cu
ft).
EXAMPLE:
Btu heating input = Btu/cu ft X cu ft/hr
Heating value of gas = 1070 Btu/cu ft
Time for 1 revolution of 2-cu ft dial = 72 sec
Gas rate = 100 X 1070 = 107,000 Btuh
(8.) Check to make sure that measured gas input does not
exceed gas input on unit rating plate.
(9.) Proceed to item c to adjust manifold pressure.
c. Adjust gas input.
(1.) Remove regulator adjustment seal cap. (See Fig. 14.)
(2.) Turn adjusting screw counterclockwise to decrease
input. Turn screw clockwise to increase input. DO
NOT set manifold pressure less than 3.2-in. wc or
more than 3.8-in. wc for natural gas. Make any major
adjustments by changing main burner orifices.
(3.) When correct input is obtained, replace regulator
adjustment seal cap. Main burner flame should be
clear blue, almost transparent. (See Fig. 15.)
d. High altitude—In the United States, gas input on unit rating
plate is for altitudes up to 2000 ft. Ratings for altitudes over
2000 ft must be 4 percent less for each 1000 ft above sea
level. To obtain the adjusted altitude rating, adjust the
manifold pressure, item c, and replace the main burner
orifices as needed. Refer to NFGC Appendix F, Table F-4
for proper orifice sizing at high altitudes.
e. Canadian installations only—The Canadian ratings are
approved for altitudes up to 2000 ft for natural and propane
gases. High-altitude ratings are from 2000 ft to 4500 ft
above sea level. See Table 9 for nominal burner orifice
size. High-altitude input ratings include a 10 percent
derated as required by Canadian standards.
2. Set temperature rise.
Furnace must operate within range of temperature rise speci-
fied on the unit rating plate. Determine the air temperature rise
as follows.
12