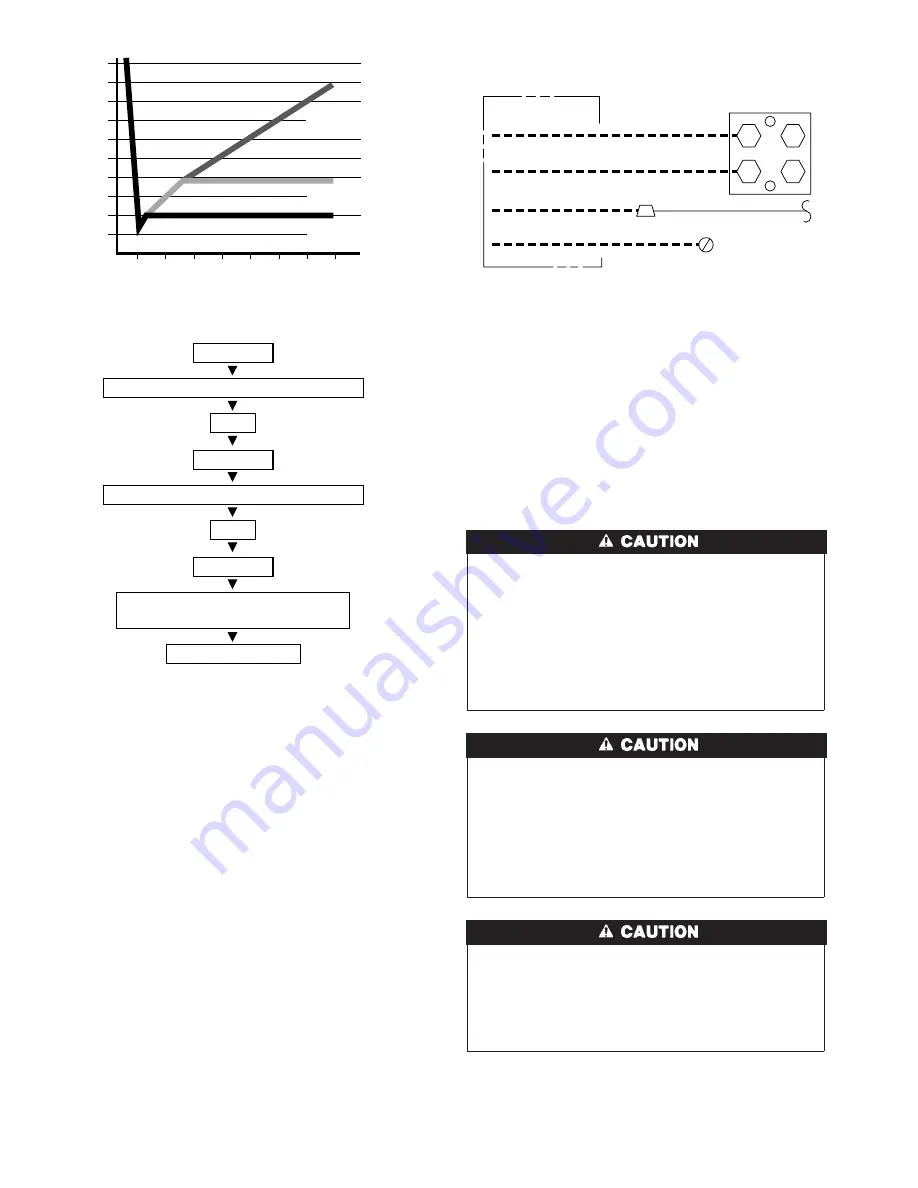
CONNECT CONTROL WIRING
Route 24v control wires through control wiring grommet and
connect leads to control wiring. (See Fig. 11.)
Use No. 18 AWG color-coded, insulated (35°C minimum) wire. If
thermostat is located more than 100 ft from unit, as measured
along the control voltage wires, use No. 16 AWG color-coded wire
to avoid excessive voltage drop.
All wiring must be NEC Class 1 and must be separated from
incoming power leads.
Use furnace transformer, fan coil transformer, or accessory trans-
former for control power, 24v/40va minimum.
NOTE:
Use of available 24v accessories may exceed the mini-
mum 40va power requirement. Determine total transformer load-
ing and increase the transformer capacity or split the load with an
accessory transformer as required.
FINAL WIRING CHECK
IMPORTANT:
Check factory wiring and field wire connections
to ensure terminations are secured properly. Check wire routing to
ensure wires are not in contact with tubing, sheet metal, etc.
Step 9—Compressor Crankcase Heater
When equipped with a crankcase heater, furnish power to heater a
minimum of 24 hr before starting unit. To furnish power to heater
only, set thermostat to OFF and close electrical disconnect to
outdoor unit.
A crankcase heater is required if refrigerant tubing is longer than
50 ft. Refer to Application Guideline and Service Manual —
Residential Split-System Air Conditioners and Heat Pumps using
Puron® Refrigerant.
Step 10—Install Electrical Accessories
Refer to the individual instructions packaged with kits or acces-
sories when installing.
Step 11—Start-Up
To prevent compressor damage or personal injury, observe
the following:
•Do not overcharge system with refrigerant.
•Do not operate unit in a vacuum or at negative pressure.
•Do not vent refrigerant to atmosphere. Recover during
system repair or final unit disposal.
•Do not disable low-pressure switch.
In scroll-compressor applications:
•Dome temperatures may be hot.
To prevent personal injury wear safety glasses, protective
clothing, and gloves when handling refrigerant and observe
the following:
•Back-seating service valves are not equipped with Schrader
valves. Fully back seat (counterclockwise) valve stem before
removing gage-port cap.
•Front-seating service valves are equipped with Schrader
valves.
• 3-phase scroll compressors are rotation sensitive.
• A flashing LED on phase monitor indicates reverse rotation.
(See Fig. 10 and Table 3.)
• This will not allow contactor to be energized.
• Disconnect power to unit and interchange 2 field wiring
leads on unit contactor.
Fig. 7—Deep Vacuum Graph
A95424
500
MINUTES
0
1
2
3
4
5
6
7
1000
1500
LEAK IN
SYSTEM
VACUUM TIGHT
TOO WET
TIGHT
DRY SYSTEM
2000
MICRONS
2500
3000
3500
4000
4500
5000
A95424
Fig. 8—Triple Evacuation Method
A95425
CHECK FOR TIGHT, DRY SYSTEM
(IF IT HOLDS DEEP VACUUM)
EVACUATE
BREAK VACUUM WITH DRY NITROGEN
WAIT
EVACUATE
CHARGE SYSTEM
BREAK VACUUM WITH DRY NITROGEN
EVACUATE
WAIT
Fig. 9—Line Power Connections
A94025
DISCONNECT
PER N.E.C. AND/OR
LOCAL CODES
CONTACTOR
GROUND
LUG
FIELD GROUND
WIRING
FIELD POWER
WIRING
BLUE
3 PHASE ONLY
6