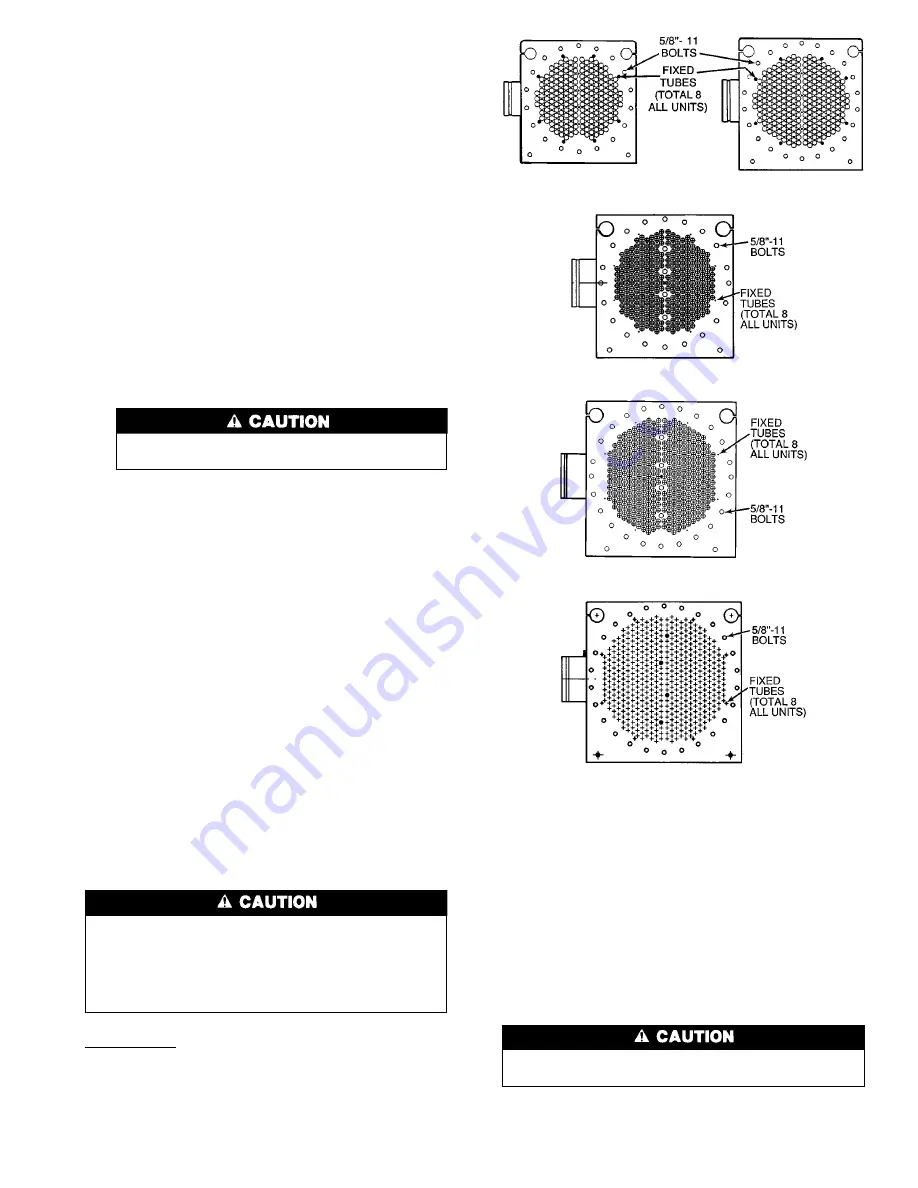
REPLACING COOLER — To replace the cooler:
1. Insert new cooler carefully into place. Reattach the screws
into the cooler feet (using saved screws).
On 30GT080-110 and 230B-315B units, reattach the 2
vertical supports under the condenser coil in front of the
cooler using screws saved.
2. Replace the liquid lines and solder at the cooler liquid
line nozzles.
3. Rebolt the suction flanges onto the cooler head using bolts
saved during removal. Use new gaskets for the suction
line flanges. Use compressor oil to aid in gasket sealing
and tighten the suction flange bolts to 70 to 90 ft-lb
(94 to 122 N-m).
NOTE: The suction flange has a 4-bolt pattern. See Carrier
specified parts for replacement part number, if necessary.
4. Using adhesive, reinstall the cooler insulation on the re-
frigerant connection end of the cooler.
5. Reinstall the thermistors. Refer to Thermistors section on
page 65, and install as follows:
a. Apply pipe sealant to the
1
⁄
4
-in. NPT threads on the
replacement coupling for the fluid side, and install it
in place of the original.
Do not use the packing nut to tighten the coupling.
Damage to the ferrules will result.
b. Reinstall thermistor T1 well, and insert thermistor T1
into well.
c. Install thermistor T2 (entering fluid temperature) so that
it is not touching an internal refrigerant tube, but so
that it is close enough to sense a freeze condition. The
recommended distance is
1
⁄
8
in. (3.2 mm) from the cooler
tube. Tighten the packing nut finger tight, and then tighten
1
1
⁄
4
turns more using a back-up wrench.
6. Install the cooler heater and conduit (if equipped), con-
necting the wires as shown in the unit wiring schematic
located on the unit.
7. Close the air vent at the top of the cooler, and close the
drain on the bottom of the cooler near the leaving fluid
outlet. Both the drain and the air vent are located on the
leaving fluid end of the cooler. See Fig. 23.
8. Reconnect the cooler fluid piping, and open the shutoff
valves (if installed). Purge the fluid of all air before start-
ing unit.
9. Open the discharge service valves, close the circuit break-
ers, and open the liquid line service valves for the
compressors.
SERVICING COOLER — When cooler heads and partition
plates are removed, tube sheets are exposed showing ends of
tubes.
Certain tubes in the 10HB coolers cannot be removed.
Eight tubes in the bundle are secured inside the cooler
to the baffles and cannot be removed. These tubes are
marked by a dimple on the tube sheet. See Fig. 24. If
any of these tubes have developed a leak, plug the tube(s)
as described under Tube Plugging section below.
Tube Plugging — A leaky tube can be plugged until re-
tubing can be done. The number of tubes plugged deter-
mines how soon cooler must be retubed. Tubes plugged in
the following locations will affect the performance of the
unit: Any tube in the area of thermistor T2, particularly the
tube that thermistor T2 is adjacent to, will affect unit reli-
ability and performance. Thermistor T2 is used in the freeze
protection algorithm for the controller. If several tubes re-
quire plugging, check with your local Carrier representative
to find out how number and location can affect unit capacity.
Figure 25 shows an Elliott tube plug and a cross-sectional
view of a plug in place.
Use extreme care when installing plugs to prevent dam-
age to the tube sheet section between the holes.
SIZES 080,090*
SIZES 100,110*
SIZES 130,150*
SIZES 170,190*
SIZE 210*
*And associated modular units (see Table 1).
Fig. 24 — Typical Tube Sheets, Cover Off
(Non-Removable Tubes)
59