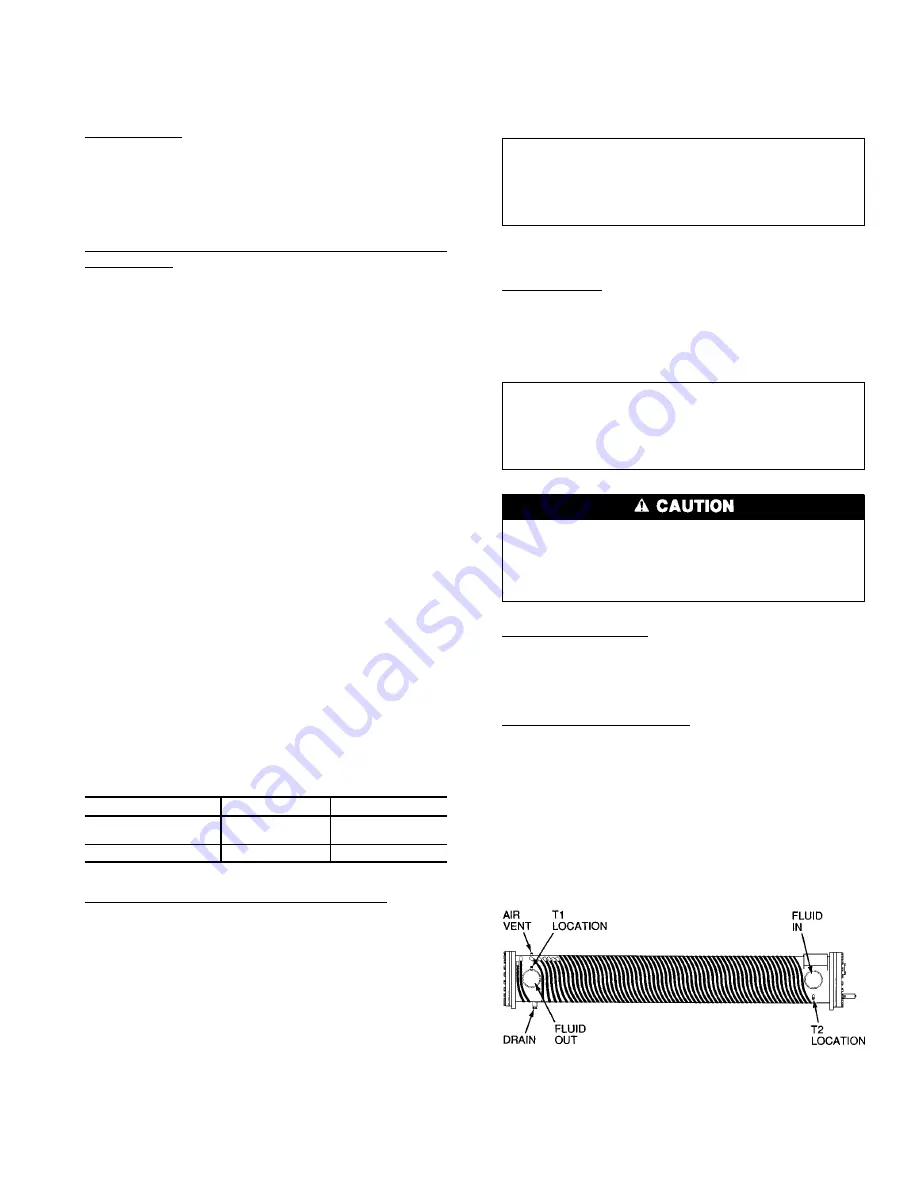
Safety Devices —
Chillers contain many safety
devices and protection logic built into electronic control. Fol-
lowing is a brief summary of major safeties. For complete
details, refer to Controls and Troubleshooting literature.
COMPRESSOR PROTECTION
Circuit Breaker — One manual reset calibrated-trip mag-
netic circuit breaker for each compressor protects against over-
current. Do not bypass or increase size of a breaker to
correct problems. Determine cause for trouble and correct
before resetting breaker. Circuit breaker must-trip amps (MTA)
are listed on individual circuit breakers, and on unit label
diagrams.
30GT080-110 AND 230B-315B Compressor Protection
Board (CPCS) — The CPCS is used to control and protect
compressors and crankcase heaters. Board provides follow-
ing features:
• Compressor contactor control
• Crankcase heater control
• Ground current protection
• Status communication to processor board
• High-pressure protection
One large relay is located on CPCS board that controls
crankcase heater and compressor contactor. In addition, re-
lay provides a set of contacts that microprocessor monitors
to determine operating status of compressor. If processor board
determines that compressor is not operating properly through
signal contacts, control locks compressor off.
The CPCS contains logic that can detect if current-to-
ground of any winding exceeds 2.5 amps; if so, compressor
shuts down.
A high-pressure switch with a trip pressure of 426
± 7 psig (2,936 ± 48 kPa) is mounted on each compressor;
switch setting is shown in Table 18. Switch is wired in series
with the CPCS. If switch opens, CPCS relay opens, proces-
sor detects it through signal contacts and compressor locks
off.
If any of these switches open during operation, the com-
pressor stops and the failure is detected by processor when
signal contacts open. If lead compressor in either circuit is
shut down by high pressure switch, ground current protec-
tor, loss of charge switch, or oil pressure switch, all com-
pressors in the circuit are locked off.
Table 18 — Pressure Switch Settings, psig
(kPa)
SWITCH
CUTOUT
CUT-IN
High Pressure
426 ± 7
(2936 ± 48)
320 ± 20
(2205 ± 138)
Loss-of-Charge
7 (48.2)
22 (151.6)
30GT130-210, 230A-315A, AND 330A/B-420A/B — A con-
trol relay in conjunction with a ground fault module replaces
the function of the CPCS. To reset, press the push-button
switch on the module.
LOW OIL PRESSURE PROTECTION — Lead compressor
in each circuit is equipped with a switch to detect low oil
pressure. Switch is connected directly to processor board.
Switch is set to open at approximately 5 psig (35 kPa) and
to close at 9 psig (62 kPa) maximum. If switch opens
when compressor is running, processor board stops all com-
pressors in circuit. During start-up, switch is bypassed for
2 minutes.
CRANKCASE HEATERS — Each compressor has a 180-w
crankcase heater to prevent absorption of liquid refrigerant
by oil in crankcase when compressor is not running. Heater
power source is auxiliary control power, independent of main
unit power. This assures compressor protection even when
main unit power disconnect switch is off.
IMPORTANT: Never open any switch or disconnect
that deenergizes crankcase heaters unless unit is being
serviced or is to be shut down for a prolonged period.
After a prolonged shutdown or a service job, energize
crankcase heaters for 24 hours before starting unit.
COOLER PROTECTION
Freeze Protection — Cooler can be wrapped with heater cables
as shown in Fig. 33, which are wired through an ambient
temperature switch set at 36 F (2 C). Entire cooler is cov-
ered with closed-cell insulation, applied over heater cables.
Heaters plus insulation protect cooler against low ambient
temperature freeze-up to 0° F (−18 C).
IMPORTANT: If unit is installed in an area where am-
bient temperatures fall below 32 F (0° C), it is rec-
ommended that inhibited ethylene glycol or other suit-
able corrosion-inhibitive antifreeze solution be used in
chilled-liquid circuit.
If coolers are equipped with heaters and the coolers are
drained during the non-cooling season, the cooler heat-
ers MUST be disconnected by removing fuse no. 1. With-
out fluid in the cooler, the heater could reach a tempera-
ture that damages the cooler insulation.
Low Fluid Temperature — Microprocessor is programmed
to shut chiller down if leaving fluid temperature drops be-
low 35 F (1.7 C). When fluid temperature rises to 6° F
(3.3° C ) above leaving fluid set point, safety resets and chiller
restarts.
Loss of Fluid Flow Protection — Microprocessor contains
internal logic that protects cooler against loss of cooler flow.
Entering and leaving fluid temperature sensors in cooler
detect a no-flow condition. Leaving sensor is located in leav-
ing fluid nozzle and entering sensor is located in first cooler
baffle space in close proximity to cooler tubes, as shown in
Fig. 23. When there is no cooler flow and the compressors
start, leaving fluid temperature does not change. However,
entering fluid temperature drops rapidly as refrigerant enters
cooler through EXV. Entering sensor detects this tempera-
ture drop and when entering temperature is 5° F (2.8° C)
below leaving temperature, unit stops and is locked off.
T — Thermistor
Fig. 33 — Cooler Heater Cables
67