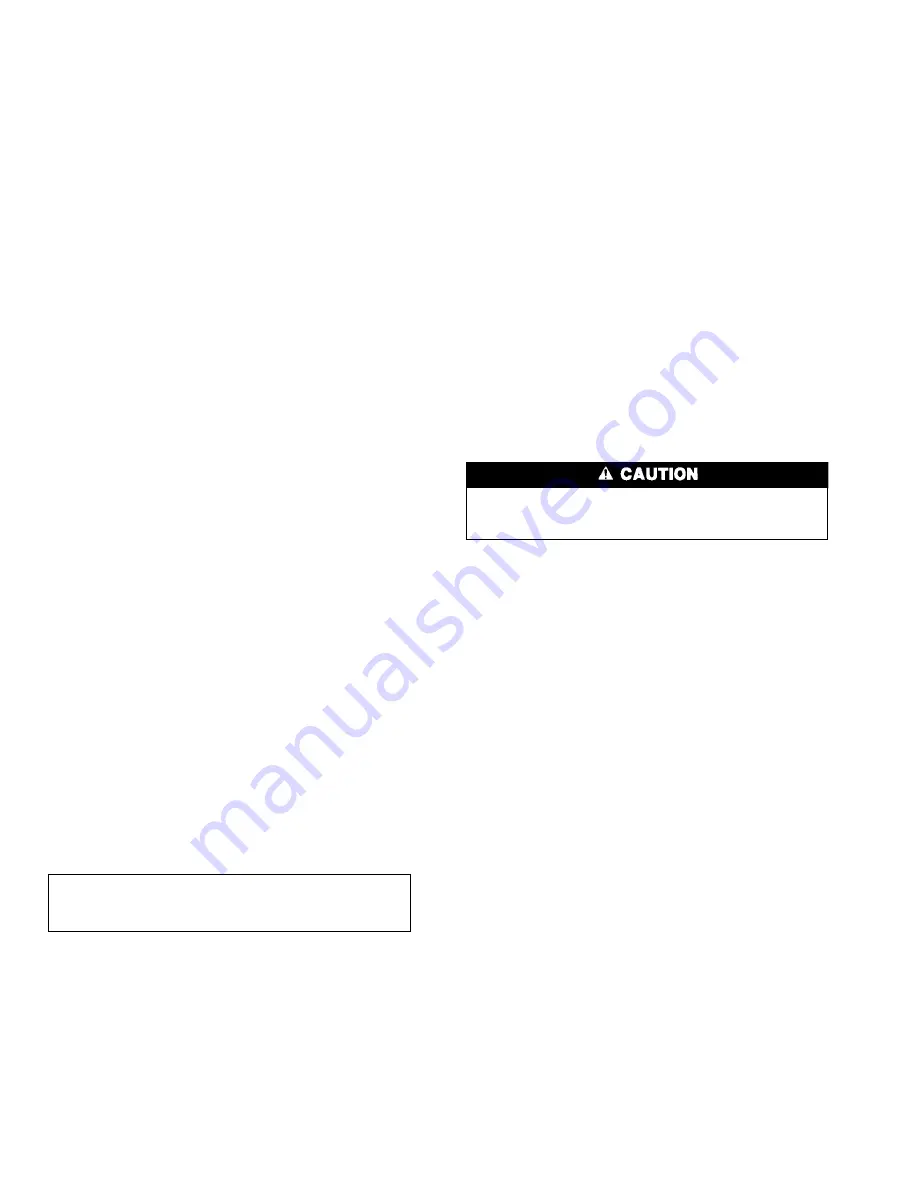
OPEN-DRIVE MACHINES (17 SERIES)
LUBRICATION CYCLE
Summary —
The main oil pump and oil reservoir are
contained in the compressor base. Oil is pumped through an
oil cooler and a filter to remove heat and any foreign par-
ticles. A portion of the oil is then directed to shaft-end bear-
ing and the shaft seal. The balance of the oil lubricates the
compressor transmission and the thrust and journal bear-
ings. The bearing and transmission oil returns directly to the
reservoir to complete the cycle. Contact-seal oil leakage, how-
ever, is collected in an atmospheric float chamber to be pumped
back to the main reservoir as the oil accumulates.
Details (See Fig. 6) —
Oil may be charged into the
reservoir (1) through a hand valve (2) which also functions
as an oil drain. If there is refrigerant in the machine, how-
ever, a hand pump will be required for charging at this
connection.
An oil-charging elbow (Item 20) on the seal-oil return cham-
ber allows oil to be added without pumping. The seal-oil re-
turn pump (Item 21) automatically transfers the oil to the
main reservoir. Sight glasses (Item 6) on the reservoir wall
permit observation of the oil level.
A motor-driven oil pump (Item 5) discharges oil to an oil
cooler (Item 7) at a rate and pressure controlled by an oil
regulator (Item 4). The differential oil pressure (bearing sup-
ply versus oil reservoir) is registered on the control panel.
Water flow through the oil cooler is manually adjusted by
a plug valve (Item 8) to maintain the oil at an operating tem-
perature of approximately 145 F (63 C). During shutdown,
the oil temperature is also maintained at 150 to 160 F (65 to
71 C) by an immersion heater (Item 3) in order to minimize
absorption of refrigerant by the oil.
Upon leaving the oil cooler, the oil is filtered (11) and a
portion is directed to the seal-end bearing (17) and the shaft
seal (18). The remainder lubricates the compressor trans-
mission (15) and the thrust and journal bearings (10). Thrust
bearing temperature is indicated by the PIC controls. Oil from
both circuits returns by gravity to the reservoir.
A demister (13 and 16), by centrifugal action, draws re-
frigerant gas from the transmission area to a housing that is
vented to the cooler (Item 19). The resulting pressure dif-
ference prevents oil from the transmission cavity from pass-
ing through the transmission shaft labyrinth into the demis-
ter outlet chamber.
The open compressor drive requires that the shaft seal (18)
be kept full of lubrication oil, even when the machine is not
operating, to prevent loss of refrigerant.
If the machine is not operating and the oil pump has not
operated during the last 12 hours, the control system will
automatically run the oil pump for one minute in order to
keep the contact seal filled with oil.
IMPORTANT: If the control power is to be deener-
gized for more than one day, the machine refrigerant
should be pumped over to the utility vessel.
STARTERS
All starters, whether supplied by Carrier or the customer,
must meet Carrier Starter Specification Z-375. This speci-
fication can be obtained from the Carrier Sales Representa-
tive. The purpose of this specification is to ensure the com-
patibility of the starter and the machine. Many styles of
compatible starters are available, including solid-state start-
ers, autotransformer, wye-delta closed transition starters, and
full voltage starters.
CONTROLS
Definitions
ANALOG SIGNAL — An analog signal varies in propor-
tion to the monitored source. It quantifies values between
operating limits. (Example: A temperature sensor is an ana-
log device because its resistance changes in proportion to
the temperature, generating many values.)
DIGITAL SIGNAL — A digital (discrete) signal is a 2-position
representation of the value of a monitored source. (Ex-
ample: A switch is a digital device because it only indicates
whether a value is above or below a set point or boundary
by generating an on/off, high/low, or open/closed signal.)
VOLATILE MEMORY — Volatile memory is memory in-
capable of being sustained if power is lost and subsequently
restored.
The memory of the PSIO module is volatile. If the bat-
tery in a module is removed or damaged, all program-
ming will be lost.
General —
The 17/19EX centrifugal liquid chiller con-
tains a microprocessor-based control center that monitors and
controls all operations of the machine. The microprocessor
control system matches the cooling capacity of the machine
to the cooling load while providing state-of-the-art machine
protection. The system controls cooling load within the set
point plus the deadband by sensing the leaving chilled water
or brine temperature, and regulating the inlet guide vane via
a mechanically linked actuator motor. The guide vane is a
variable flow prewhirl assembly that controls the refrigera-
tion effect in the cooler by regulating the amount of refrig-
erant vapor flow into the compressor. An increase in guide
vane opening increases capacity. A decrease in guide vane
opening decreases capacity. Machine protection is provided
by the processor which monitors the digital and analog in-
puts and executes capacity overrides or safety shutdowns, if
required.
12
Содержание 17
Страница 13: ...Fig 6 Open Drive 17 Series Lubrication Cycle 13 ...
Страница 15: ...Fig 7 17EX Controls and Sensor Locations 15 ...
Страница 16: ...Fig 7 17EX Controls and Sensor Locations cont 16 ...
Страница 17: ...Fig 7 17EX Controls and Sensor Locations cont 17 ...
Страница 19: ...Fig 8 19EX Controls and Sensor Locations cont 19 ...
Страница 23: ...Fig 16 17 19EX LID Menu Structure 23 ...
Страница 24: ...Fig 17 17 19EX Service Menu Structure 24 ...
Страница 50: ...Fig 28 17 19EX Leak Test Procedures 50 ...