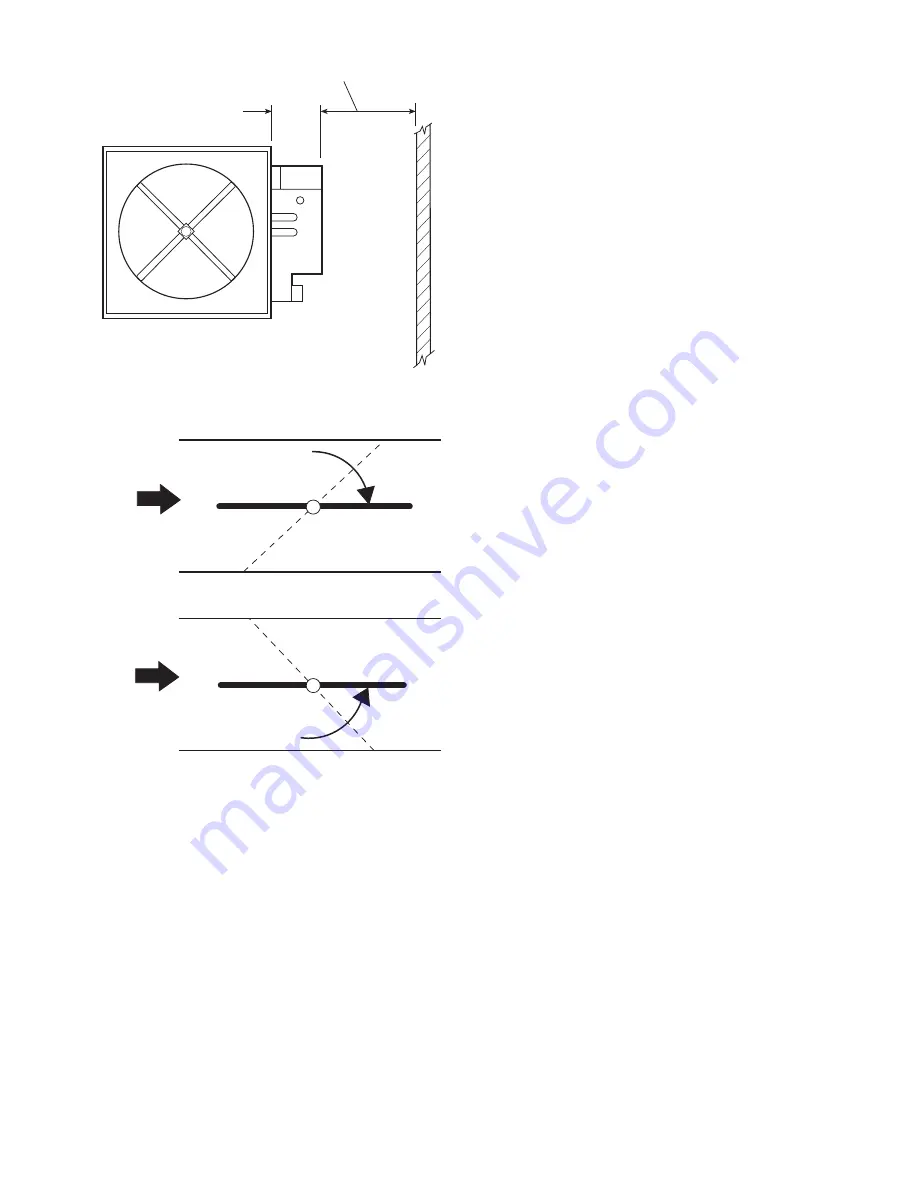
5
7. Mount the zone controller to the terminal by sliding the
damper shaft through the actuator clamp assembly.
Secure the zone controller to the duct by installing the
screw provided through the grommet in the anti-rotation
tab or by attaching the mounting bracket to the damper.
Be sure the floating grommet is in the center of the slot.
Failure to center the grommet may cause the actuator to
stick or bind.
8. Tighten the actuator clamp assembly to the damper shaft.
Secure by tightening the two 10-mm nuts.
9. If the damper has less than 90 degrees of travel between
the fully open and fully closed positions, then a mechani-
cal stop must be set on the actuator. The mechanical stop
prevents the damper from opening past the maximum
damper position. To set the mechanical stop, perform the
following procedure:
a. Press the actuator release button and rotate the
damper to the fully open position.
b. Using a Phillips screwdriver, loosen the appropri-
ate stop clamp screw.
c. Move the stop clamp screw so that it contacts the
edge of the cam on the actuator. Secure the stop
clamp screw in this position by tightening the
screw.
10. Verify that the damper opens and closes. Press the actua-
tor release button and rotate the damper. Verify that the
damper does not rotate past the fully open position.
Release the button and lock the damper in the fully open
position.
NOTE: The actuator must rotate to the end of the actuator
range in the fully closed position. For actuators with less than
90 degrees of travel, the opposite stop must be moved so the
actuator travels to mid-range when fully open. Damper calibra-
tion will fail if stops on actuator are not set correctly.
Connect the Power Transformer —
An individual,
field-supplied, 24-vac power transformer is recommended
for each zone controller. If multiple zone controllers are
powered from one power transformer (100 va maximum for
UL [Underwriters’ Laboratories] Class 2 conformance),
maintain polarity on the power input terminals. All transformer
secondaries are required to be grounded. Use only stranded
copper conductors for all wiring to the zone controller. Wiring
connections must be made in accordance with NEC (National
Electrical Code) and local codes. Ground the transformer at the
transformer location. Provide an 18-gage, green, chassis
ground wire at the terminal.
The power supply is 24 vac ± 10% at 40 va (50/60 Hz).
For VVT® zone controllers, the power requirement sizing
allows for accessory water valves and for electric heat contac-
tor(s). Water valves are limited to 15 va on both two-position
and modulating hot water. The electric heat contactor(s) are
limited to 10 va (holding) each.
NOTE: If a water valve or electric heat contactor exceeds these
limits, or external contactors are required for electric heat, then
it is recommended a 60 va transformer be used. The maximum
rating for any output is 20 va.
NOTE: Do not run sensor or communication wiring in the
same conduit with line-voltage wiring.
NOTE: A conduit cover is provided and integrated with the
zone controller.
Perform the following steps to connect the power
transformer:
1. Install the field-supplied transformer in an electrical
enclosure that conforms to NEC and local codes.
2. Connect 24 vac from the transformer as shown in the
applicable wiring diagram (Fig. 5-13)
.
END VIEW INLET
ZONE
CONTROLLER
ALLOW 12” CLEARANCE FOR SERVICE
ACCESS TO CONTROL BOX
3” REF.
Fig. 3 — Service Clearance for
Zone Controller Mounting
AIR
FLOW
AIR
FLOW
CW TO OPEN, CCW TO CLOSE
CCW TO OPEN, CW TO CLOSE
Fig. 4 — Damper Configuration
Содержание 3V VVT 33ZCVVTZC-01
Страница 59: ......