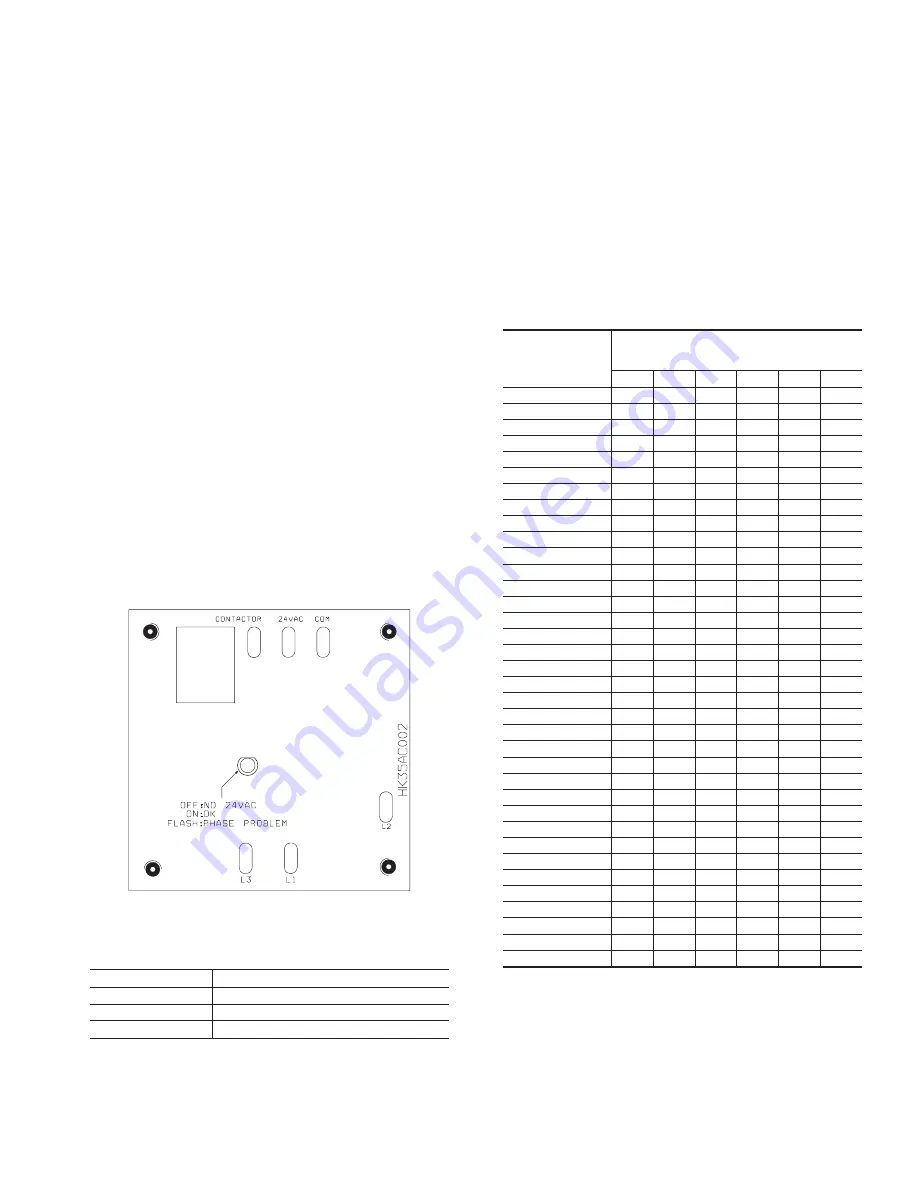
Follow these steps to properly start up the system.
1. After system is evacuated, fully back seat (open) liquid and
vapor service valves.
2. Unit is shipped with valve stem(s) front seated (closed) and
caps installed. replace stem caps after system is opened to
refrigerant flow. Replace caps finger-tight and tighten with
wrench an additional 1/12 turn.
3. Close electrical disconnects to energize system.
4. Set room thermostat at desired temperature. Be sure set point
is below indoor ambient temperature.
5. Set room thermostat to COOL and fan control to ON or AUTO
mode, as desired. Operate unit for 15 minutes Check system
refrigerant charge.
SEQUENCE OF OPERATION
Turn on power to indoor and outdoor units. Transformer is
energized.
On a call for cooling, thermostat makes circuits R-Y and R-G. On
three phase models with scroll compressors, the units are equipped
with a phase monitor to detect in the incoming power is correctly
phased for compressor operation. If the phasing is correct, circuit
R-Y energizes contactor, starting outdoor fan motor and compres-
sor circuit. R-G energizes indoor unit blower relay, starting indoor
blower motor on high speed.
NOTE:
If the phasing is incorrect, the contactor will not be
energized. To correct the phasing, interchange any two of the three
power connections on the field side.
When thermostat is satisfied, its contacts open, de-energizing
contactor and blower relay. Compressor and motors stop.
If indoor unit is equipped with a time-delay relay circuit, the
indoor blower runs an additional 90 sec to increase system
efficiency.
Step 12—Check Charge
UNIT CHARGE
Factory charge and charging method are shown on unit informa-
tion plate. Charge Puron® units using a commercial-type metering
device in manifold hose. Charge refrigerant into suction line.
NOTE:
If superheat or subcooling charging conditions are not
favorable, charge must be weighed in accordance with unit rating
plate ± 0.6 oz/ft of 3/8-in. liquid line above or below 15 ft
respectively.
Fig. 10—Phase Monitor Control
A00010
Table 3—Phase Monitor Led Indicators
LED
STATUS
OFF
No call for compressor operation
FLASHING
Reversed phase
ON
Normal
Table 4—Required Liquid-Line Temperature (°F)
LIQUID
PRESSURE AT
SERVICE VALVE
REQUIRED SUBCOOLING
TEMPERATURE
(°F)
8
10
12
14
16
18
189
58
56
54
52
50
48
195
60
58
56
54
52
50
202
62
60
58
56
54
52
208
64
62
60
58
56
54
215
66
64
62
60
58
56
222
68
66
64
62
60
58
229
70
68
66
64
62
60
236
72
70
68
66
64
62
243
74
72
70
68
66
64
251
76
74
72
70
68
66
259
78
76
74
72
70
68
266
80
78
76
74
72
70
274
82
80
78
76
74
72
283
84
82
80
78
76
74
291
86
84
82
80
78
76
299
88
86
84
82
80
78
308
90
88
86
84
82
80
317
92
90
88
86
84
82
326
94
92
90
88
86
84
335
96
94
92
90
88
86
345
98
96
94
92
90
88
354
100
98
96
94
92
90
364
102
100
98
96
94
92
374
104
102
100
98
96
94
384
106
104
102
100
98
96
395
108
106
104
102
100
98
406
110
108
106
104
102
100
416
112
110
108
106
104
102
427
114
112
110
108
106
104
439
116
114
112
110
108
106
450
118
116
114
112
110
108
462
120
118
116
114
112
110
474
122
120
118
116
114
112
486
124
122
120
118
116
114
499
126
124
122
120
118
116
511
128
126
124
122
120
118
7