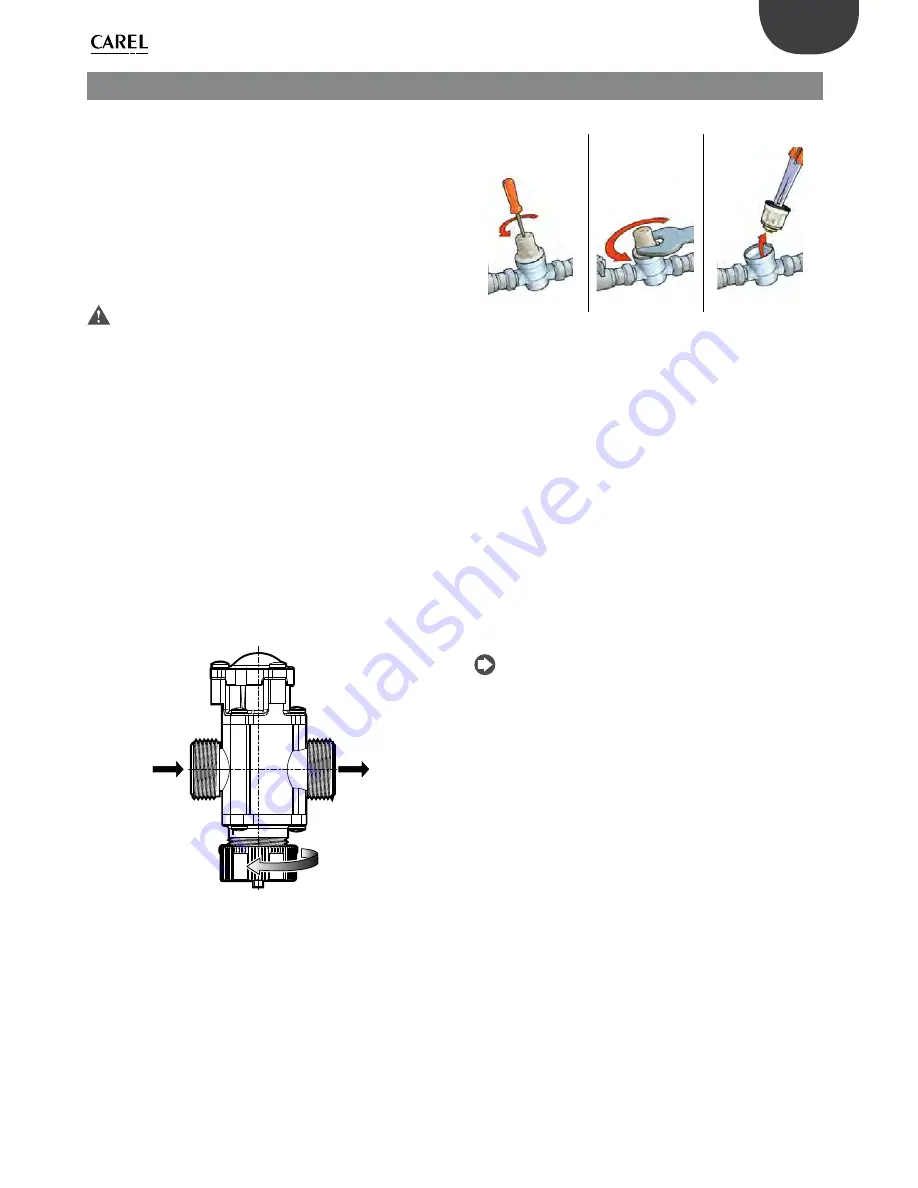
15
ENG
“
kit OEM KEC
” +030222160 - rel. 1.0 - 03/11/2015
3. MAINTENANCE
Maintenance carried out on the KEC at regular intervals will ensure system
performance over time. The checks mostly involve the pumping unit, the
distribution rack in the duct and the droplet separator, if installed, while
the electronics do not need to be checked.
The maintenance intervals mainly depend on the quality of the
feedwater: the higher the quantity of salts and impurities, the more
frequently periodical checks will be required. An initial check should
be carried out three months after starting operation, so as to ascertain
system conditions in relation to the effective number of operating hours,
as shown by the main air-conditioning unit controller. Based on these first
checks, successive routine maintenance operations can be scheduled
accordingly.
Important: before carrying out any maintenance that requires
contact with the components in the KEC water circuit, disconnect
power upstream using the disconnect switch installed in the main
electrical panel.
Cabinet
•
Replace the cartridge on the micron filter upstream of the KEC (at least
every 3 months if using mains water).
•
After closing the shut-off valve upstream of the KEC, check and where
necessary clean the built-in filter on the pressure reducer.
- On units from 50 to 400 L/h, access the filter by unscrewing the cap
underneath the pressure reducer, in the direction indicated by the
arrow, shown in Fig. 3.a.
- On units from 800 to 1000 L/h, the filter is openable from the
pressure reducer inlet. If the filter needs cleaning, proceed as follows:
- unscrew (counting the no. of turns) the calibration screw
anticlockwise until releasing the spring inside (Fig. 3.b);
- unscrew the cover (Fig. 3.c);
- remove the cartridge using a pair of pliers (Fig. 3.d);
- clean the filter that surrounds the cartridge;
- reposition the cartridge, cover and calibrate the pressure reducer
again to 3 bars.
Pressure reducer with filter on 50-400 l/h versions
INGRESSO
INLET
USCITA
OUTLET
Fig. 3.a
Pressure reducer with filter on 800-1000 l/h versions
1
2
3
Fig. 3.b
Fig. 3.c
Fig. 3.d
•
Check and if necessary clean the filter at the fill solenoid valve inlet.
To access the filter, unscrew the plastic nut on the connector, just
upstream of the solenoid valve.
•
Check tightness of the tubing and water fittings in the cabinet.
•
Make sure there are no leaks or dripping from the pump.
•
Check operating pressure on the pressure gauges: with the pump
running, p in ≥ 1.8 bars, p out ≤ 15 bars.
Distribution system
•
Visually check that the nozzles atomise water when the unit is
operating.
•
If necessary, open the head of the nozzle by unscrewing it, and
clean the opening using compressed air. If hard scale is present, after
removing the O-ring, soak the nozzle head in a solution of 20% acetic
acid in water for around 30 minutes. If necessary, replace the nozzles.
•
Check tightness of the compression fittings, and tighten if necessary.
Droplet separator (if installed)
•
Make sure the droplet separator is not blocked, and replace the
modules if necessary.
Note
: The rotary vane pump does not require maintenance. If
necessary, replace the pump when it is no longer able to deliver
pressurised water downstream when all other conditions are equal.